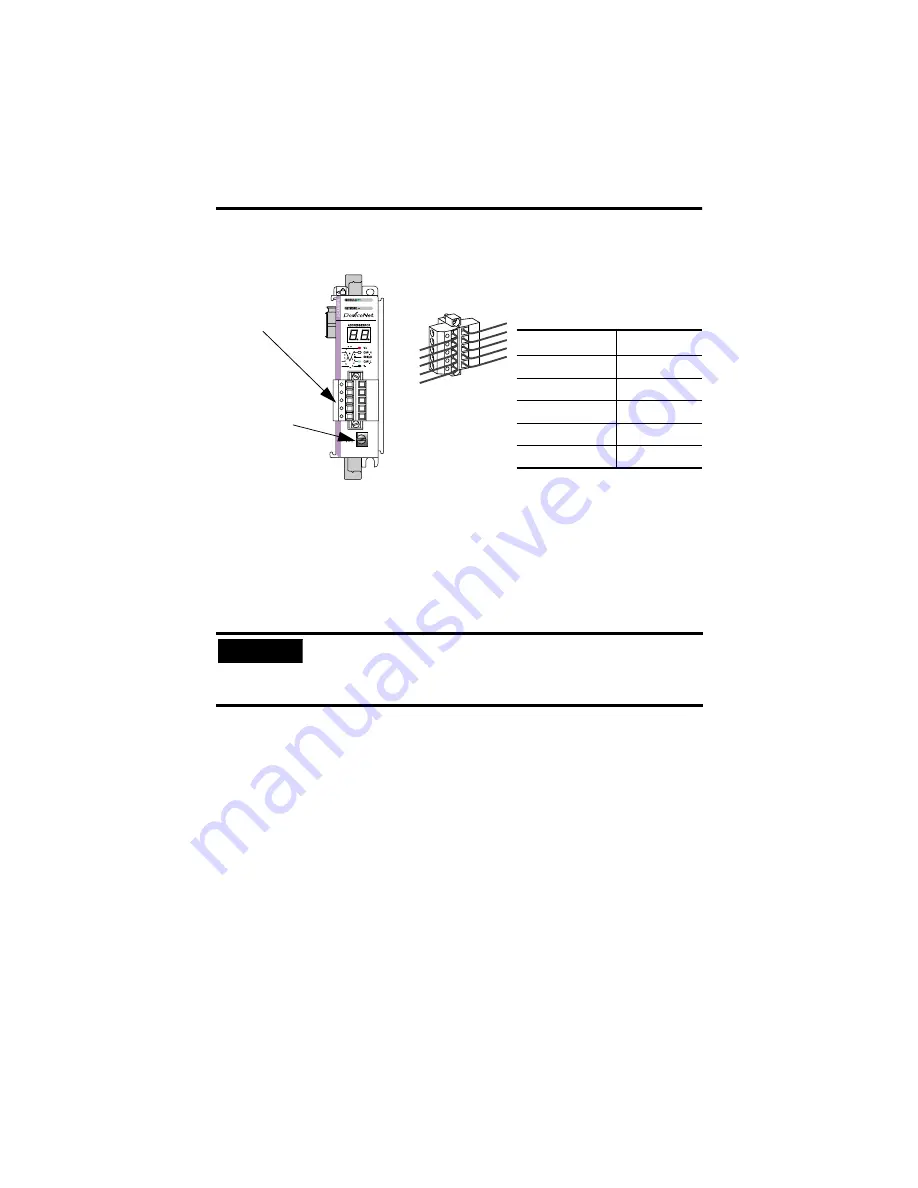
Compact I/O DeviceNet Scanner Module
15
Publication 1769-IN060C-EN-P - May 2002
DeviceNet Wiring
1.
Connect the DeviceNet cable to the removable connector as shown.
2.
Insert the removable female connector into the mating male connector on
the DeviceNet scanner module.
3.
Screw the removable connector to the scanner case with the upper and
lower mounting screws. Screw torque is 0.6 to 0.7 Nm (5 to 6 in-lbs).
Scanner Module Power-Up
When power is applied via the Compact I/O bus, the scanner module goes through
a self test sequence. Upon successful completion of the self test, the scanner is
ready to communicate.
The default scanner settings are:
•
baud rate = 125K
•
node address = 63
Use your configuration software to change the baud rate and node address.
IMPORTANT
If the 1769-SDN is the first or last device connected to the
DeviceNet network trunkline, be sure to add a termination resistor
(120
Ω
1%
≥
¼W resistor, Allen-Bradley part number 1485A-C2)
across the Blue (CAN Low) and White (CAN High) wires.
DeviceNet Connector
Connect
(1)
To
Red Wire
V+
White Wire
CAN High
Bare Wire
Shield
Blue Wire
CAN Low
Black Wire
V-
Grounding Screw
Use #14 AWG wire
to connect to panel
ground.