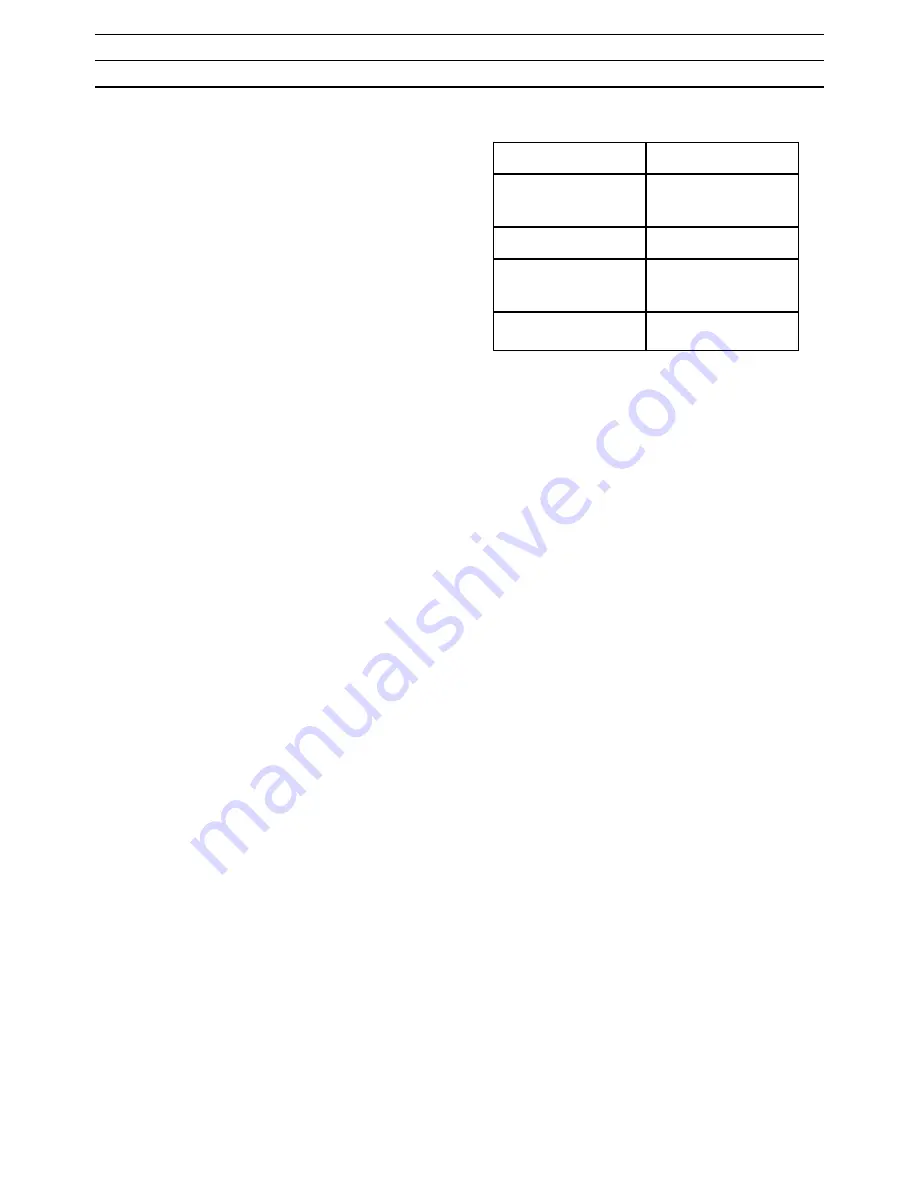
5
012208
5.0 INSTALLATION AND ELECTRICAL
CONNECTION—GENERAL
All equipment manufactured by Ronan Engineering is
carefully packaged and shipped to prevent damage. Any
discrepancies between shipping contents and invoice
should be immediately reported to Ronan or the Ronan
representative.
All Series X90 system components (source holder,
integral switch and remote tube assembly) will tolerate
normal industrial vibration. However, in cases where
vibrators are attached directly to the vessel, the system
components must be mounted on adjacent building
framework or use special supports that provide a degree
of isolation.
When the axis of the detector is placed parallel to the
surface of the process material and its side-facing
source, relay contact changeover will be obtained when
the set limit is exceeded by about one-half inch. When a
level limit is appropriate, a broad band of about five
inches can be obtained by placing the detector axis
perpendicular to the surface of the process material. In
either case, an alarm is produced after the tube is
obscured from (or exposed to) the radiation from the
source.
Whenever possible, separate power sources should be
used for the X90 and the alarm circuit. With this
arrangement, the alarm will operate if the power to the
X90 is interrupted (provided, of course, the alarm circuit
has power available).
Local electrical codes must be followed for all wiring. All
conduit entrances should be sealed to prevent
condensed moisture or water from entering the
enclosures. The cable used to connect the remote
detector should also be run through conduit. All
explosion-proof housing covers must be replaced when
the system is in operation.
6.0 SETUP
Normal setup by the user involves setting two (2) jumper
Options on the switch. The first is the High/Low Level
Alarm. The second is the Buildup Alarm enable. The
jumper must be set to
Enabled
or
Disabled
depending
upon the application. Note that if the jumper for Alarm is
set to Low Level Alarm, the Buildup Alarm will be
disabled regardless of the jumper setting. The standard
(or custom) parameters will already have been
programmed into the unit at the factory. The user must
then mount and wire to the switch. Once a reference is
performed, the switch is ready to use.
The on board dip switch settings are defined as follows:
7.0 CALIBRATION CONTROLS
The following front-panel controls are used in the set-
up procedures :
Start Reference Push Button
is pushed to start the
referencing of the switch on an empty vessel.
Reference in Process LED
indicates a referencing is
occurring.
Normal LED
indicates the switch is in normal opera-
tion.
Fail Alarm LED
indicates any equipment problems.
Level Alarm LED
indicates process alarm states.
Push to Test Button
is used to test hardware.
Communication Port is used to
connect hand held
programmer for detail setup (optional).
Calibration should be attempted only after all system
components have been securely mounted in position
with power and other connections made where re-
quired.
7.1 Referencing
A local or remote pushbutton can be used to refer-
ence the switch. The remote
Reference
pushbutton
can be mounted up to 1000 feet away from the
switch. When the
Reference
input is held for 5 sec-
onds, the
Reference LED
will indicate that the
Refer-
encing
is in process. Once the
Reference
has been
completed, the
Reference LED
will be extinguished.
If a detector failure occurs during referencing, the
Reference LED
will flash rapidly for 5 seconds to indi-
cate the condition.
7.2 Push-to-Test Function
A second pushbutton (local only) is available as a
Push-to-Test Function. This pushbutton will “short
Switch Position
Function
1-5
Device Address (0-31) for
multi-drop communications
access.
6
Not Used
7
Level Alarm Mode:
On=High Level/Off= Low
Level Alarm
8
Buildup alarm Mode: On=
Enabled/Off=Disabled