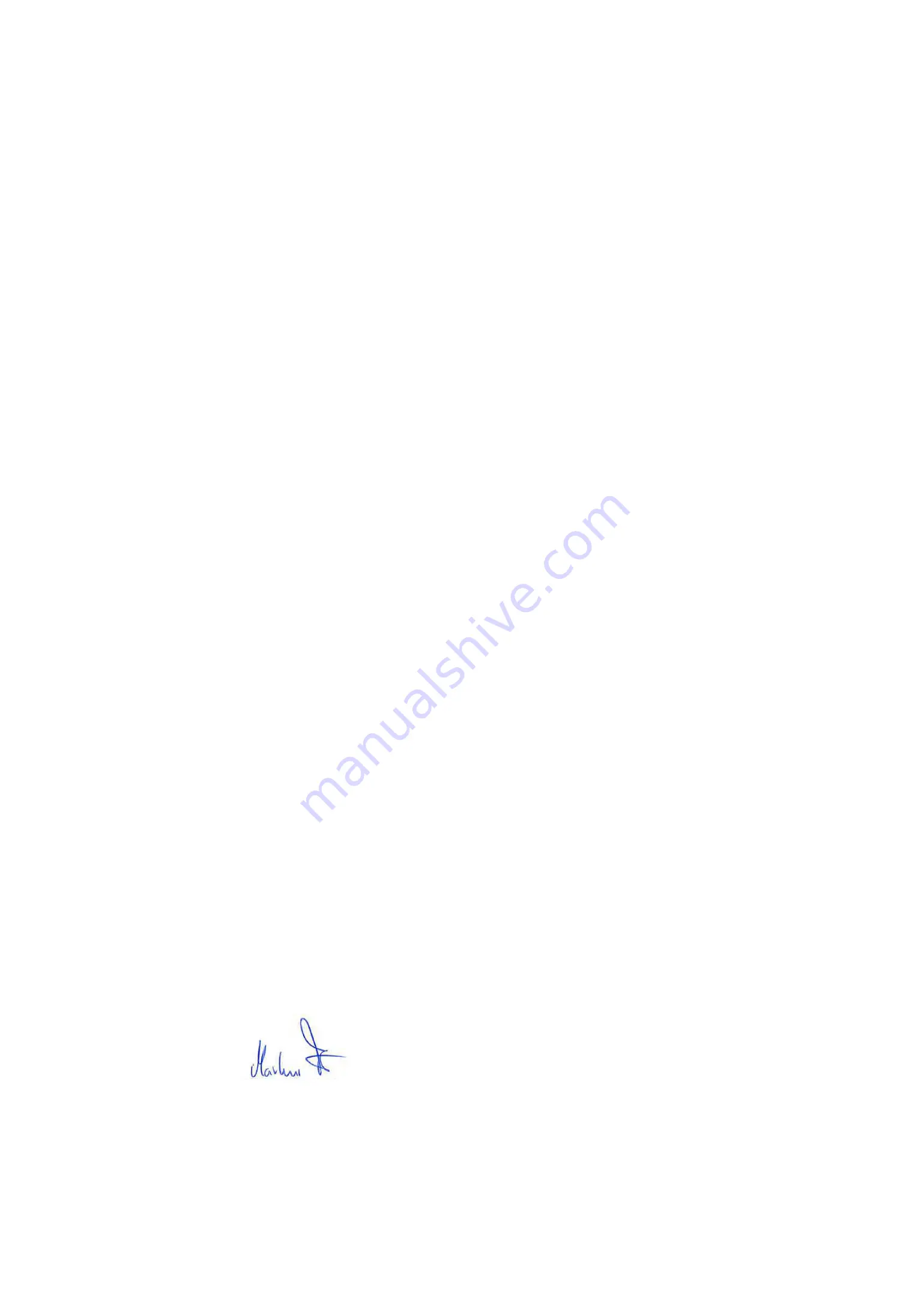
Manufacturer:
Förster-Technik GmbH,
Gerwigstr. 25
78234 Engen
Person residing within the Community authorised to compile the relevant technical documentation:
Müller Barbara
Förster-Technik GmbH,
Gerwigstr. 25
78234 Engen
Description and identification of the machinery:
Make:
Automatic feeder
Type:
TAP0-EZ1-28-M, TAP0-EZ1-32-M, TAP0-EZ1-38-M, TAP0-EZ1-50-M, TAP1-EZ1-32-M, TAP1-EZ1-38-M,
TAP5-EZ2-50-F3, TAP5-EZ2-32-F3, TAP5-EZ2-28-F3, TAP5-EZ2-50-F4, TAP5-EZ2-32-F4,
TAP5-EZ2-28-F4
Function:
Automatic preparation, heating, and dosing of liquid feeds for young animal feeding
It is expressly declared that the machinery fulfils all relevant provisions of the following EU Directives:
2006/42/EG
Directive 2006/42/EG of the European Parliament and of the Council of 17 May 2006 on machinery, and
amending Directive 95/16/EG (recast)
2014/30/EU
Directive 2014/30/EU of the European Parliament and of the Council of 26 February 2014 on the
harmonisation of the laws of the Member States relating to electromagnetic compatibility (recast)
Reference to the harmonised standards used, as referred to in Article 7(2):
EN ISO 12100:2010-11
Safety of machinery - Electrical equipment of machines - Part 1: General requirements
(ISO 12100:2010)
EN 60335-1:2012/A11:2014
Household and similar electrical appliances - Safety - Part 1: General requirements IEC 60335-1:2010
(modified)
EN 61000-6-2:2005/AC:2005
Electromagnetic compatibility (EMC) - Part 6-2: Generic standards - Immunity for industrial environments
EN 61000-6-3:2007/A1:2011/
AC:2012
Electromagnetic compatibility (EMC) - Part 6-3: Generic standards - Emission standard for residential,
commercial and light-industrial environments
Engen, 11.01.2018
-------------------------------------------------------------------------------------------------------------------------------------
Place, date
Signature
Markus Förster
CEO
EC declaration of conformity
according to the EU Machinery Directive 2006/42/EG, Annex II, 1.A