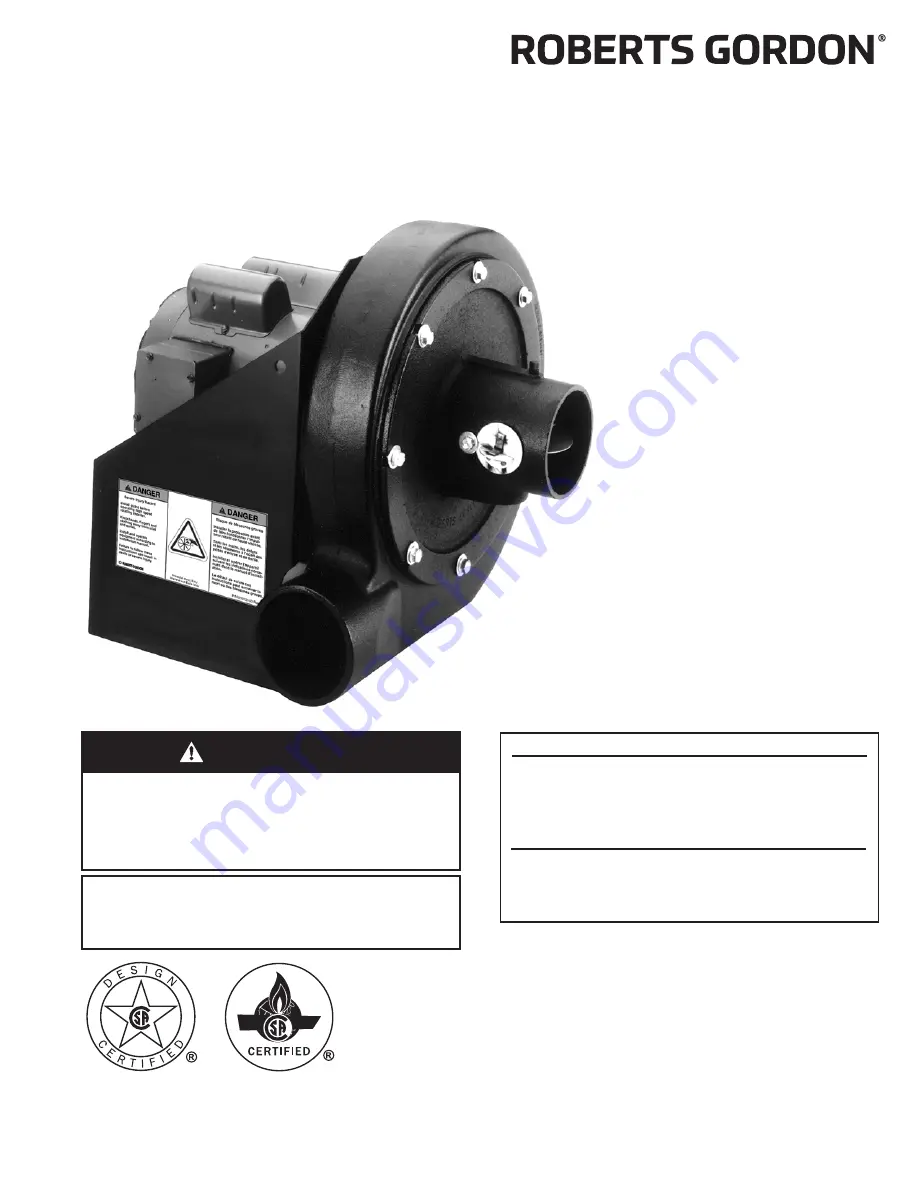
WARNING
Installation must be done by a contractor qualified
in the installation and service of gas-fired heating
equipment or your gas supplier.
Improper installation, adjustment, alteration, service
or maintenance can result in death, injury or
property damage. Read the Installation, Operation
and Service Manual thoroughly before installing or
servicing this equipment.
Installer
Please take the time to read and understand
these instructions prior to any installation.
Installer must give a copy of this manual to the owner.
Owner
Keep this manual in a safe place in order to provide
your service technician with necessary information.
Roberts-Gordon LLC
1250 William Street
P.O. Box 44
Buffalo, New York 14240-0044
Telephone: +1.716.852.4400
Fax: +1.716.852.0854
Toll Free: 800.828.7450
www.robertsgordon.com
© 2018 Roberts-Gordon LLC
EP-200 Series
Pump
Installation,
Operation &
Service Manual
P/N 127200NA Re
v
. M 3/18
Summary of Contents for EP 201
Page 2: ......
Page 4: ......
Page 6: ......
Page 34: ...EP 200 SERIES PUMP INSTALLATION OPERATION AND SERVICE MANUAL 28 of 27 ...