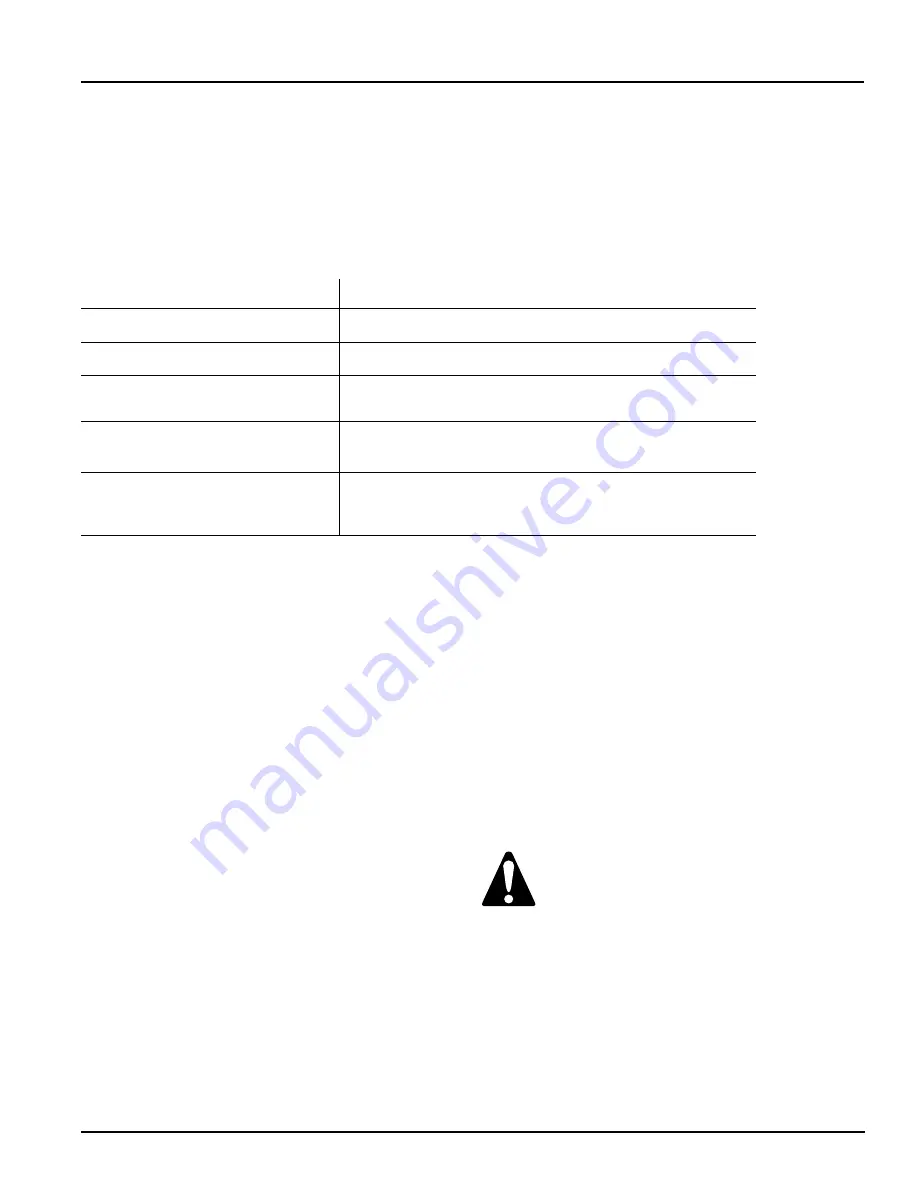
13
Rockford Systems, LLC—www.rockfordsystems.com
Call: 1-800-922-7533
DM
2
Series D Dual-Solenoid Valves
SECTION 6—PRELIMINARY INFORMATION
STARTUP
Before startup, the installation must be checked thoroughly by persons trained and experienced in the operation of pneumatic
equipment. Make sure that specifications given on the valve label (e.g. max. operating pressure and electrical characteristics)
will be in accordance with the operating specifications of the press. When operating pressure is initially applied, it may be
necessary to actuate the reset valve momentarily to move the main valve into the ready-to-run condition. Make sure that the
inlet supply and the exhaust path are not restricted. Operating pressure must comply with the minimum and maximum limits.
FUNCTIONAL TEST
Test
Result
1. Solenoid A actuated
Valve moves into lockout mode, slight leakage at exhaust port 3
2. Solenoid B actuated
Valve moves into lockout mode, slight leakage at exhaust port 3
3. Solenoids A and B actuated with
Valve operates properly
D
t < 0.1 s
4. Solenoids A and B actuated with
Valve moves into lockout mode, slight leakage at exhaust port 3
D
t > 0.1 s
5. After lockout, permanent signal on
Valve cannot be moved into ready-to-run mode
reset valve–solenoids A and B
or only A/only B actuated
PRESSURE TEST
After a valve lockout, the dual-solenoid valve must be moved
into the ready-to-run position by using the reset valve. In gen-
eral, if the valve is in the lockout mode and one or both of the
solenoids are energized, the valve should not reset with applica-
tion or application and removal of the reset signal. If the valve
is in the ready-to-run mode after the reset solenoid valve has
been actuated momentarily, the valve will function normally with
application and removal of pilot solenoid signal. However, if the
valve elements cycle asynchronously, the valve will go to the
lockout mode. Provided that both solenoids are de-energized,
removal of reset signal will return the valve to the ready-to-run
mode.
An additional test to perform:
• With the valve in the ready-to-run mode, exhaust and re-
pressurize the inlet port. The valve should remain in the
ready-to-run mode.
• With the valve in the lockout mode, exhaust and re-pres-
surize the inlet port. The valve should remain in the lockout
mode.
LOCKOUTS
Any asynchronous movement between both piston elements for
a time period > 0.1 s will result in a lockout of the valve. This can
be due to one or more of the various causes below:
• worn piston seals
• delayed response of the main valve elements due to dirt or
varnished lubricant
• electrical signals to solenoid incomplete or unable to main-
tain proper voltage
• independent electrical signals to solenoids are not received
concurrently
• delayed response of solenoid pilots or booster pilots due to
damaged components, dirt, or varnished lubricant
• collection of excessive water or lubrication
MAINTENANCE, TESTING
Maintenance and testing procedures must follow the rules and
regulations set by the respective national work-safety institu-
tions. These procedures should only be performed by persons
trained and experienced in the use of pneumatic equipment.
Regulations generally require that maintenance and test proce-
dures be performed at least once a year.
REPAIR
Rockford Systems, LLC would be happy to service this special-
ized dual-solenoid valve for you at its factory repair center. Call
1-800-922-7533 for information. If you service the valve your-
self, be sure to turn off electrical power to the valve, shut off the
air supply, exhaust the air in the system, and lockout all power
sources before beginning any disassembly operation. Custom-
ers maintaining their own valves should make sure that only
original spare parts are used.
Pneumatic equipment should be repaired only by
persons trained and experienced in the repairing
of such equipment, guided by these operating in-
structions. Information about valve repair and/or
the exchange of a valve must be written down in
the machine operation documentation.