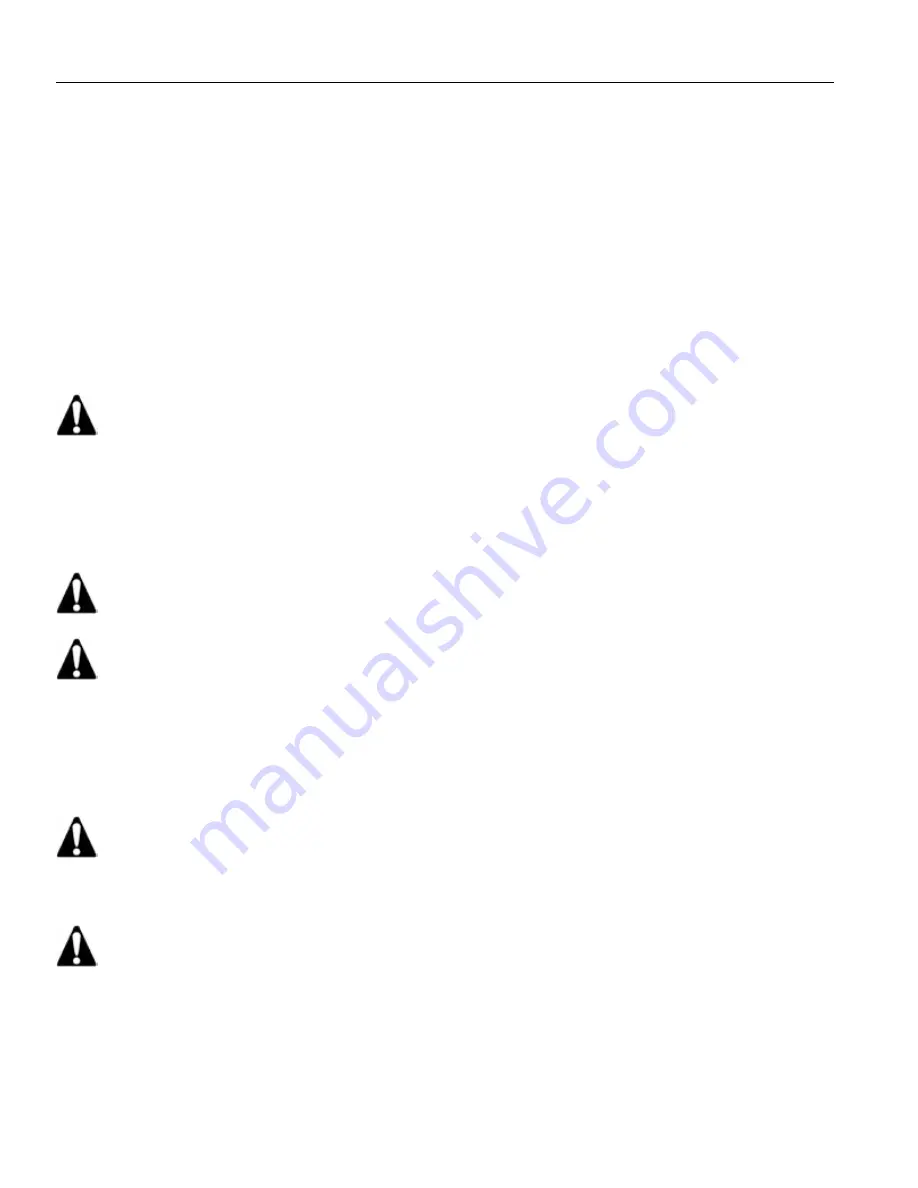
SECTION 2—INSTALLATION OF COMPONENTS
Detect-A-Finger
®
Drop Probe Device-Welder
Rockford Systems, LLC
8
Call 1-800-922-7533
Preliminary Steps Before Installation
Before proceeding with the installation of the enclosed equipment, you should undertake the following preliminary
steps.
1. Read and make sure you understand this entire installation manual.
2. Refer to the front cover, other line drawings and photos, then make a sketch of your installation to plan the location
of the enclosed equipment on the machine.
3. Please make sure the machine is in first-class condition. Before starting any installation, it is essential that
the machine is thoroughly inspected. Be sure all mechanical components and all collateral equipment are in first-
class operating condition. Your inspection should be done according to the machine manufacturer’s installation
and maintenance instruction manual. If you have any doubts or questions concerning the condition of the machine,
contact the machine manufacturer for assistance. Repair or replace all parts not operating properly before
proceeding.
Inspection and maintenance programs must be established and implemented to keep machines in
first-class condition. Safety programs must include thorough inspections of each machine on a weekly
basis and records kept of these inspections. Any part of the machine that is worn, damaged or is not
operating properly must be replaced immediately or repaired before the machine is used.
4. Verify that the machine is in first-class condition and operating properly; shut off all power to the machine. Padlock
all electrical and pneumatic energy in the off position and do not actuate the machine again until the installation of
all package components has been completed. Lockout/tagout energy isolation procedures must always be practiced
and enforced.
The operator must be protected from all hazards. All applicable sections of OSHA Section 1910.212
must be complied with on all machines where this equipment is installed.
The Detect-A-Finger® controls are applicable on most types of resistance welders. The function of the
Detect-A-Finger® device, when properly installed, adjusted and maintained, is to keep the operator from
inadvertently cycling the machine with fingers in the point of operation. This control only provides
an interface between the foot switch and the welder controller which will not allow stroke initiation
unless the area being probed is cleared of all obstructions. To accomplish this protection, the Detect-
A-Finger® must be properly installed on the machine and the device must be properly maintained and
adjusted by the user. A properly designed sensing probe must be used and additional sensing probe
safeguarding must be provided where applicable. This device does not protect the operator if fingers
are placed above the sensing probe.
Before starting any installation work, it is imperative the welder be inspected to exhibit proper operation.
Run the welder in a normal operating sequence to determine proper operation. Do not install the Detect-A-
Finger® on a welder that does not function properly. When the welder is operating satisfactorily, shut off
the power with the disconnect switch and do not operate the welder again until installation is complete.
Use of a lockout device and padlock on the disconnect handle must be used during this period.
The maintenance and inspection section in this manual cannot be all-inclusive for maintaining welders.
Always refer to the original welder manufacturer’s maintenance manuals or owner’s manual. If you do not
have an owner’s manual, please contact the welder manufacturer.
NOTE: The Detect-A-Finger® does not change the operation of the machine. This interface only interrupts the
foot switch signal. If this welder is capable of continuous operation while the foot switch is held, then
an interface will be required to have the sensing probe drop before each cycle of the welder.