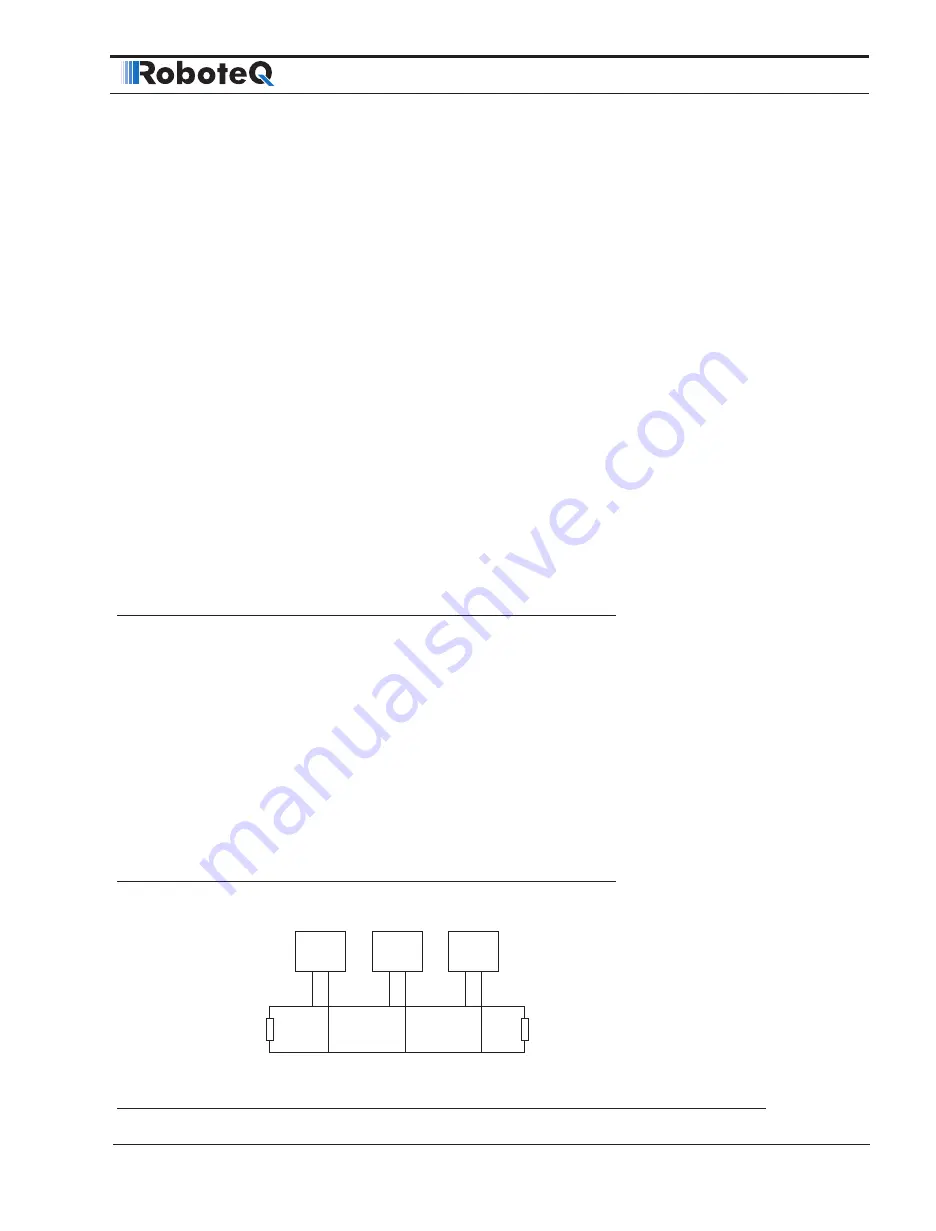
Use and benefits of CANopen
CANBus Networking Manual
27
SECTION 3
CANopen
Interface
This section describes the configuration of the CANopen communication protocol and the
commands accepted by the controller using the CANopen protocol. It will help you to en-
able CANopen on your Roboteq controller, configure CAN communication parameters, and
ensure efficient operation in CANopen mode.
The section contains CANopen information specific to Roboteq controllers. Detailed information
on the physical CAN layer and CANopen protocol can be found in the DS402 documentation.
Use and benefits of CANopen
CANopen protocol allows multiple controllers to be connected into an extensible unified
network. Its flexible configuration capabilities offer easy access to exposed device param-
eters and real-time automatic (cyclic or event-driven) data transfer.
The benefits of CANopen include:
•
Standardized in EN50325-4
•
Widely supported and vendor independent
•
Highly extensible
•
Offers flexible structure (can be used in a wide variety of application areas)
•
Suitable for decentralized architectures
•
Wide support of CANopen monitoring tools and solutions
CAN Connection
CANH
CANL
120 Ohm
Termination
Resistor
120 Ohm
Controller
Controller
Other
CAN Device
FIGURE 3-1. CAN connection