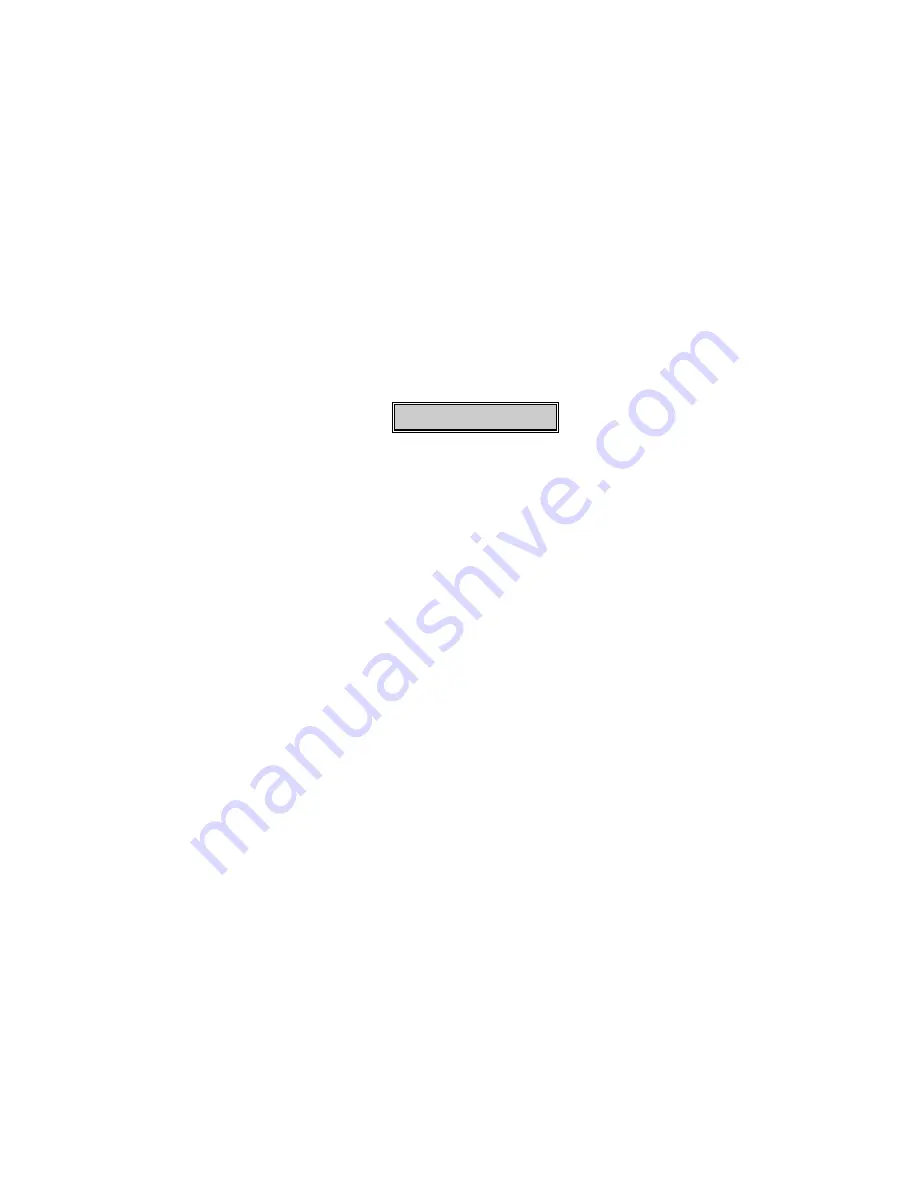
MAN-2V3B-4.1V REV (E)
10
5.8
GAS PIPING LEAK CHECK:
Every 1000 hours of running time or any time the piping
system is disturbed, such as during a corrective maintenance action, the piping should be examined for
leaks. Any obvious leaks should be dealt with as they are detected. Leak testing the piping requires that
the compressor is pressurized, and therefore running or recently run.
A soapy solution in a squirt bottle works best for locating leaks in a gas system. The gaskets and O-
rings needed for the specific repair should be on hand prior to attempting to fix a leak.
Caution: Do not use any flammable solution for leak testing.
The test is simplified if the compressor is allowed to cool, then restarted immediately prior to running
the leak test, since the hot discharge pipes can boil away the leak test soap solution making detection of
leaks difficult or impossible.
WARNING
Hot discharge lines can produce painful burns. Be careful to avoid
making contact with hot pipes while performing tests and repairs.
Wearing safety glasses when performing leak checks is mandatory.
PROCEDURE
a.
Restart compressor after it has been allowed to cool down.
b.
Systematically inspect from joint to joint and fitting to fitting in the gas system piping,
spraying the leak test solution.
c.
Observe for any formation of bubbles. Mark the location of any detected leaks. Large
leaks may blow the soap solution away as quickly as it is applied. These may be detected
by close inspection or by feel. Always practice caution when handling hot discharge
lines.
d.
O-ring joints cannot be corrected by additional tightening. In most every case, the
leaking O-ring must be discarded and a new one installed. Always inspect the surfaces
that seal against the O-ring for defects and correct or replace as required. Insure that O2
cleaned and proper durometer (hardness) o-rings are used.
Note: See Drawing A5089G for O-ring installation and material information
5.9 VALVES:
Valves should be inspected every 4500 hours of operation, or earlier if pressures
vary from normal, flow capacity drops, noise is detected or an abnormally high temperature is observed.
The customer should establish reference data for use in scheduled maintenance by taking gauge readings
when the compressor is running under normal operating conditions.
The perimeter of valve seats and o-rings should be lightly lubed with oxygen compatible grease to ease
assembly. (see additional information in chapter 7)
Summary of Contents for RIX 2V3B-4.1V Series
Page 54: ......
Page 55: ......
Page 56: ......
Page 57: ......
Page 58: ......
Page 59: ......
Page 60: ......
Page 61: ......
Page 62: ......
Page 66: ......
Page 67: ......
Page 68: ......
Page 70: ...P N 515 910 P N 515 911 P N 515 792 P N 515 829 X515 910 X515 911 X515 792 X515 829...
Page 71: ......
Page 72: ......
Page 73: ...P N 76 713 X76 713...
Page 74: ......
Page 75: ......
Page 76: ......
Page 77: ......
Page 78: ......
Page 79: ......