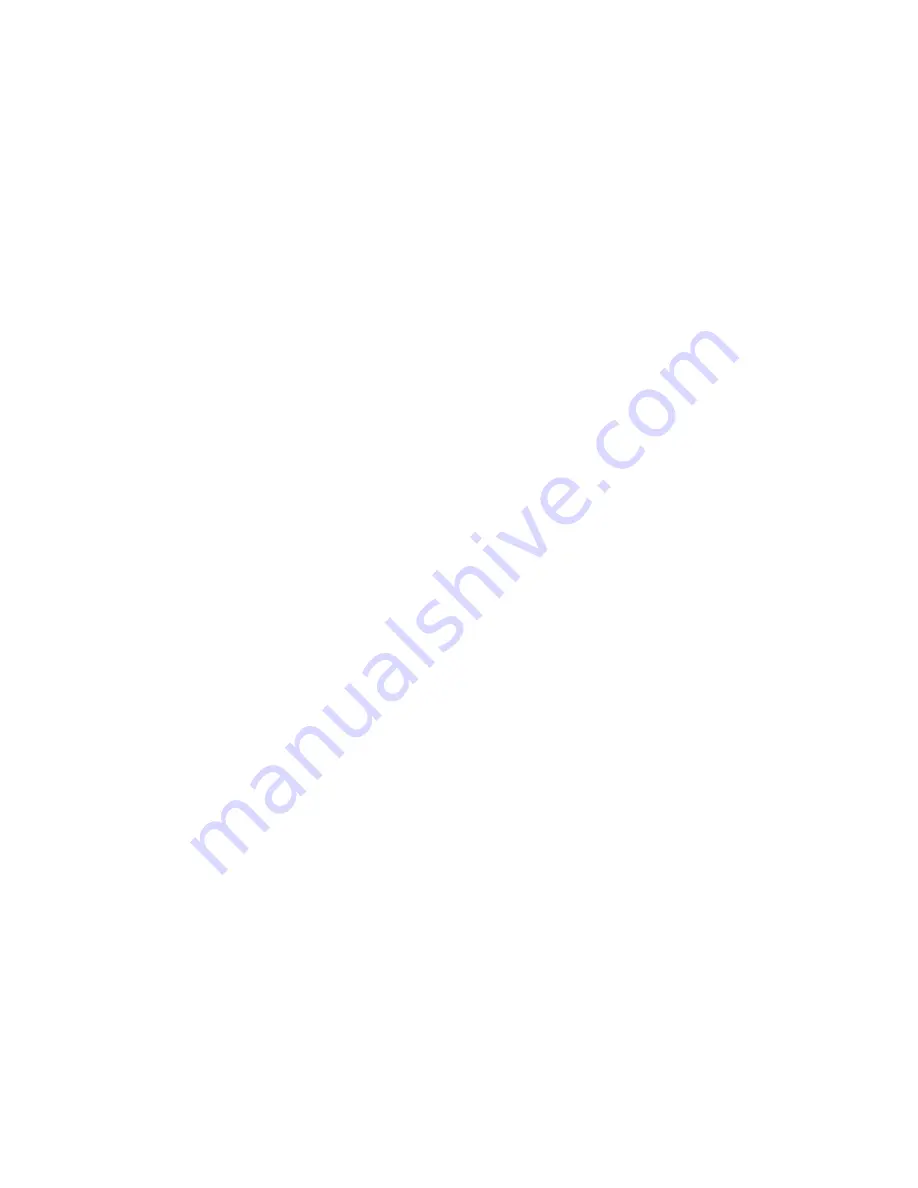
26
Instruction and precautions for
power connection
●
The boiler should not have a plug socket
only a flex
●
Voltage/frequency for the gas boiler:230
V~/50Hz
●
Please obey the following steps when
operate the gas boiler:
-- Do not touch the appliance with parts of the
body that are wet or damp and/or bare feet.
--Do not pull the power cable.
--Do not expose the appliance to direct sun
and rain.
--Do not allow children or inexperienced
people to operate the appliance.
●
User should not change the power cables.
If the power cable has been damage, turn off
the appliance. Ask an installer/engineer to
change the power cable.
●
For electrical safety, please make the
correct earth connection with accordance to
local safety rules.
●
The above safety requirements must be
checked. If you have any questions, please
ask the installer/engineer to check the
appliance carefully. The manufacturer will not
take any responsibility for any losses caused
by not earthing the appliance.
●
Ask the installer/engineer to check the
circuit line, make sure the circuit can match
the maximum power capacity of the appliance.
The maximum capacity is indicated in the
technical section.
●
Please do not use multi plugs, extension
leads or adaptors. Use a two-phase switch
when connecting to the power grid, the
distance between the contact points should
be at least 3mm, which as stipulated in the
current safety rules regulations.