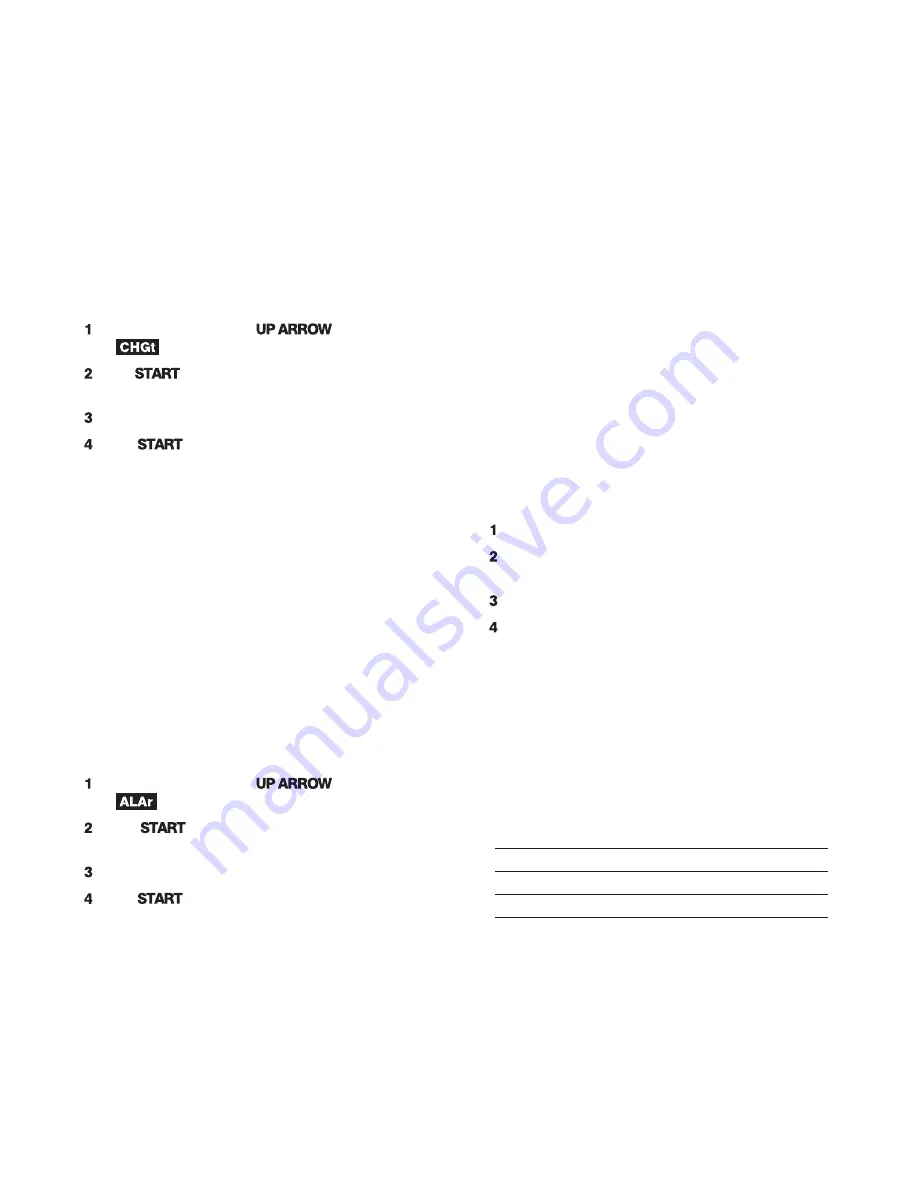
/
7
Editing the Current Segment Target
Temperature During Firing
While the kiln is firing a User Defined program, you can
change the target temperature of the current segment. You
can edit only the segment that is firing. So if the first seg-
ment is the current one, you can edit only the first segment.
To edit other segments, wait until the firing has progressed
to those segments.
Even if the current segment has already started its hold
time, you can still edit the segment's target temperature. You
can raise or lower the target temperature. The controller will
go back out of hold and fire to the new target temperature at
the original rate. (You cannot edit the rate, however.)
During a firing, press the
repeatedly un-
til
appears.
Press
. The target temperature for the current
segment will appear.
Use thearrow keys to changethetarget temperature.
Press
. The normal kiln temperature will ap-
pear.
The Alarm
The alarm works in both PMC and User Defined pro-
grams.
While the kiln is firing, you can set the alarm, which
sounds when the kiln reaches the alarm temperature. Use
the alarm to alert you to check the fusing or slumping of
glass.
You can enter only one alarm temperature at a time. How-
ever, after the alarm beeps, you can set the alarm for another
temperature, as many times as you want, during the firing.
Entering an alarm temperature automatically erases the pre-
vious alarm temperature.
Note:
The alarm temperature that you set during a
firing must be higher than the current display
temperature.
During a firing, press the
repeatedly un-
til
appears.
Press
. The current alarm temperature will
appear.
Use thearrow keys to changethealarm temperature.
Press
. The normal kiln temperature will ap-
pear.
To silence the alarm, press any key.
An alarm temperatureof 32°F / 0°C willturn off thealarm.
Lost Wax Burnout
Caution:
Only kilns with vent holes are designed
for lost wax burnout. However, you can use a kiln
without the vent hole provided that you open the
door ½” during venting.
Caution:
Always use a wax tray.
Note:
These instructions apply to injection wax that
melts at 200°F, not pattern waxes and plastics that
melt at higher temperatures. If smoke appears dur-
ing wax elimination, turn off the kiln. Smoking wax
means the kiln fired hotter than 300°/148°C.
Overview
Lost wax casting is the process of carving a shape in wax,
making a mold, and then casting that shape in metal. After
the wax has been carved, a mold is made of the wax shape.
The mold is a negative image of the wax. The wax is later
melted out of the mold through hollow channels called
sprues.
Lost wax burnout is the process of preparing a casting
mold for the melted metal that will be poured into it. The
steps in lost wax burnout:
Melt the wax from the mold.
Remove wax from the kiln before raising the temper-
ature higher than 300°F/148°C.
Harden the mold at high temperature.
Maintain the mold at the casting temperature recom-
mended for the type of metal that will be poured into
the mold.
Caution:
Prevent wax or carbon from contacting
the kiln’s walls and elements. Carbon build-up in-
side a kiln ruins the interior. Carbon conducts elec-
tricity and causes elements to short circuit. Damage
to elements from contact with foreign materials is
not covered by warranty.
A Sample Program
Rate
Temp.
Segment
°F/°C
°F/°C
Hold
1
500/277
300/148
01.00
2
500/277
1350/732
01.00
3
450/250
800/426
02.00
Segment 1 heats the wax to 300°F/148°C and holds it for
one hour, allowing it to drip from the mold.
Segment 2 hardens the mold.
Segment 3 lowers temperature to 800°F/426°C, the typi-
cal casting temperature for silver. (Most types of gold cast at
900°F/482°C.)
Note:
Casting temperature depends on the size of
the mold. The temperatures above are only a guide.