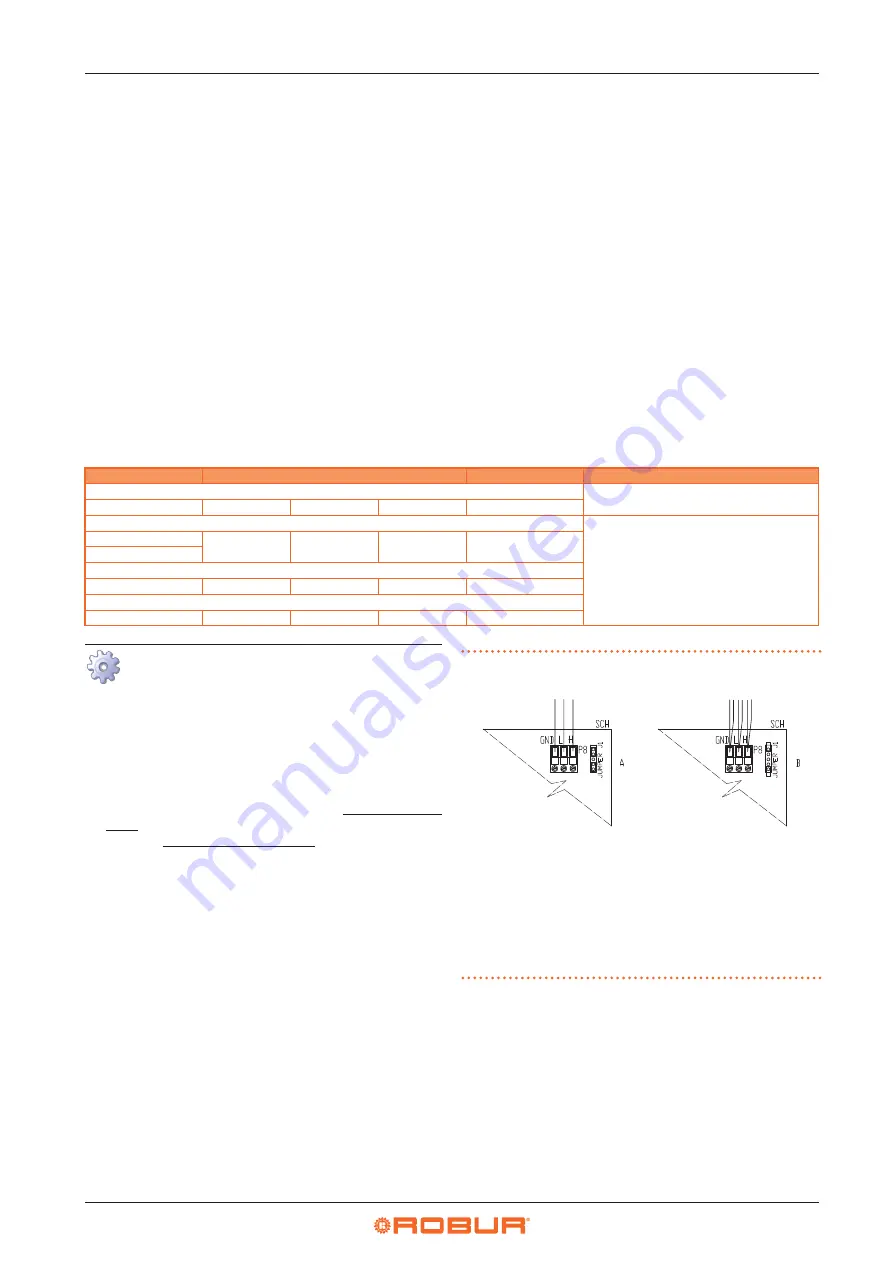
Electrical installer
26
4
2� Connect the three lead-in wires to the terminal (TER)
in the electrical panel on the machine.
3� Provide the earth lead-in wire longer than live ones
(last to be torn in the event of accidental pulling).
4.4
SET-UP AND CONTROL
Control systems, options (1) (2) (3)
Three separate adjustment systems are provided, each with
specific features, components and diagrams (see 4.4
4.5
p. 27):
▶
System (1), with DDC control (with CAN-BUS connection).
▶
System (2), with CCP/CCI control (with CAN-BUS connec-
tion).
▶
System (3), with an external request.
CAN-BUS communication network
The CAN-BUS communication network, implemented with
the cable of the same name, makes it possible to connect and
remotely control one or more Robur appliances with the DDC or
CCP/CCI control devices.
It entails a certain number of serial nodes, distinguished in:
▶
intermediate nodes, in variable number;
▶
terminal nodes, always and only two (beginning and end);
Each component of the Robur system, appliance (GAHP, GA, AY,
...) or control device (DDC, RB100, RB200, CCI, ...), corresponds to
a node, connected to two more elements (if it is an intermedi-
ate node) or to just one other element (if it is a terminal node)
through two/one CAN-BUS cable section/s, forming an open lin-
ear communication network (never star or loop-shaped).
CAN-BUS signal cable
The DDC or CCP/CCI controllers are connected to the appliance
through the CAN-BUS signal cable, shielded, compliant to Table
4.1
p. 26 (admissible types and maximum distances).
For lengths ≤200 m and max 4 nodes (e.g. 1 DDC + 3 GAHP), a
simple 3x0.75 mm shielded cable may even be used.
Table 4�1
CAN BUS cables type
CABLE NAME
SIGNALS / COLOR
MAX LENGTH
Note
Robur
Ordering Code OCVO008
ROBUR NETBUS
H= BLACK
L= WHITE
GND= BROWN
450 m
Honeywell SDS 1620
In all cases the fourth conductor should not be
used
BELDEN 3086A
H= BLACK
L= WHITE
GND= BROWN
450 m
TURCK type 530
DeviceNet Mid Cable
TURCK type 5711
H= BLUE
L= WHITE
GND= BLACK
450 m
Honeywell SDS 2022
TURCK type 531
H= BLACK
L= WHITE
GND= BROWN
200 m
How to connect the CAN BUS cable to the appliance
To connect the CAN-BUS cable to the S61 electronic board (Para-
graph 1.5
p. 13), located in the Electrical Panel inside the unit,
(Figure 4.3
1� Access the Electrical Board of the appliance according to the
Procedure 4.2
2� Connect the CAN-BUS cable to terminals GND, L and H
(shielding/ea two signal conductors);
3� Place the CLOSED J10 Jumpers (Detail A) if the node is ter-
minal (one connected CAN-BUS cable section only), or OPEN
(Detail B) if the node is intermediate (two connected CAN-
BUS cable sections);
4� Connect the DDC or the CCP/CCI to the CAN-BUS cable ac-
cording to the instructions in the following Paragraphs and
the DDC or CCP/CCI Manuals.
Figure 4�3
Electrical wiring diagram - Connection cable CAN BUS to
electronic board
SCH
Electronic board
GND
Common data
L
Data signal LOW
H
Data signal HIGH
J1
Jumper CAN-BUS in board
A
detail of "terminal node" case (3 wires; J1=jumper
"closed")
B
Detail of "intermediate node" case (6 wires; J1=jumper
"open")
P8
CAN port/connector
GAHP Configuration (S61) + DDC or CCP/CCI
(Systems (1) and (2) see also Paragraph 1.7