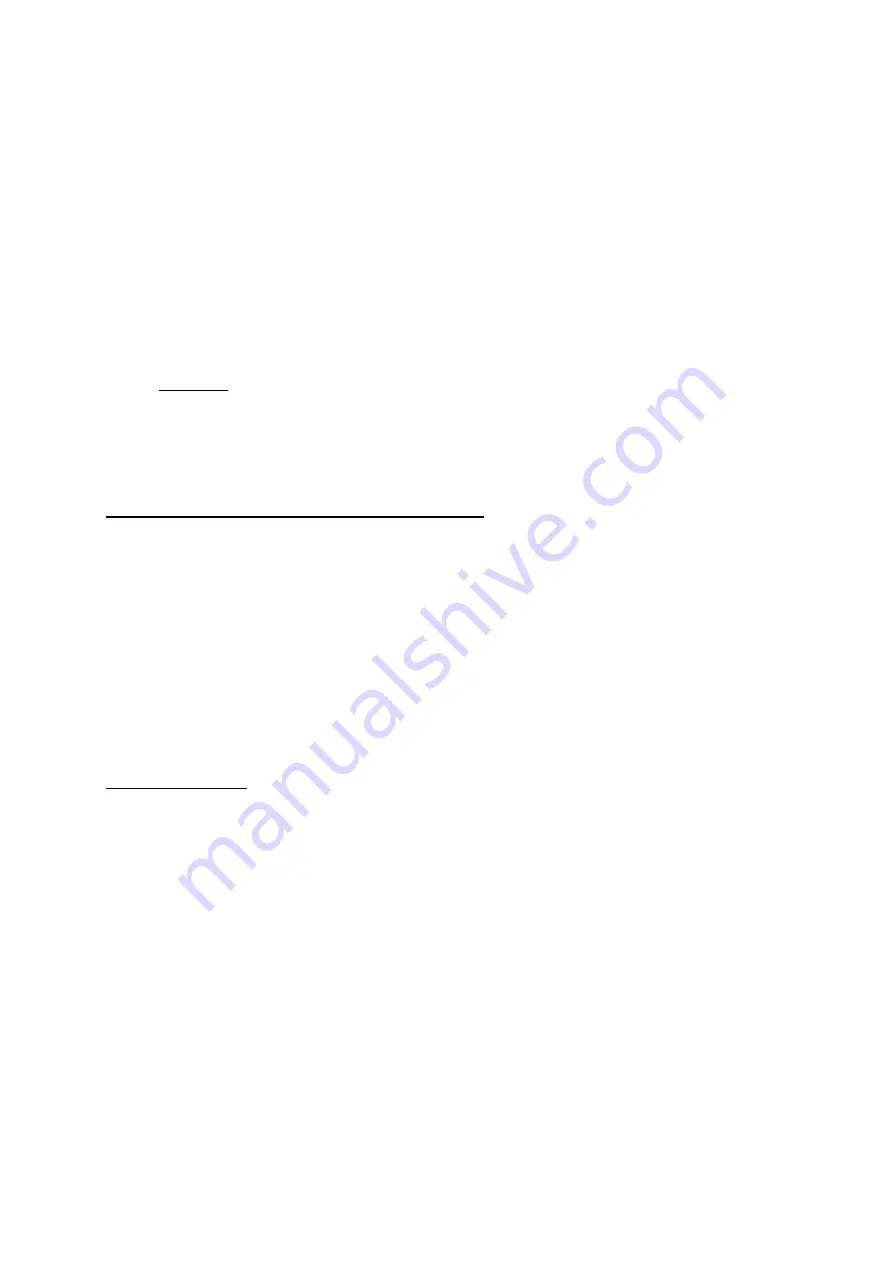
10
fuel injectors in each cylinder, both systems being electrically supplied when the engine master switch
is “ON”.
The engine starting procedure is extremely simple. With the main battery switched on, the selection of
the engine master switch to “ON” causes the glow plugs to heat up, which is indicated by the “GLOW”
warning light momentarily illuminating. It also causes the fuel injectors to open and allow fuel under
pressure stored in the common rail to be injected in the cylinders, the whole operation being FADEC
controlled. As soon as the “GLOW” warning light extinguishes, and with the thrust lever in full idle
position, engine starting may be initiated by turning the starter key.
Small detail: the engine’s hobbsmeter (hourmeter) starts “counting” as soon as the engine master
switch is selected to “ON”, whether the engine is running or not. Switching the engine master switch
to “OFF” causes the engine to shut down.
[HOP3]
CAUTION: Selecting either the battery switch or pulling the alternator circuit-breaker to
“OFF” will not cause the running engine to stop, at least not immediately (see below).
However, if both battery and alternator are switched off, as the FADEC is no
longer electrically supplied, the engine will stop at once.
If the alternator fails,
electrical power will be provided by the battery only. The time the engine can run on
battery alone will depend on total electrical consumption supported by the battery.
ENGINE COOLING AND CABIN HEATING SYSTEMS
Both these systems are closely related. As was mentioned earlier, the engine uses liquid coolant
instead of being air-cooled. One advantage of the liquid cooling system is that shock cooling during
descent is eliminated. The coolant is stored in a tank within the engine compartment, and is a fiftyfifty
mixture of water and BASF Glysantin Protect Plus/G48, again a product which is only available
through Maintenance.
Prior to start engine, the pilot must check the coolant’s level. This is done by means of a yellow
“COOLANT LEVEL” warning light. When the battery switch is selected to “ON”, it is imperative to verify
that the warning light initially illuminates (mostly very shortly) then extinguishes. Assuming that the
light remains illuminated, the coolant level is too low and engine starting is prohibited. Note also that
engine starting is not allowed if the coolant temperature happens to be lower than -30°C. Incidentally,
the same limit is also applicable to the engine oil and gearbox temperatures.
Engine cooling circuit
The coolant leaves the tank and is pumped into the engine where it evidently picks up heat. Upon
exiting the engine, the coolant is directed to a three-way thermostat of which one exit is unregulated
and relates to the cabin heating system (see below). The two other exits regulate the coolant flow
between a so-called short circuit and/or a large circuit (also referred to as “external circuit”),
depending on the coolant’s temperature:
a) Assuming that the coolant’s temperature is less than 84°C, the coolant circulates through the short
circuit which directs it immediately back to the engine via the pump.
b) Assuming that the coolant’s temperature is between 84°C and 94°C, the coolant is caused to flow
partly through the small circuit, partly through the large circuit. This latter circuit includes a heat
exchanger (radiator) located on the left side of the engine, where the fluid is cooled by outside air
coming from the left upper air intake on the front part of the cowling. This heat exchanger is divided
in two parts, one serving the coolant’s fluid cooling, the other serving the engine oil cooling (see
engine oil system). Upon exiting the heat exchanger, the coolant fluid is directed partly back to the
tank, partly back to the engine.
Versie oktober 07