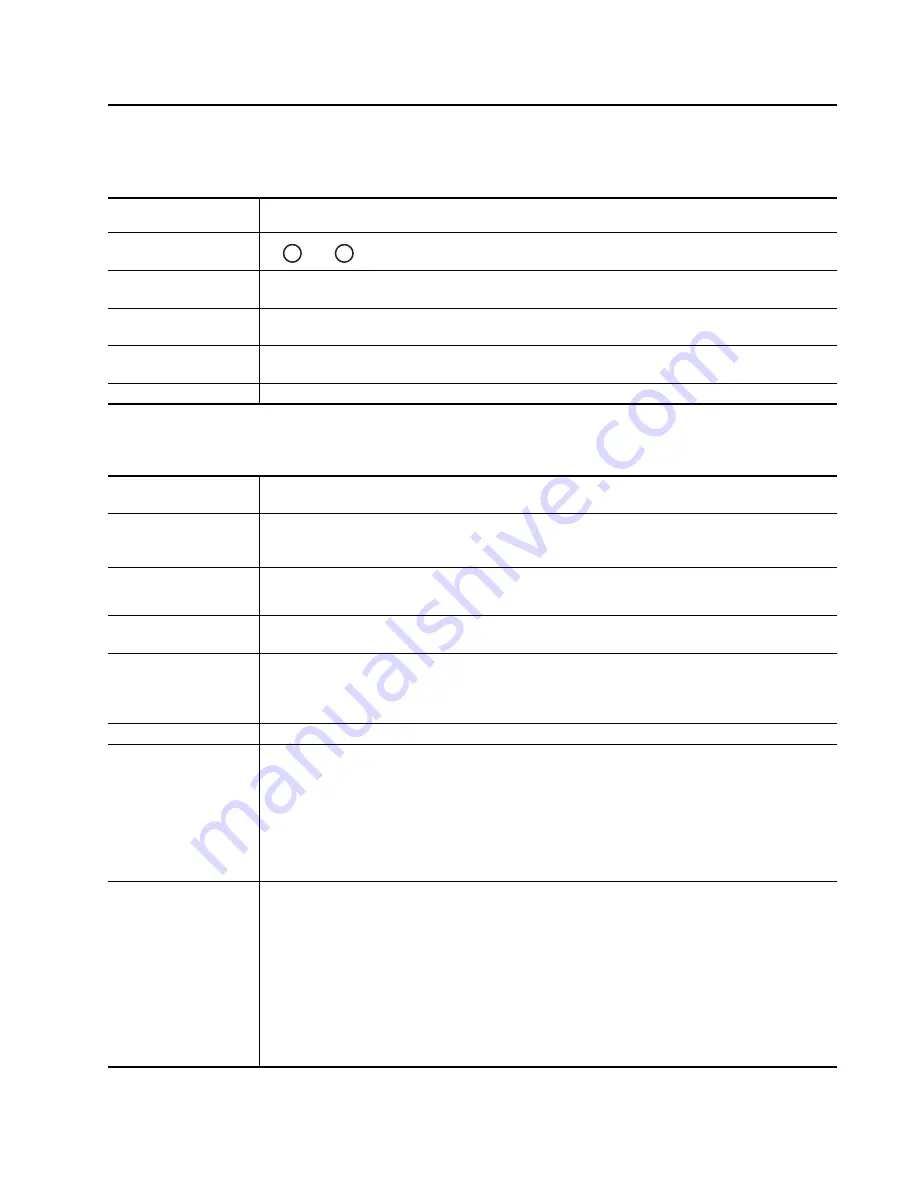
Appendix
A
Specifications
Table A.A Standard Configured Drive Products
Table A.B Standard PowerFlex 40 Drives
Input/Output Ratings
Output Frequency:
0-400 Hz (Programmable)
Efficiency:
97.5% (Typical)
Approvals
Fuses and Power
Disconnecting Means
140M Motor Circuit Protector:
Provides branch circuit protection, 65 kA short circuit withstand
194R Fused Disconnect:
Provides branch circuit protection, 100 kA short circuit withstand, Class J fuses
Protective Features
Over Voltage:
480V AC Input – Trip occurs at 810V DC bus voltage (equivalent to 575V AC incoming line)
Under Voltage:
480V AC Input – Trip occurs at 390V DC bus voltage (equivalent to 275V AC incoming line)
Environment
Ambient Operating Temperature, NEMA 4/12, 4X (IP66):
–10 to 40 degrees C (14 to 104 degrees F)
(1)
Cooling Method:
Fan (All drive ratings)
(1) The design of the PowerFlex 40 Standard Configured Drive NEMA 4/12 and 4X packages support indoor and outdoor applications that are not in direct sunlight.
When optional Door Mounted HIM is supplied, enclosure is rated for indoor use only.
Control
Carrier Frequency:
2-4 kHz. Drive rating and heat calculations are based on 4 kHz.
