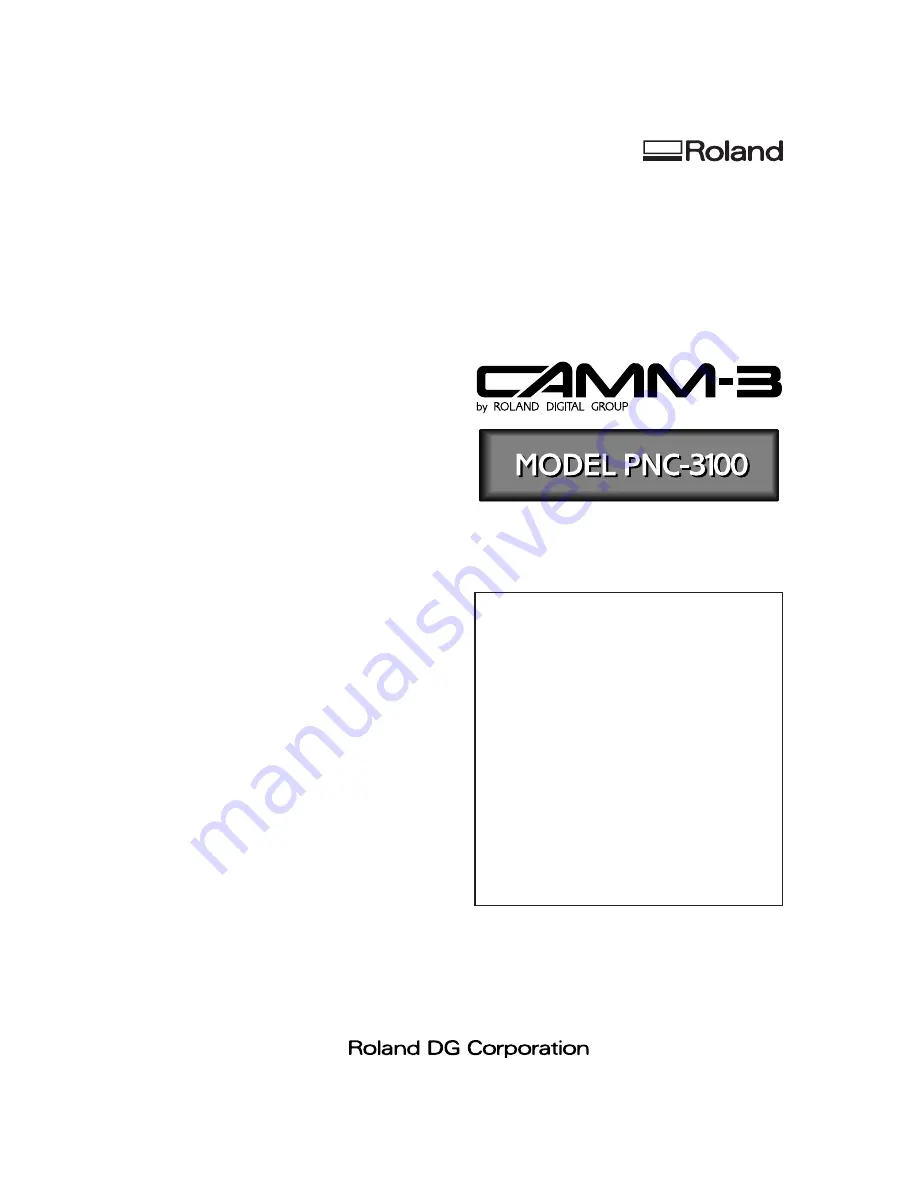
User's Manual
Thank you very much for purchasing the CAMM-3
Model PNC-3100.
• To ensure correct and safe usage with a full under-
standing of this product's performance, please be sure
to read through this manual completely and store it in
a safe location.
• Unauthorized copying or transferral, in whole or in
part, of this manual is prohibited.
• The contents of this operation manual and the
specifications of this product are subject to change
without notice.
• The operation manual and the product have been
prepared and tested as much as possible. If you find
any misprint or error, please inform us.
Summary of Contents for PNC-3100 CAMM-3
Page 54: ...Appendix 44 MEMO ...