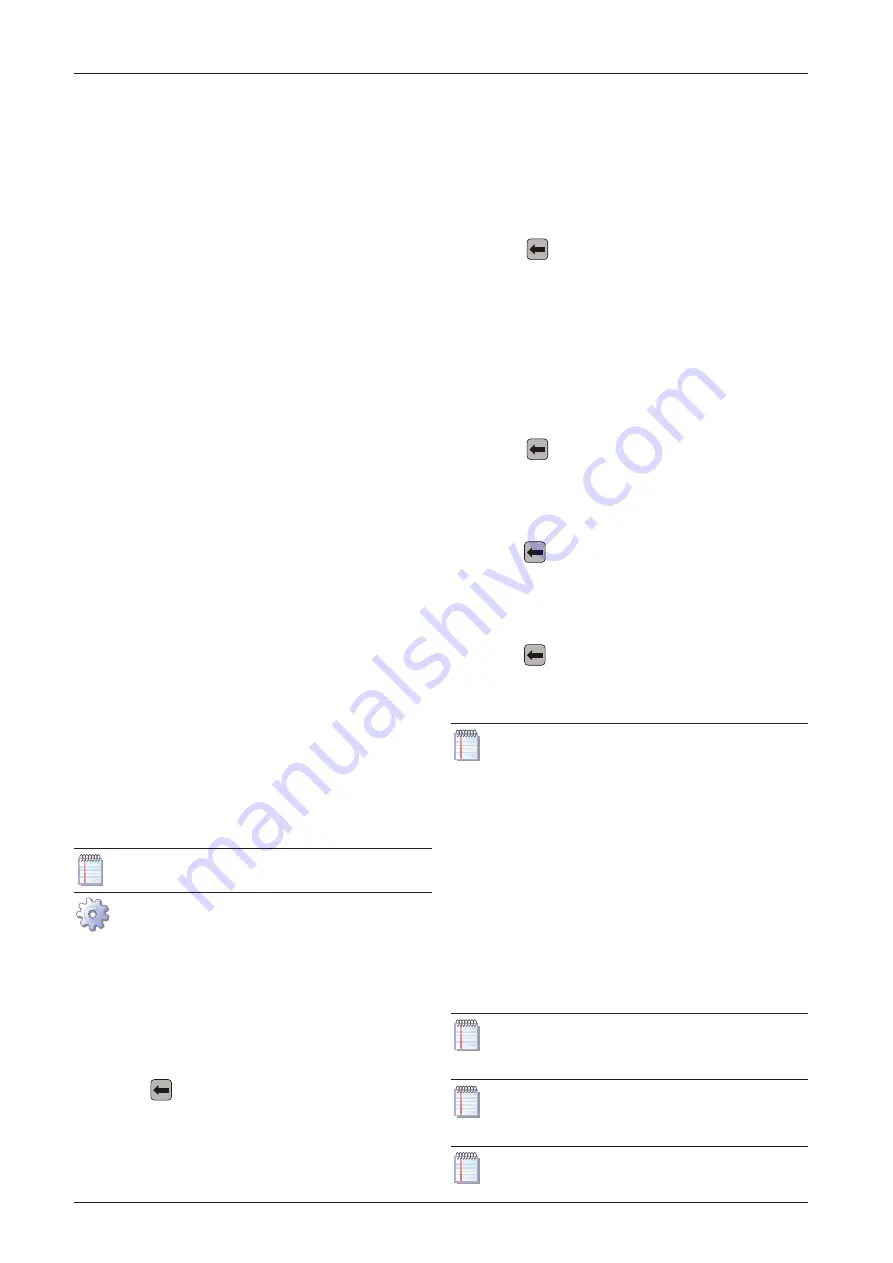
First start-up
Installation, use and maintenance manual – K18 Simplygas
37
5
capacities and equipped with all safety and control devices
required by the regulations in force.
▶
Absence of leaks in the water and gas systems.
▶
Type of gas for which the appliance is designed (natural gas).
▶
Supply gas pressure complying with the values of Table
p. 28, with max tolerance ±15%.
▶
Power supply mains complying with the appliance's rating
plate data.
▶
Appliance correctly installed, according to the manufactur-
er's instructions.
▶
System installed in a workmanlike manner, according to na-
tional and local regulations.
