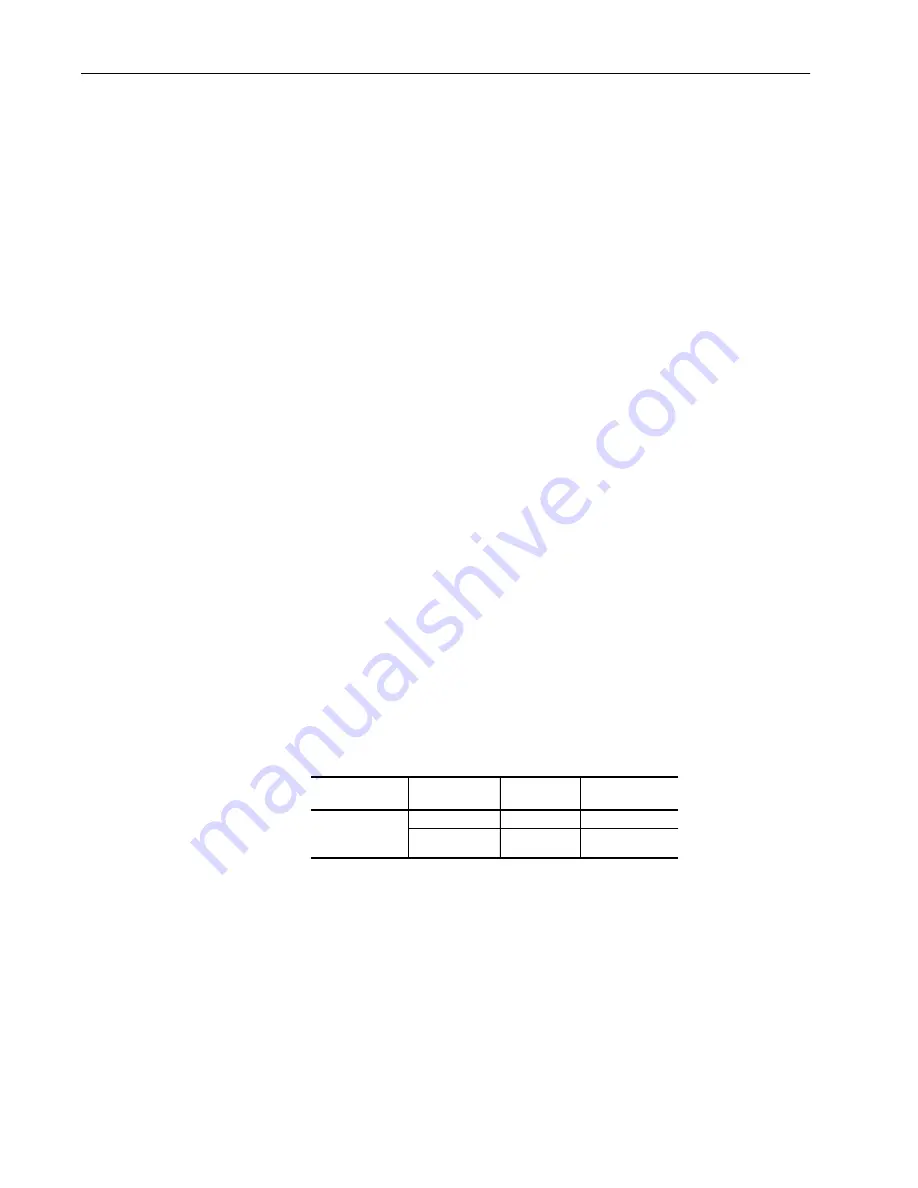
4
DC Motors
Location
Locate the machine where the ambient temperature is not over 40 degrees C
(104 degrees F) and where clean air has free access to ventilating intake and
outlet openings. Except for machines with a suitable protective enclosure,
the location should be clean and dry.
Important:
Sufficient clearance must be provided on all inlet and outlet
openings to provide for unrestricted flow of air. Separately
ventilated motors with exhaust to ambient (pipe-in only) must
have at least 152.4 mm (6 in.) of clearance between the opening
and adjacent walls or floor.
Air Supply
Cooling air through a self-ventilated or forced-ventilated motor must be
clean and have relative humidity between 30 and 100% with no free water
in the air. Use of damp, cool outside air with high humidity and free water
may cause the motor to flash over. Use of excessively dry air may cause
excessive brush and commutator wear. Cooling air temperature must not
exceed the maximum ambient temperature indicated on the motor
nameplate (standard 40 degrees C/104 degrees F). Cooling air temperature
must not be lower than 0 degrees C (to provide base speed and regulation
within NEMA limits). Use of outside air below 0 degrees C may cause
excessive brush and commutator wear due to the low humidity. Cooling air
absolute humidity must be at least 2 grains per cu. ft.
Important:
Motors located in damp, moist environment must have space
heater or fields energized at 50% voltage to protect against
condensation when motor is not operating.
Separately ventilated motors must have the following volume of air to
adequately cool the motor unless the motor nameplate specifies a different
value.
Power Supply
Check the motor nameplate to be sure the voltage and type of power rating
is the same as that of the power source.
A code stamped on the nameplate identifies the type of power supply that
must be used to supply armature power to the motor in order to obtain the
rated nameplate output. Since the code letter has been selected in alphabetic
order of increasing magnitude of ripple current, a motor may be operated on
a power supply having a letter designation prior in the alphabet to the letter
stamped on the nameplate, with no loss in nameplate rating.
Frame
Base Speed
RPM
Air Volume
CFM
Static Pressure
Inches of Water
DC180ATZ,
C180ATZ and
DC210ATZ
2500
152
2.0
1750 and lower
105
0.95