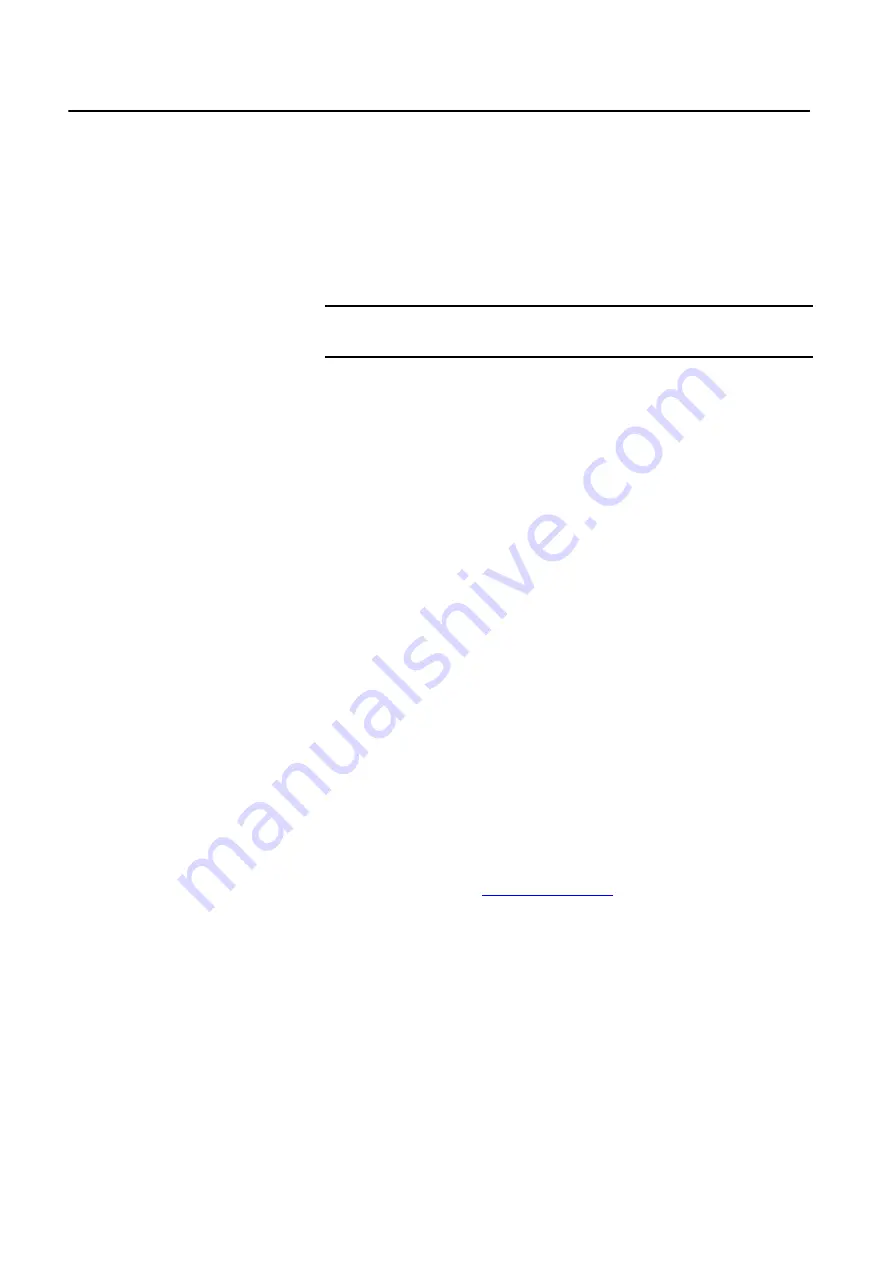
38
Rockwell Automation Publication 440G-UM001C-EN-P - June 2019
Chapter 7
Application Examples
Circuit Status as Shown
The gate is open and unlocked. The motor is off. The GLP is ready for reset.
The GLP has a Logic setting of 3: (Safely-limited Speed with Logic IN OFF), a
Safely-limited Speed (SLS1) setting of 5 (5 Hz) and a maximum (SLS2) speed
setting of 8 (2000 Hz). The safety outputs (X14 & X24), the single wire safety
output (L11), and the auxiliary output (Y32) are OFF.
Starting
Close the gate and press Reset to lock the gate and turn on the GLP safety
outputs. Press Start to turn the motor ON.
Safety-limited Speed
A normal production stop is performed by pressing Stop. Access through the
safety gate is initiated by pressing Gate Unlock Request. The Y32 output of the
GLP turns ON and commands the PowerFlex® drive to bring the motor to a
safe slow speed (Preset Freq 1). When the proximity sensors detect the speed
has dropped below the Safely-limited Speed (5 Hz), the gate becomes
unlocked. The operator can enter the machine cell, as the motor continues to
run at the safe slow speed. After you leave the cell and close the gate, press Reset
to lock the gate and return the machine to production speeds.
The circuit meets the safety requirements up to Category 3, Performance
Leve
l d
in accordance with ISO 13849-1 and SIL CL 2 in accordance with
IEC 62061.
Wiring to GLT Relay
The GLT safety relay is designed to operate with PTR switches. To use a PTL
switch, you must use an interposing relay on the lock command at terminal 51
of the GLP.
In this example shown in
Figure 12 on page 39
, the GLT sends an immediate
command to the drive to turn OFF. After eight seconds, the GLT turns off its
safety outputs and unlocks the gate. The risk assessment must determine
adequate time delay for the machine to achieve a safe state before unlocking the
gate.
IMPORTANT
Start the GLP logic configuration from “0” to configure X14 and X24 for use
as safety outputs.