5.1.2
Abnormal or hazardous installation situations
Should any abnormal or hazardous installation situations be
found, the TAC shall not perform first start-up and the appliance
shall not be commissioned.
These situations may be:
▶
Appliance installed inside a room.
▶
Failed compliance with minimum clearances.
▶
Insufficient distance from combustible or flammable mate-
rials.
▶
Conditions that do not warrant access and maintenance in
safety.
▶
Appliance switched on/off with the main switch, instead of
the provided control device (OQLT021, OCDS007, or external
request).
▶
Appliance defects or faults caused during transport or instal-
lation.
▶
Gas smell.
▶
Non-compliant mains gas pressure.
▶
Non-compliant flue gas exhaust.
▶
All situations that may involve operation abnormalities or
are potentially hazardous.
5.1.3
Non-compliant system and corrective actions
Should the TAC find any non conformities, the user/installer is
bound to perform any corrective procedures required by the
TAC.
After performing the remedial actions (the installer's responsi-
bility), if the TAC deems that safety and conformity conditions
are in place, first start-up may be effected.
5.2
COMBUSTION PARAMETERS CHECK
Paragraph reserved exclusively to TACs.
Figure 5.1
1. If the appliance is running, switch it off with the applicable
control system (OQLT021, OCDS007, external request).
2. Remove the cap over the offset adjustment screw (C).
3. Screw in completely the throttle adjustment screw (D).
4. Screw in completely the offset adjustment screw (C).
5. Unscrew the throttle adjustment screw (D) as indicated in
6. Unscrew the offset adjustment screw (C) as indicated in
7. Press the
key on the user interface of the unit (detail B
of Figure 1.9
p. 16) for 5 seconds to activate the chimney
sweep function at minimum power.
8. The display shows the letters "CS.LO" (chimney sweep low
power), alternating with the flashing message "UAIt" (wait)
which indicates that the machine is not yet ready for the
reading.
9. Once an approximate time ranging between 5 and 8 min-
utes elapses, the flashing message becomes "_GO_" to indi-
cate that the combustion control can be implemented.
10. Ensure the CO
2
value is between values indicated in column
"Minimal heat input" of Table 5.1
p. 38. Otherwise set
CO
2
percentage reading by acting on the offset adjustment
screw.
11. Press the
key on the user interface again for 5 seconds
to activate the chimney sweep function at maximum power.
12. The display shows the letters "CS.HI" (chimney sweep high
power), alternating once again with the flashing message
"UAIt" (wait) which indicates that the machine is not yet
ready for the reading.
13. After a short while, the flashing message becomes "_GO_"
again to indicate that the combustion control at maximum
power can be implemented.
14. Ensure the CO
2
value is between values indicated in column
"Nominal heat input" of Table 5.1
If the check is successful:
15. Press the
key on the user interface again for 5 seconds
to deactivate the chimney sweep function and complete the
procedure.
If the check is not successful:
16. Set CO
2
percentage reading by acting on the throttle adjust-
ment screw.
17. Press the
key on the user interface again for 5 seconds to
deactivate the chimney sweep function.
18. Repeat steps 7 to 10 to reactivate the chimney sweep func-
tion at minimum capacity; verify once again and if necessary,
correct the CO
2
value in these conditions by actuating the
offset adjustment screw.
19. Press the
key on the user interface again for 5 seconds to
activate the chimney sweep function at maximum capacity,
and then again for 5 seconds to deactivate it and complete
the procedure.
To ensure the chimney sweep function is executed prop-
erly, there must be adequate thermal load, otherwise the
appliance could reach the maximum limit of the delivery
and/or return temperature and then stop.
The following may be necessary to provide adequate
thermal load, depending on the system characteristics:
Activate any pumps or zone valves of the water distribu-
tion circuit.
Fully open the manual or thermostatic valves, mounted
on the radiators.
Activate the ventilation of the fan coils and increase the
setting of any thermostat placed on them.
Table 5.2
p. 38 shows the messages that can appear on the
display while the chimney sweep function is running, the rela-
tive meaning and the optional actions required.
Limit the time you use the chimney sweep function to
the minimum actually required.
The system automatically interrupts chimney sweep
function after 20 minutes from activation.
If the required CO
2
settings cannot be reached, contact
Robur.