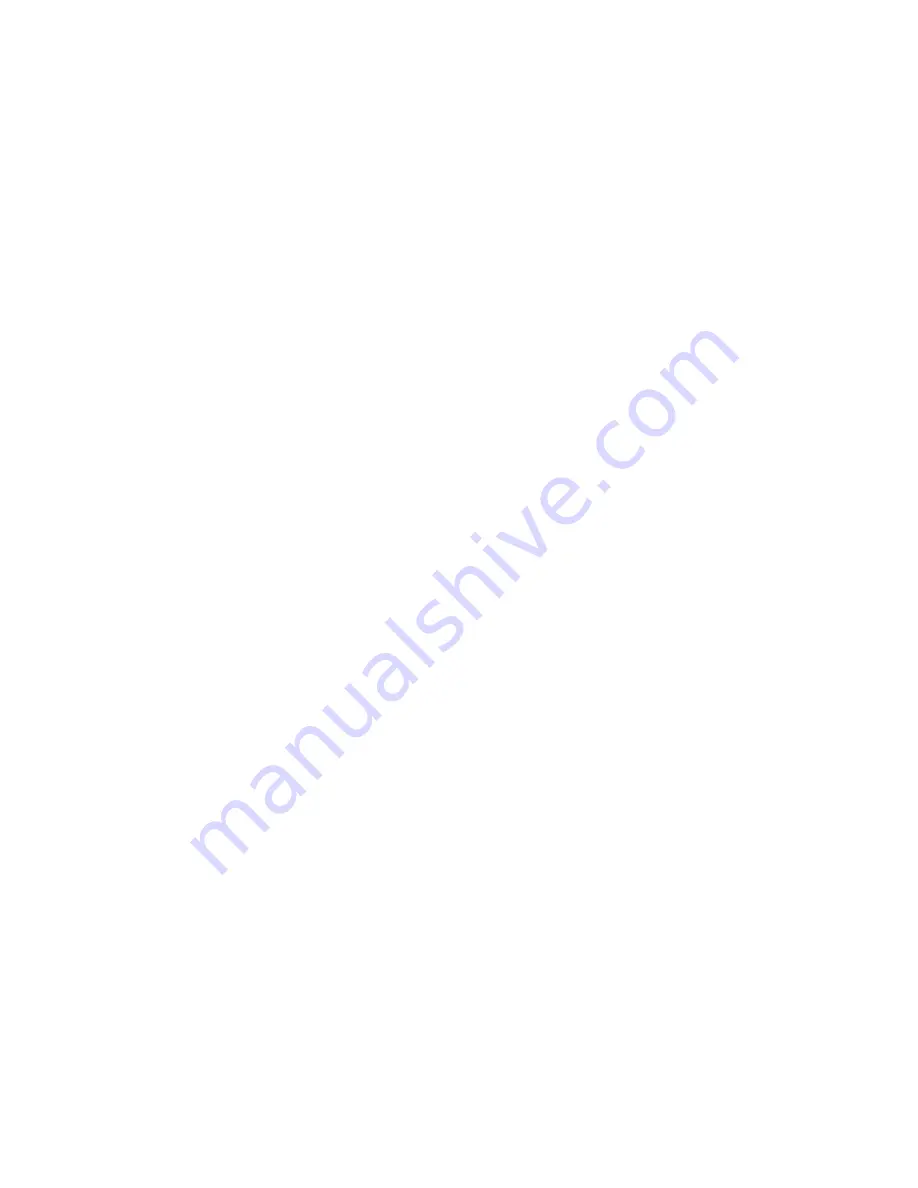
CAUTION: DO NOT OPERATE MACHINE WITHOUT PROPER INSTRUCTIONS.
Observe all safety rules and regulations. Become familiar with controls and intended operation before
using. MACHINE MUST BE SECURELY BOLTED TO FLOOR and connected to correct source of
voltage, phase and cycles.
WARNING:
Electrical danger -- misuse of improper installation of machinery connected to a source of
electricity may result in accidental shock that could cause injury or death. Installation must conform to
National Electric Code (Article 250 - Grounding, etc.) Ground all electrically powered equipment. Ma-
chine to be operated by qualified personnel only.
WARNING: KEEP HANDS AND FINGERS CLEAR OF ROLLS AT ALL TIMES.
Provide point of operation guarding as required to avoid injury. The exact guard needed will be governed
by many factors and may require change when going from one cylinder to another. All required guarding
to be installed and effective before using. Some of the factors involved are: Diameter of cylinder, length
of cylinder, type and gauge of material, direction of feed, number of passes through rolls, etc. Do not
allow clothing or any part of the body (fingers, hands, arms, hair, etc.) to come in contact with the rolls
while the machine is operating. Do not use machine if servicing is required. Use safety glasses and
protective tools when required. Never adjust machine with power on. Be alert to all potential hazards.
Roll Forming Machines are intended for forming a flat sheet of metal into cylinders of various diameters.
Capacity ratings given are based on forming annealed mild steel the full length of the rolls. Definite
capacities depend upon the diameter and length of cylinder to be formed and the number of passes
through the rolls to obtain the desired diameter of cylinder. Stiffness of material and uniformity desired
are factors that must also be considered. When a Roll Forming Machine is overloaded, there will be
excessive deflection at the center of the rolls resulting in cylinders that are bulged in the center.
Become familiar with the location and operation of all controls before using machine. Electrical require-
ments (voltage, phase and frequency) are indicated on the disconnect box and connection to the correct
power source should be made and checked by a qualified electrician.
WARNING
: Electrical danger -- misuse or improper installation of machinery connected to a source of
electricity may result in accidental shock that could cause injury or death. Installation must conform to
National Electric Code (Article 250 - Grounding, etc.) The Roll Forming Machine electrics include a
control panel, forward and reversing relays, brake, and footswitch. The control panel is located on the left
hand housing as shown in Figure 3. A close-up of the control panel is shown in Figure 6.
7