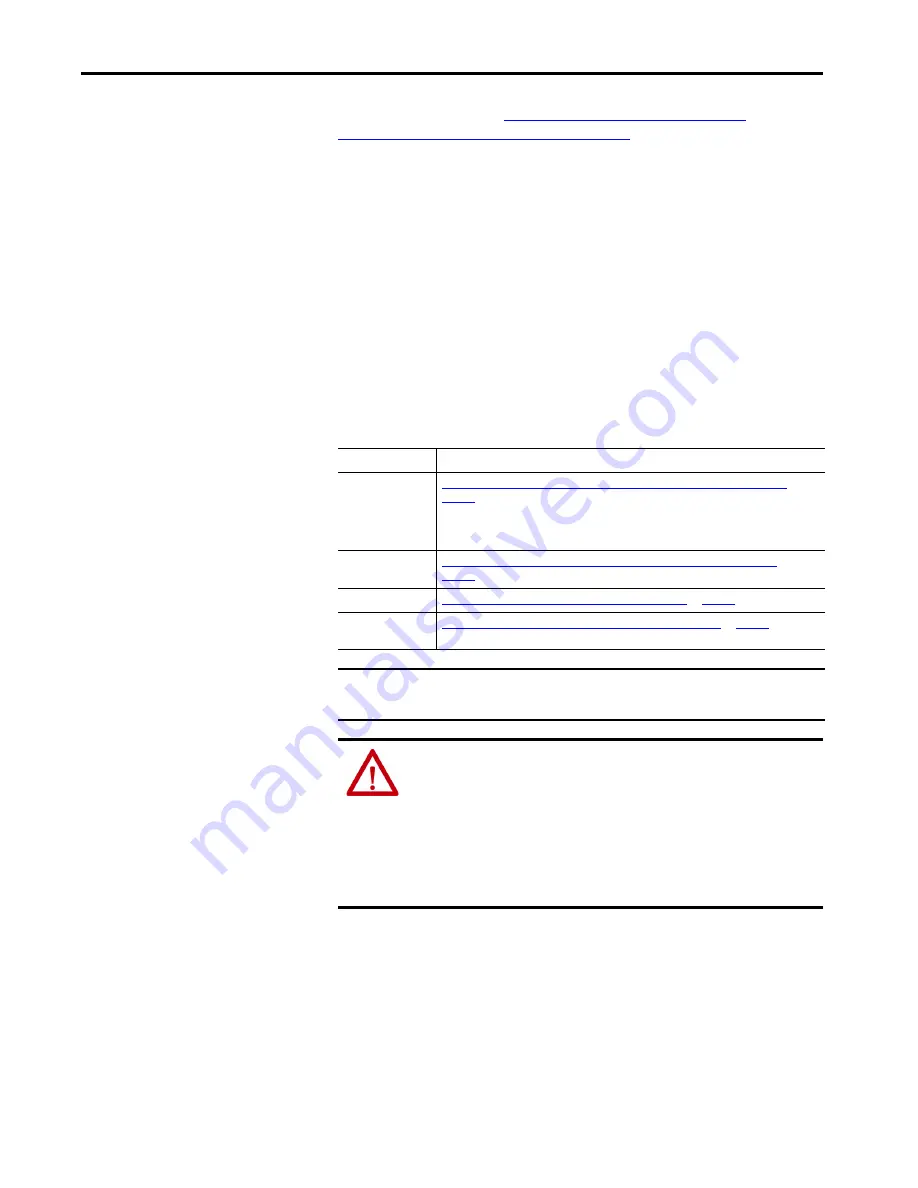
34
Rockwell Automation Publication LDAT-UM001A-EN-P - April 2016
Chapter 4
Commission
http://www.rockwellautomation.com/
rockwellautomation/support/downloads.page?
Contact Technical Support at
(440) 646-5800 for assistance.
Configure Your Linear
Thruster
Configure the linear thruster by using the basic parameter settings that are
described in this section. Use the procedure appropriate for your motion axis.
LDAT-S
xxxxxx-x
B linear thrusters with incremental encoders, are compatible
with all Kinetix drives and have a default resolution of 5 μm.
LDAT-S
xxxxxx-x
D linear thrusters with absolute encoders are only
compatible with Kinetix 300 drives.
The Allen-Bradley drive type that is connected to the linear thruster
determines the configuration procedure. The following table shows you the
configuration procedures to follow.
Positive Motion Direction
Positive motion is defined as the slider extend from the stator body opposite
the power and feedback connectors.
Drive
See:
Kinetix 2000
Kinetix 6000
Kinetix 6200
Ultra3000 with
SERCOS
Configure and Commission Your SERCOS Servo Drive with Logix Designer Application
on
Kinetix 5500
Kinetix 6500
Configure Your Kinetix 6500 or Kinetix 5500 Drive with Logix Designer Application
on
.
Kinetix 300
Configure Your Kinetix 300 Drive with MotionView Software
on
Ultra3000 and
Kinetix 3
Configure Your Ultra3000 or Kinetix 3 Drive with Ultraware Software
on
.
IMPORTANT
Verify that the servo control system safely controls the linear thruster
regarding maximum force, acceleration, and speed.
ATTENTION:
Linear thruster in motion can cause injuries. Before
commissioning the linear thruster, make sure all components are secure and
safe guards are in place to prevent access to motion path.
Safeguards must prevent access to the linear thruster until all motion has
stopped.
Check that the linear thruster is clear of foreign matter and tools. Objects hit
by the moving slider can become projectiles, cause personal injury, or
damage the equipment.