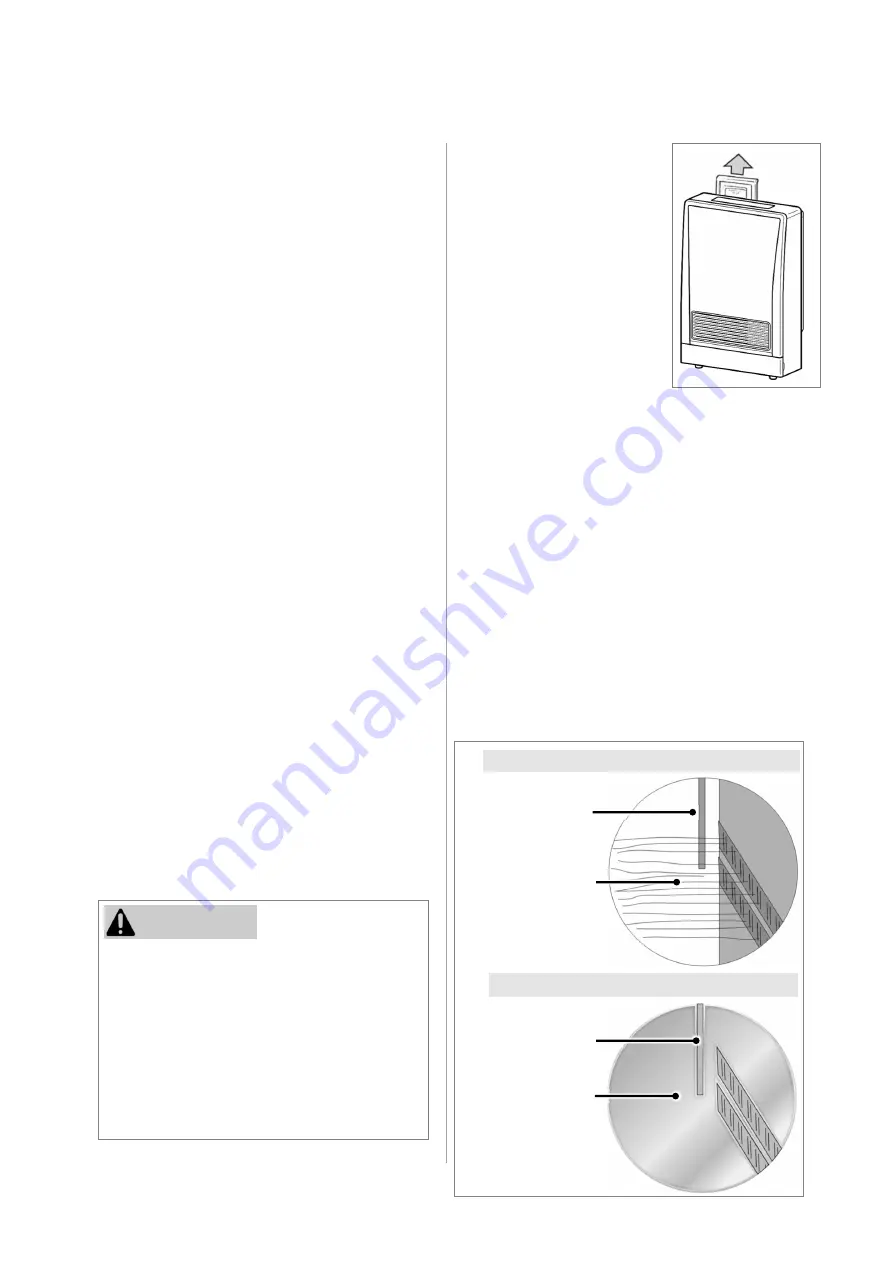
EX08DT and EX11DT Installation and Operation Manual
37
Filters
Dirty filters reduce the air flow
and the furnace’s ability to
produce heat. The filters
should be cleaned frequently
during the heating season.
If the filters become blocked,
the filter indicator lamp will
flash red and a beep will
sound five times. This
beeping will repeat every five
minutes. Eventually the
furnace will turn off and
display fault code 14 on the
control panel display.
This direct vent furnace must be inspected
annually by a trained and qualified
professional. Repairs and maintenance must
be performed by a trained and qualified
professional. The trained and qualified
professional must verify proper operation
after servicing.
More frequent cleaning may be required due
to excessive lint from carpeting, bedding
material, etc. It is imperative that control
compartments, burners, and circulating air
passage ways of the furnace be kept clean.
Any screen or guard removed for servicing
the furnace must be replaced prior to
operating the furnace. Clean as follows:
1. Turn heat off. Allow to cool for one hour.
2. Remove the front panel by removing the
five screws.
3. Use pressurized air to remove dust from
the main burner, heat exchanger, and
fan blades.
4. Use a soft, dry cloth to wipe the cabinet.
Do not use wet cloth or spray cleaners on
the burner.
The flue should be inspected annually for
blockages or damage.
Motors are permanently lubricated and do
not need periodic lubrication. Keep fan and
motor free of dust and dirt by cleaning
annually.
Verify proper operation after servicing.
When attaching the front panel, do not clip
or pinch any electric cords to prevent electric
shock.
Exterior Care
Dampen soft cloth with warm water. Wring
water out well and wipe the unit.
Do not use volatile substances such as
benzene or thinners as they may cause
fading of the paint and deformation of the
resin.
Prevent dust from accumulating on the
power cord, side covers, and parts
behind the furnace.
Keep the area around flue terminal free of
snow and ice. The furnace will not
function properly if the intake air or
exhaust is impeded by obstructions.
Refer to “Flue Terminal Clearances” in
section “4.3.2 Clearances.” The
clearance in Ref. A should be maintained
from any snow accumulation.
CAUTION
To clean the filters, the furnace should be OFF and cool.
Remove the filter and clean it using a soft dry cloth or vacuum.
If the filter is greasy, wash with warm soapy water, rinse, and
dry completely.
Do not use the furnace without the filter installed.
Install the air filter properly so that the filter is flush against the
back surface of the furnace, with the top angle of the frame
pointing outward (away from the furnace). There should be no
spacing or air gaps between the air filter and furnace.
Visual Inspection of Flame
Check that the burner flames are operating normally. The
flame can be seen through the circular window through the
louvers.
When operating normally, the burner flame should appear as
long, clear, blue, stable streaks. Yellow flames or an orange
color is abnormal and maintenance is required.
6. Maintenance
Air Filter
Figure 51
NORMAL
Flame Rod
Long, clear, blue,
stable flames
Yellow flames or
orange color
ABNORMAL
Flame Rod
Figure 52