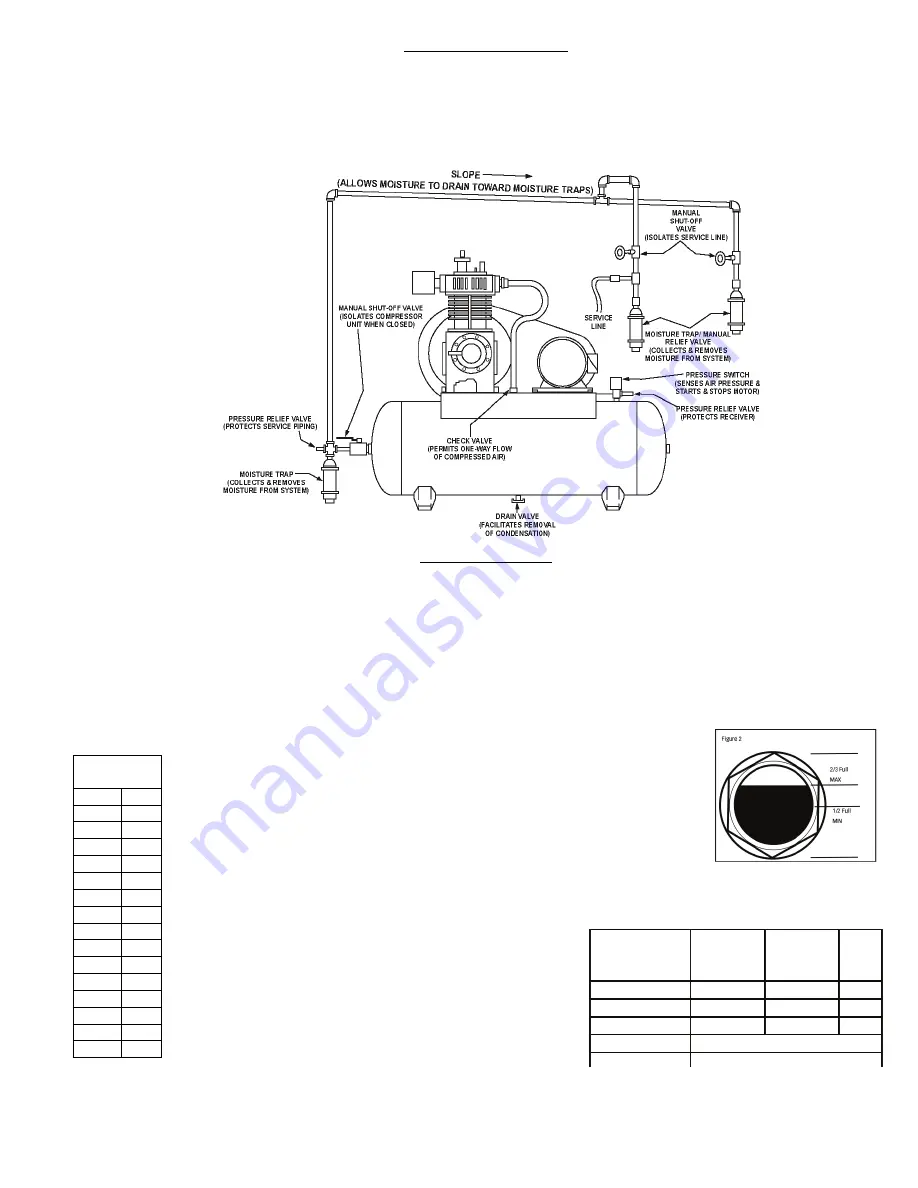
Proper Oil Level:
INSTALLATION
(con’t)
PIPING:
The compressed air distribution system should be of sufficient pipe size to keep the pressure drop between the
supply and point of use to a minimum. All piping should be sloped to an accessible drain-point. Outlets should be
taken from top of mainline so that moisture will not enter the outlet.
OPERATION
LUBRICATION:
Prior to daily operation, make a habit of checking the oil level in your compressor pump. A sight gauge on the outside
of the pump’s crankcase is provided to make the job easier. Always maintain the oil level to read 2/3 full on the sight
gauge. Oil levels over this amount will result in oil blowing past the rings or out of the crankcase breather. Lower
amounts of oil will result in insufficient lubrication of moving parts.
Reciprocating compressors will consume a certain amount of oil under normal operation. If you are concerned about
your oil consumption, monitor and record oil consumption daily and consult your local dealer. When filling your
crankcase with oil, be sure to use a single viscosity, non-detergent oil. DO NOT USE A
DETERGENT OIL!!
Check the oil before starting.
Prior to shipping, complete units are filled with oil and tested. The oil should
be drained and replaced after an initial break-in period of 50 hours.
NOTE: Bare pumps are shipped without oil. See reference charts for oil type
and capacity.
Whether you have purchased a complete unit or bare
pump, check the oil level and correct if needed before
starting each day.
Important: Do not over-fill your pump. It will cause harm.
After break-in period, use a single-grade, non-detergent
motor oil with foam, rust and oxidation inhibitors. For
maximum performance and service life, we recommend
using ROLAIR Premium Quality compressor oil. (See your oil distributor
or representative for compressor oil.)
DO NOT USE DETERGENT OIL!
See chart for oil recommendation in varying temperature conditions.
Oil Capacity
(oz.)
K8 12
K11 17
K12 15
K17 34
K18 34
K22 61
K23 61
K24 61
K25 61
K28 61
K30 47
K35 47
K50 59
K60 98
K70 98
K100 127
Ambient
Temperature
Viscosity
@100°F
SSU
ISO
Viscosity
CS+
SAE
No.
0° - 40°
250-350
46-68
20
40° - 80°
450-550
100
30
80° - 120°
650-750
150
40
Under 0°
Consult Factory
Over 120°
Consult Factory