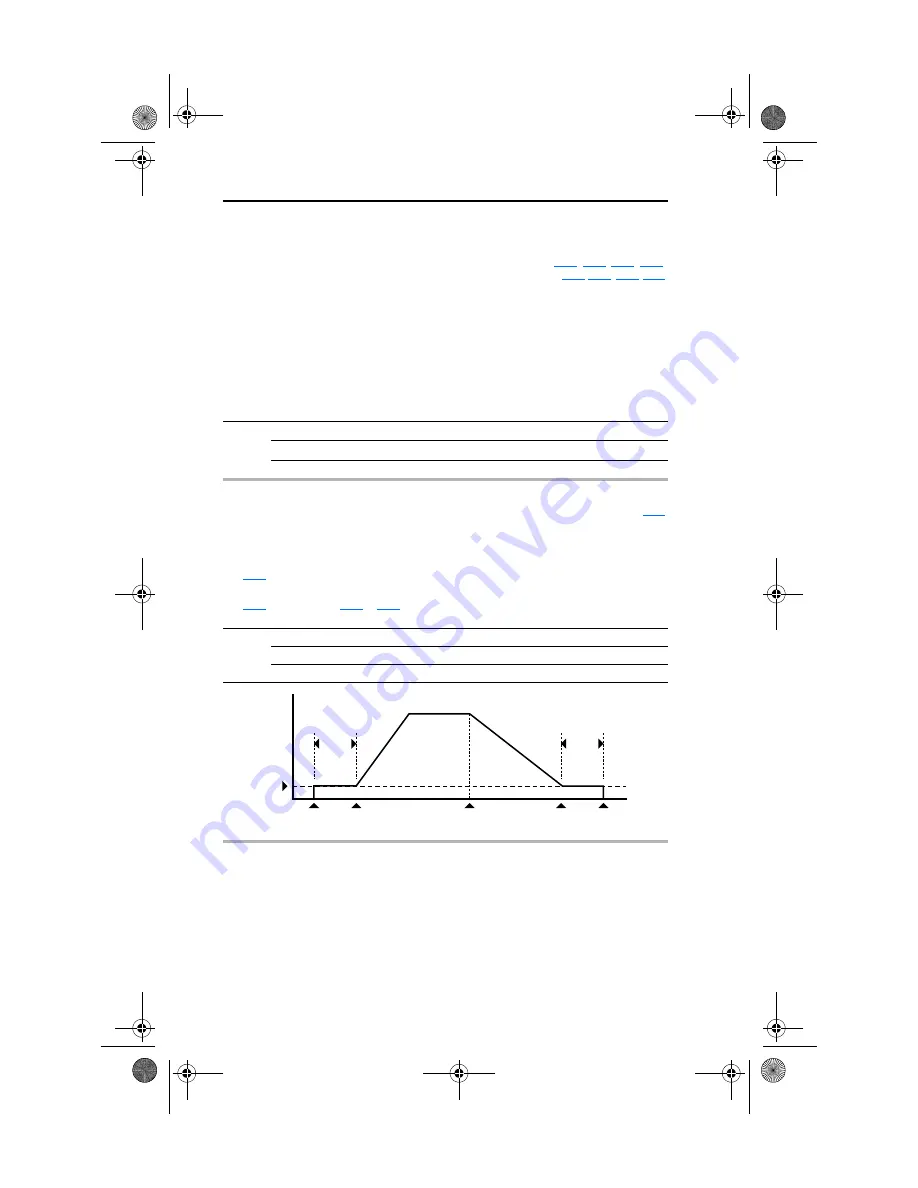
3-42
Programming and Parameters
PowerFlex 40 Adjustable Frequency AC Drive FRN 1.xx - 7.xx User Manual
Publication 22B-UM001I-EN-E
Advanced Program Group
(continued)
A150 [Stp Logic Time 0]
A151 [Stp Logic Time 1]
A152 [Stp Logic Time 2]
A153 [Stp Logic Time 3]
A154 [Stp Logic Time 4]
A155 [Stp Logic Time 5]
A156 [Stp Logic Time 6]
A157 [Stp Logic Time 7]
,
,
-
Sets the time to remain in each step if the corresponding StpLogic command word is set to “Step after
Time”.
Values
Default:
30.0 Secs
Min/Max:
0.0/999.9 Secs
Display:
0.1 Secs
A160 [EM Brk Off Delay]
Related Parameter(s):
Sets the time the drive remains at minimum frequency before the relay or an opto output is energized
and the drive ramps to the commanded frequency.
The relay or opto output is typically connected to a user-supplied electromechanical brake coil relay.
Set
[Stop Mode] to 8 “Ramp+EM B,CF” or 9 “Ramp+EM Brk” to enable the electromechanical
brake option.
Set
[Relay Out Sel],
[Opto Outx Sel] to 22 “EM Brk Cntrl” to control brake
operation.
Values
Default:
2.00 Secs
Min/Max:
0.01/10.00 Secs
Display:
0.01 Secs
Frequency
Time
Minimum Freq
A160 [EM Brk Off Delay]
A161 [EM Brk On Delay]
Stop
Commanded
Start
Commanded
EM Brk
De-Energized (On)
Drive Stops
EM Brk
Energized (Off)
Ramp Accel
Ramp Decel
22B-UM001.book Page 42 Tuesday, May 30, 2017 5:22 PM