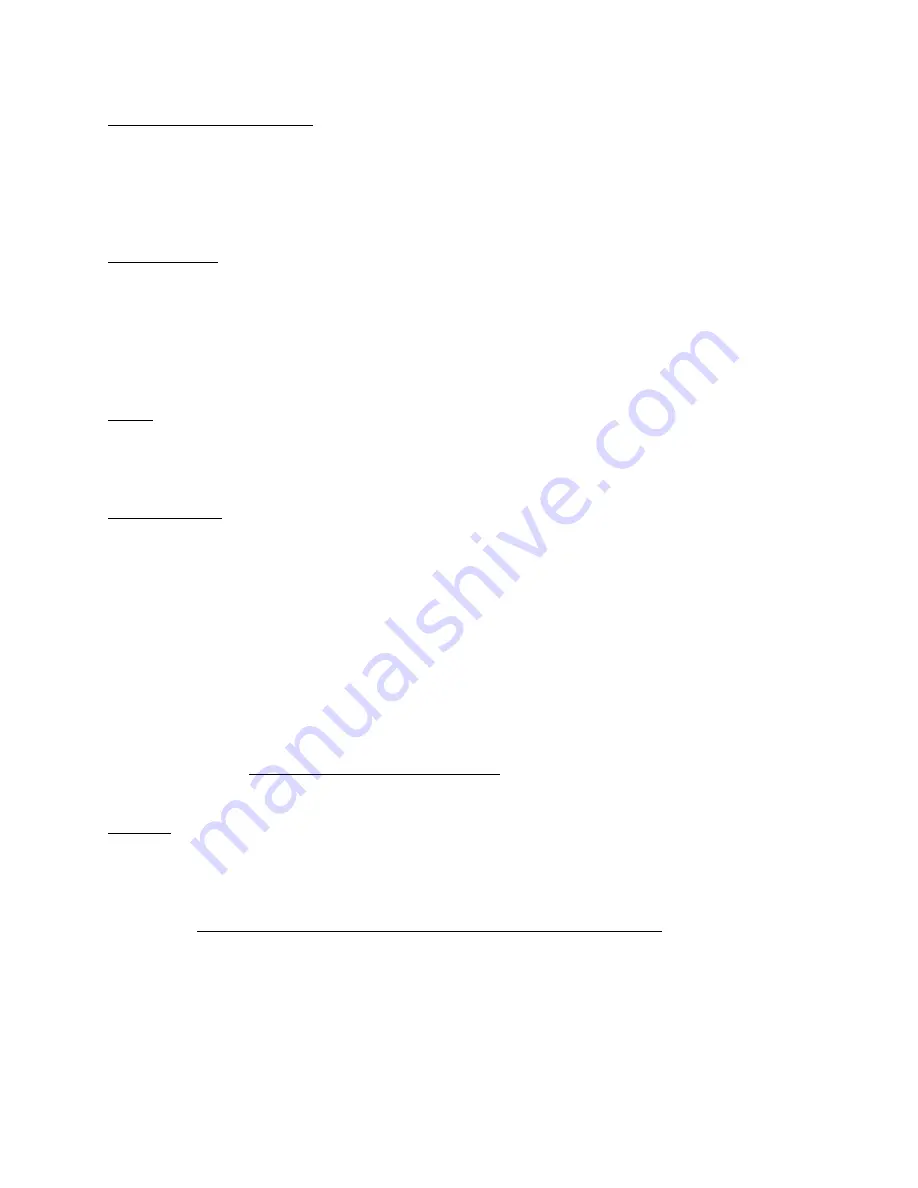
UNPACKING INSTRUCTIONS
Your compressor was inspected at the factory and packaged to protect against shipping
damage. Inspect your unit for damage or missing parts. If any damage occurs or parts are
missing as a result of shipping, a notation to that effect should be made on the Delivery
Receipt. Claims should be settled directly with the transportation company.
LUBRICATION
Prior to initial start-up, fill the crankcase to the designated level with a single viscosity, non-
detergent oil. The oil sight gauge should be filled up to ¾ full. You should be able to see a
small bubble at the top of the sight gauge. Be sure not to fill above the indicated level. DO
NOT USE A DETERGENT OIL! All models are splash lubricated by means of dippers on the
connecting rods. The pump must be operated in a level position for proper lubrication.
BELTS
Install belts on compressor and motor pulleys. Belt tension should be adjusted to allow 3/8”
to ½” deflection with normal thumb pressure.
DRIVE PULLEYS
Drive pulleys must be properly aligned and belt drive tension set to specifications. Improper
pulley alignment and belt tension can cause motor overloading, excessive vibration and
premature belt and/or bearing failure. As the compressor starts, check the rotation of the
flywheel. The direction of the rotation must be counter-clockwise when facing the flywheel.
Should the rotation be incorrect, disengage the power supply and check the motor wiring.
*SPECIAL NOTE: Compressor flywheel has left-hand thread. Remove nut by turning
clockwise.
To determine the correct motor pulley, use the formula below:
Motor Pulley = Flywheel O.D. x Compressor RPM
Motor RPM
GUARDS
Guards should be designed to achieve the required degree of protection and still allow full air
flow from the compressor sheave across the unit. When the compressor is installed, make
sure the guard side is at least 18” away from a wall to provide adequate cooling of the motor
and pump. DO NOT RUN COMPRESSOR WITHOUT BELT GUARD INSTALLED!