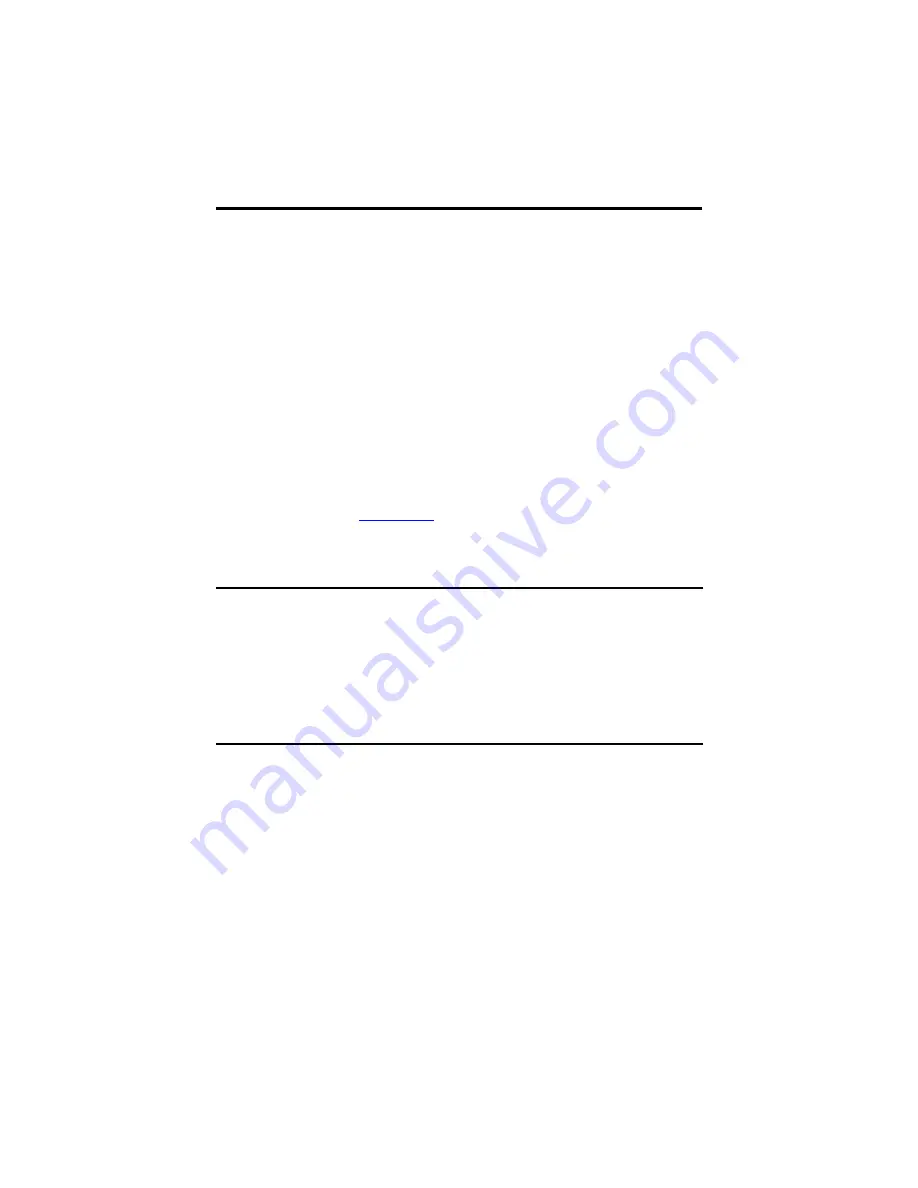
Rockwell Automation Publication VPAR-IN001B-EN-P - February 2019
5
Kinetix VP Electric Cylinders
• Motor feedback, auxiliary feedback, and I/O connector kits are not included, but can be
purchased separately.
• Factory manufactured single cables are available in standard cable lengths. They provide
environmental sealing and shield termination. Contact your Rockwell Automation sales
office or refer to the selection guide for cables.
Electric Cylinders with Brake Option
The brake option on this servo motor is a spring-set holding brake that releases when voltage is
applied to the brake coil. A separate power source is required to disengage the brake. A servo
motor controller or manual operator control can apply the power source.
If system main power fails, holding brakes can withstand occasional use as stopping brakes.
However, the rotational mechanical backlash that is created can potentially damage to the
system, increases brake wear, and reduces brake life.
An unpowered electric cylinder will require a brake to maintain its position if the force on the
actuator exceeds the Back Drive Force that is listed in Kinetix Linear Motion Specifications
Technical Data, publication
A brake can be used to help prevent the actuator from backdriving, typically in vertical
applications. A brake can be used for safety reasons or to hold the position of the actuator when
unpowered for energy savings.
IMPORTANT
Holding brakes are not designed to stop rotation of the motor shaft, nor are they intended to be
used as a safety device. They are designed to hold a motor shaft at 0 rpm for up to the rated
brake holding torque.
The recommended method to help prevent the motor shaft from rotation is a four-step process:
1. Command the servo drive to 0 rpm.
2. Verify that the motor is at 0 rpm.
3. Engage the brake.
4. Disable the drive.
A disable drive removes the potential for brake wear that shaft oscillations cause when you have a
poorly tuned servo system.