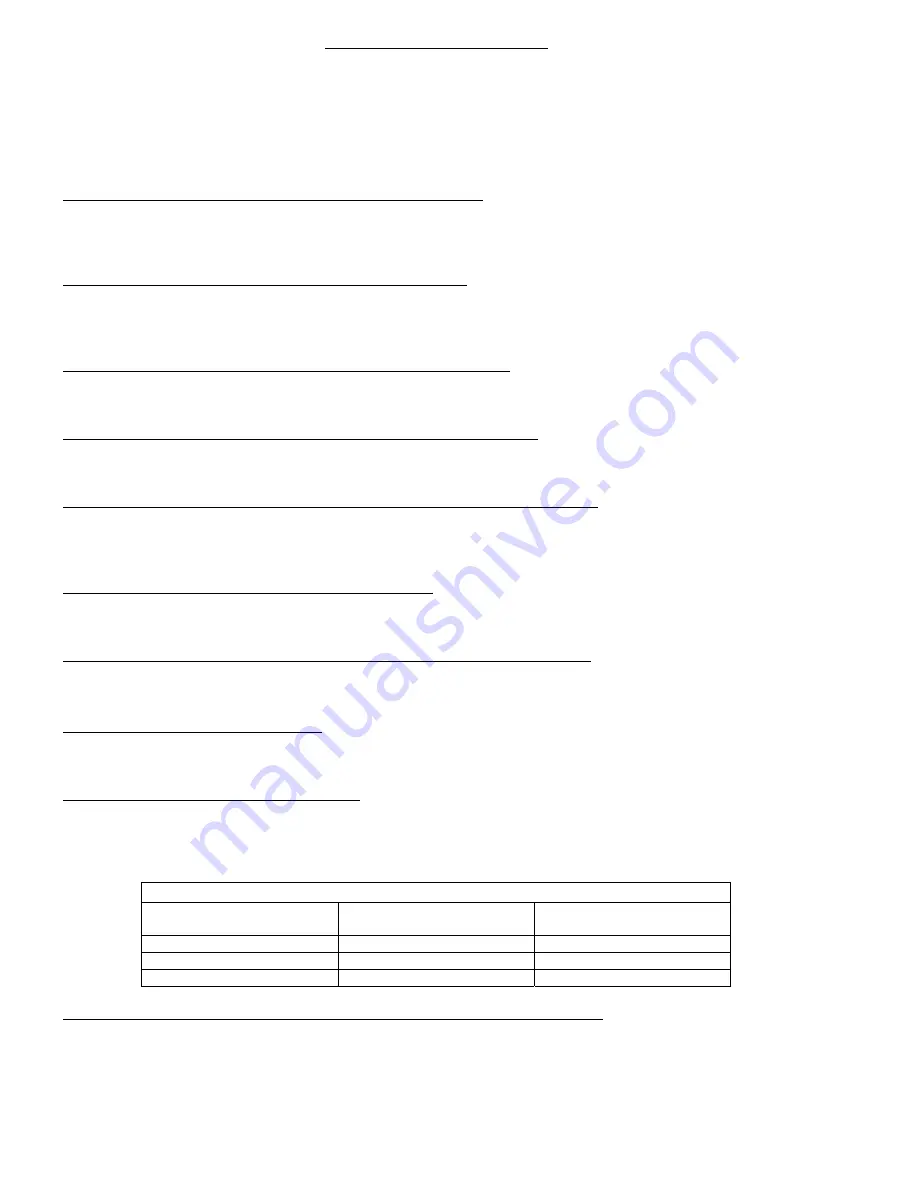
- 8 -
PRE-START CHECKLIST
Read the owner’s manual thoroughly. Make sure that you completely understand all of the safety warnings,
system controls and instructions provided before attempting to operate this air compressor. Every effort has been
made to provide you with the information needed to obtain many years of reliable and trouble-free service out of
your new air compressor. It is your responsibility to operate the air compressor properly. To obtain the longest
possible service life from your air compressor you must always keep the following instructions in mind.
1.
ALWAYS OPERATE THE COMPRESSOR IN A LEVEL POSITION
All splash-lubricated pumps have a dipper on the bottom of the connecting rod that must remain submerged in
the oil bath. Operation at more than a 10 degree angle will cause the pump to seize and void the product
warranty
2.
OPERATE IN A CLEAN, DRY AND WELL VENTILATED AREA
Allow at least 18” behind the belt guard for proper cooling of pump from flywheel blast. Do not operate in the rain
or in areas of standing water. Never operate in an area where other gases, fumes or vapors are present which
may become explosive when compressed. Do not operate compressor in an enclosed area.
3.
CHECK OIL LEVEL DAILY AND CHANGE AT REGULAR INTERVALS
Refer to the maintenance section of this owner’s manual for the correct type/weight of oil to use and how often
the oil should be changed. Check oil levels daily.
4.
INSPECT/CLEAN/CHANGE INTAKE ELEMENTS ON A REGULAR BASIS
The ingestion of dirt into the pump and engine is the primary cause of premature wear. Pay special attention to
the intake filters. Check intake filters daily.
5.
USE LONGER, PROPERLY SIZED AIR HOSE RATHER THAN EXTENSION CORDS
If an extension cord must be used, please refer to the chart below for the proper gauge and maximum length that
can be used. The use of inadequately sized air hose will also lead to frictional pressure drops that could affect the
proper performance of your air tools.
6.
DO NOT USE A GENERATOR AS THE POWER SOURCE
Air compressors use inductive motors that require 3-5 times the full-load amp draw to properly start. Most
generators will not provide the wattage needed to properly start this type of electric motor.
7.
CHECK TENSION OF BOLTS, BELTS, AND HARDWARE ON A REGULAR BASIS
Operation of any equipment with loose bolts and/or fittings will lead to excessive vibration
and the premature failure of the compressor system control components.
8.
MAINTAIN RUBBER VIBRATION PADS
Excessive vibration is a major cause of premature compressor failure. Always maintain the rubber vibration pads
located beneath tank assembly. Operation without them will void your warranty.
9.
DRAIN MOISTURE FROM AIR TANKS DAILY
Water is a natural byproduct of compressed air. Drain air tank(s) after each use to combat internal tank corrosion.
Keep drain valve(s) closed if storing compressor for any length of time.
ELECTRIC EXTENSION CORD TABLE
Minimum Wire Size
Extension
Cord Length
Motor
1/2 and 3/4 HP
Motor
1, 1-1/2, and 2 HP
Up to 25 ft.
14 Ga.
12 Ga.
25 – 50 ft.
12 Ga.
10 Ga.
50 – 100 ft.
10 Ga.
8 Ga.
10.
DO NOT ALTER FACTORY RPM SETTINGS ON GAS-POWERED COMPRESSORS. Engine throttle arm is factory set
and locked into position at RPMs that will provide maximum performance, fuel consumption and service life.
Alterations to this setting will void your warranty.
Summary of Contents for 1040HK18
Page 44: ...44 SCHEMATIC FOR VT25BIG...