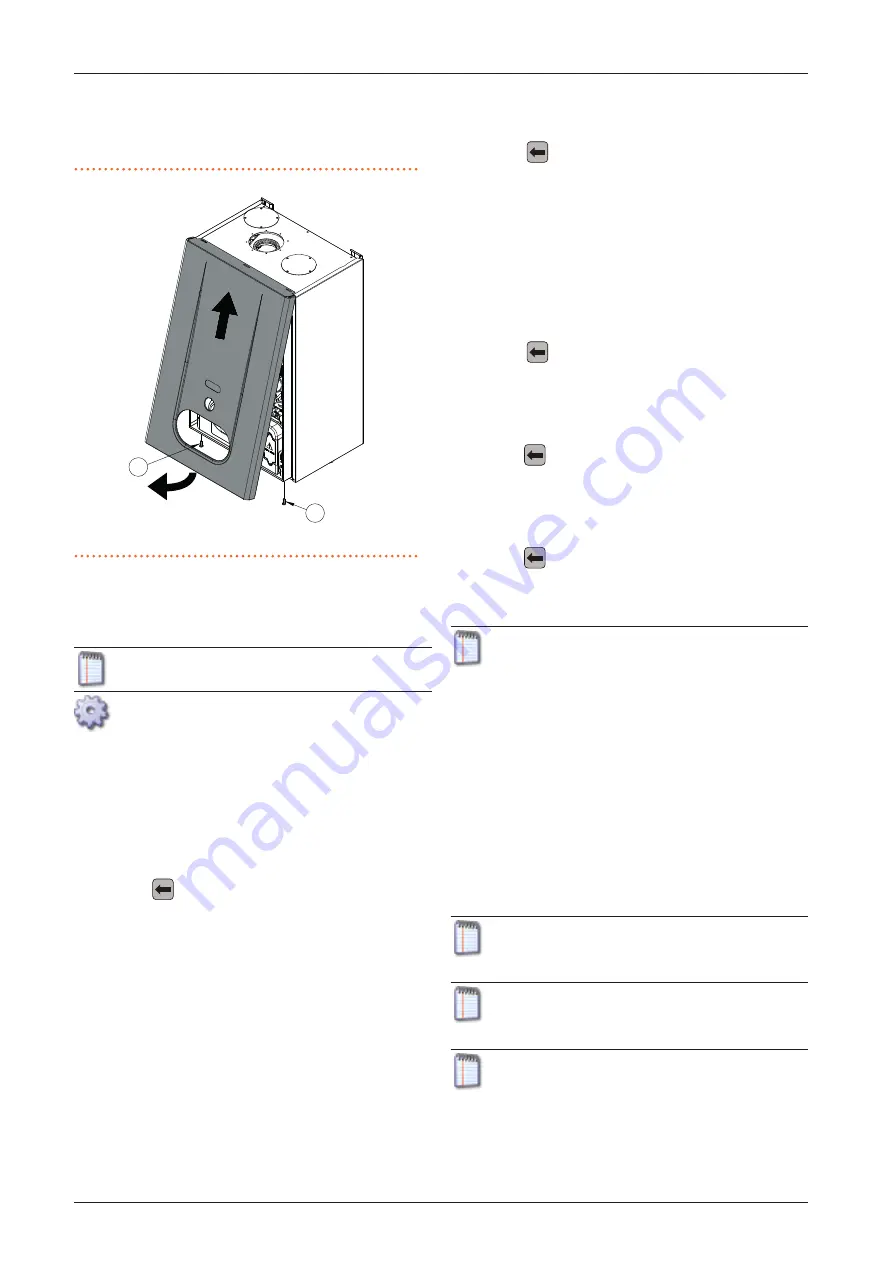
First start-up
Installation, use and maintenance manual – K18 Hybrigas
39
5
boiler front panel (detail 1 Figure 5.1
3. grab the front panel from the bottom and remove it pulling
to yourself and then upwards (Figure 5.1
p. 39).
Figure 5.1
Removal of the front panel of the boiler module
1
Boiler front panel fastening screws
1
1
5.3
HEAT PUMP COMBUSTION PARAMETERS
CHECK
Paragraph reserved exclusively to TACs.
Figure 5.2
1. If the appliance is running, switch it off with the applicable
control system (OQLT019, OCDS007, external request).
2. Remove the cap over the offset adjustment screw (C).
3. Screw in completely the throttle adjustment screw (D).
4. Screw in completely the offset adjustment screw (C).
5. Unscrew the throttle adjustment screw (D) as indicated in
6. Unscrew the offset adjustment screw (C) as indicated in Ta-
ble 5.1
7. Press the
key on the user interface of the heat pump
module of the unit (detail B of Figure 1.14
p. 20) for 5 sec-
onds to activate the chimney sweep function at minimum
power.
8. The display shows the letters "CS.LO" (chimney sweep low
power), alternating with the flashing message "UAIt" (wait)
which indicates that the machine is not yet ready for the
reading.
9. Once an approximate time ranging between 5 and 8 min-
utes elapses, the flashing message becomes "_GO_" to indi-
cate that the combustion control can be implemented.
10. Ensure the CO
2
value is between values indicated in column
"Minimal thermal capacity" of Table 5.1
p. 40. Otherwise
set CO
2
percentage reading by acting on the offset adjust-
ment screw.
11. Press the
key on the user interface again for 5 seconds
to activate the chimney sweep function at maximum power.
12. The display shows the letters "CS.HI" (chimney sweep high
power), alternating once again with the flashing message
"UAIt" (wait) which indicates that the machine is not yet
ready for the reading.
13. After a short while, the flashing message becomes "_GO_"
again to indicate that the combustion control at maximum
power can be implemented.
14. Ensure the CO
2
value is between values indicated in column
"Nominal thermal capacity" of Table 5.1
If the check is successful:
15. Press the
key on the user interface again for 5 seconds
to deactivate the chimney sweep function and complete the
procedure.
If the check is not successful:
16. Set CO
2
percentage reading by acting on the throttle adjust-
ment screw.
17. Press the
key on the user interface again for 5 seconds to
deactivate the chimney sweep function.
18. Repeat points 7 to 10 to reactivate the chimney sweep func-
tion at minimum capacity; verify once again and if necessary,
correct the CO
2
value in these conditions by actuating the
offset adjustment screw.
19. Press the
key on the user interface again for 5 seconds to
activate the chimney sweep function at maximum capacity,
and then again for 5 seconds to deactivate it and complete
the procedure.
To ensure the chimney sweep function is executed prop-
erly, there must be adequate thermal load, otherwise the
appliance could reach the maximum limit of the delivery
and/or return temperature and then stop.
The following may be necessary to provide adequate
thermal load, depending on the system characteristics:
activate optional pumps or zone valves of the distribu-
tion water circuit;
fully open the manual or thermostatic valves, mounted
on the radiators;
activate the ventilation of the fan coils and increase the
setting of the optional thermostat placed on them.
Table 5.2
p. 40 shows the messages that can appear on the
display while the chimney sweep function is running, the rela-
tive meaning and the optional actions required.
Limit the time you use the chimney sweep function to
the minimum actually required.
The system automatically interrupts chimney sweep
function after 20 minutes from activation.
If the required CO
2
settings cannot be reached, contact
Robur.