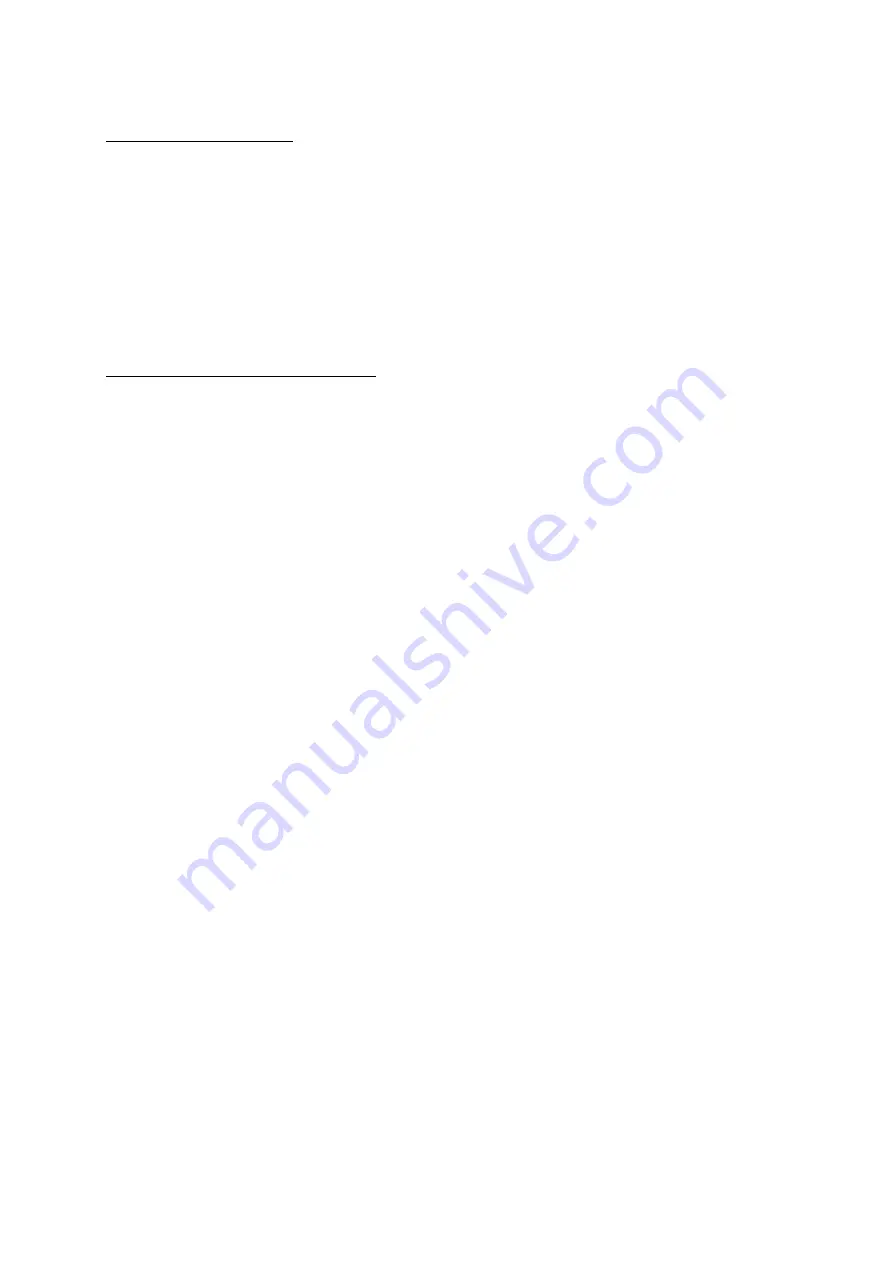
6
Fuel temperature limitations
According to the “Supplement”, assuming Jet A1 fuel, the minimum permissible fuel
temperature in the fuel tank before takeoff is -30°. For diesel, this minimum must be
above 0°C. On the other hand, minimum permissible fuel temperature in the tank during
flight is -35° for Jet A1, against -5°C for diesel. It is thus obvious that using diesel might
lead to problems if temperatures are not carefully monitored, particularly during
wintertime.
Diesel and Jet A1 may be mixed. However, as soon as the proportion of diesel in the tank
is more than 10%, or if there is uncertainty about which type of fuel is in the tank, the
fuel temperature limits for diesel operation must be observed.
Fuel circuit, common rail, direct injection
With the advent of electronic control, and provided that direct diesel injection is used, as is the case
for the TAE 125-01, the common rail technology can be applied to further improve the quality of the
exhaust gases, to reduce noise and to further reduce fuel consumption, as compared to conventional
diesel engines.
1°)
The electric pump, originally installed for priming purposes only, must be “ON” for
takeoff and landing
. According to Thielert, the electrical pump “supports the fuel flow to the fuel
filter module, if required”; according to Maintenance a possible reason is that the high pressure pump
(see below) is located on the far front of the engine, which is why the electrical pump acts as an
additional safety in case of failure of the engine driven fuel pump feeding the high pressure pump. At
any rate, no fuel pressure indicator is located on the instrument panel.
2°) From the fuel tank, the fuel goes through the fuel selector to a small reservoir (probably a
remainder from the original gasoline system), then through the shutoff valve via the electric pump.
Thus far, the system is similar to the original one, except for the fact that, for takeoff and
landing, the electrical pump must be “ON”.
3°) Beyond the shutoff valve, the fuel is ducted towards a so-called filter module which includes a
fuel pre-heater system. This pre-heater, typical for diesel engines, is thermostatically controlled to the
effect that the fuel is heated until the operating temperature of 60°C is reached.
The heating is
obtained by exchange between excess fuel returning to the tank (see below) and the cold
supply fuel.
4°) Downstream of the filter module, a camshaft driven pump, i.e. the engine driven pump, increases
the fuel pressure to 5 bar (72 lbs/sq.in.), after which a high pressure pump, also camshaft driven,
further increases the pressure up to 1500 bar (21700 lbs/sq.in.), and delivers the fuel to a duct known
as the common rail.
5°) The common rail acts as a sort of high pressure accumulator which supplies all cylinders (hence its
name) through an equal number of injector duct connections, and contains highly pressurized fuel
ready for injection at any required moment. However, an electronically (FADEC) actuated pressure
control valve in the common rail, lowers its internal pressure to a maximum of 1350 bar (19500
lbs/sq.in.). This gives way to an excess of fuel which is returned to the tank.
6°) The fuel injectors, whose operation is also electronically (FADEC) controlled, deliver highly
pressurized fuel into the combustion chamber of each cylinder. This is known as direct diesel injection,
or DI, as opposed to the indirect diesel injection, or IDI.
In the IDI system, the fuel is initially injected either into a swirl chamber or into a so-called
prechamber, located in the cylinder head, prior to enter the usual combustion chamber in the cylinder.
In a way, in both these “sub-systems”, the combustion chamber is divided in two parts. Both swirl- or
pre-chamber have their own specific advantages and disadvantages which will not be discussed here.
Versie oktober 07