Digital Control Inputs
(Input Current = 6 mA)
SRC (Source) Mode:
18 – 24 Volts = ON; 0 – 6 Volts = OFF
SNK (Sink) Mode:
0 – 6 Volts = ON; 18 – 24 Volts = OFF
Analog Control Inputs
4-20mA Analog:
250 ohm input impedance
0-10V DC Analog:
100k ohm input impedance
External Pot:
1-10k ohms, 2 Watt minimum
Control Output
Programmable Output (form C relay)
Resistive Rating: 3.0A at 30V DC, 3.0A at 125V AC, 3.0A at 240V AC
Inductive Rating: 0.5A at 30V DC, 0.5A at 125V AC, 0.5A at 240V AC
Opto Outputs
30V DC, 50 mA
Non-inductive
Analog Output (10-bit)
0-10V, 1k ohm Min.
Fuses and Circuit Breakers
Recommended Fuse Type:
UL Class J, CC, T or Type BS88; 600V (550V) or equivalent.
Recommended Circuit Breakers:
HMCP circuit breaker or equivalent.
Protective Features
Motor Protection:
I
2
t overload protection – 150% for 60 Secs, 200% for 3 Secs (Provides Class 10 protection)
Overcurrent:
200% hardware limit, 300% instantaneous fault
Control Ride Through:
Minimum ride through is 0.5 Secs - typical value 2 Secs
Faultless Power Ride Through:
100 milliseconds
Dynamic Braking
Internal brake IGBT included with all ratings
Environment
Altitude:
1000 m (3300 ft) max. without derating
Storage Temperature:
–40 to 85 degrees C (–40 to 185 degrees F)
Atmosphere:
Important:
Drive
must not
be installed in an area where the ambient atmosphere contains
volatile or corrosive gas, vapors or dust. If the drive is not going to be installed for a period of
time, it must be stored in an area where it will not be exposed to a corrosive atmosphere.
Relative Humidity:
0 to 95% non-condensing
Shock (operating):
15G peak for 11ms duration (±1.0ms)
Vibration (operating):
1G peak, 5 to 2000 Hz
Control
Frequency Accuracy
Digital Input:
Within ±0.05% of set output frequency.
Analog Input:
Within 0.5% of maximum output frequency.
Analog Output: ±2% of full scale, 10-bit resolution
Speed Regulation - Open Loop with Slip Compensation:
±2% of base speed across a 40:1 speed range.
1% of base speed across a 60:1 speed range.
Stop Modes:
Multiple programmable stop modes including - Ramp, Coast, DC-Brake, Ramp-to-Hold and S Curve.
Accel/Decel:
Two independently programmable accel and decel times. Each time may be programmed from 0 -
600 seconds in 0.1 second increments.
Intermittent Overload:
150% Overload capability for up to 1 minute; 200% Overload capability for up to 3 seconds
Electronic Motor Overload Protection:
Class 10 protection with speed sensitive response.
UL
®
LIS
TED 966X
IN
D CO NT EQ
UL508C
UL
®
LIS
TED 966X
IN
D CO NT EQ
C
CSA C 22.2 No. 14
Summary of Contents for PowerFlex 40
Page 1: ...INSTALLATION INSTRUCTIONS PowerFlex 40 Configured AC Drives ...
Page 4: ...Publication 23B IN001G 2 Table of Contents Notes ...
Page 29: ...Publication 23B IN001G Control Wiring Overview 2 3 Figure 2 2 Drive Ratings ...
Page 30: ...Publication 23B IN001G 2 4 Control Wiring Overview Figure 2 3 Control Logic Options 4 C D E P ...
Page 31: ...Publication 23B IN001G Control Wiring Overview 2 5 Figure 2 4 Control Logic Option S1 ...
Page 32: ...Publication 23B IN001G 2 6 Control Wiring Overview Figure 2 5 Control Logic Option S1 S8 ...
Page 33: ...Publication 23B IN001G Control Wiring Overview 2 7 Figure 2 6 Control Logic Option S4 ...
Page 34: ...Publication 23B IN001G 2 8 Control Wiring Overview Figure 2 7 Control Logic Option S4 S7 ...
Page 35: ...Publication 23B IN001G Control Wiring Overview 2 9 Figure 2 8 Control Logic Option S4 with S8 ...
Page 36: ...Publication 23B IN001G 2 10 Control Wiring Overview Figure 2 9 Control Logic Option S7 ...
Page 38: ...Publication 23B IN001G 2 12 Control Wiring Overview Figure 2 11 Control Logic Option S8 ...
Page 39: ...Publication 23B IN001G Control Wiring Overview 2 13 Figure 2 12 Control Logic Option S20 ...
Page 40: ...Publication 23B IN001G 2 14 Control Wiring Overview Figure 2 13 Control Logic Option S18 ...
Page 41: ...Publication 23B IN001G Control Wiring Overview 2 15 Figure 2 14 Control Logic Option S21 ...
Page 42: ...Publication 23B IN001G 2 16 Control Wiring Overview Figure 2 15 Control Logic Option S22 ...
Page 43: ...Publication 23B IN001G Control Wiring Overview 2 17 Figure 2 16 Control Logic Option S22 S8 ...
Page 44: ...Publication 23B IN001G 2 18 Control Wiring Overview Figure 2 17 Control Logic Option S23 ...
Page 46: ...Publication 23B IN001G 2 20 Control Wiring Overview Figure 2 19 Control Logic Option R4 ...
Page 48: ...Publication 23B IN001G 2 22 Control Wiring Overview Figure 2 21 Interconnect Wire Parts List ...
Page 56: ...Publication 23B IN001G A 2 Specifications Notes ...
Page 61: ......