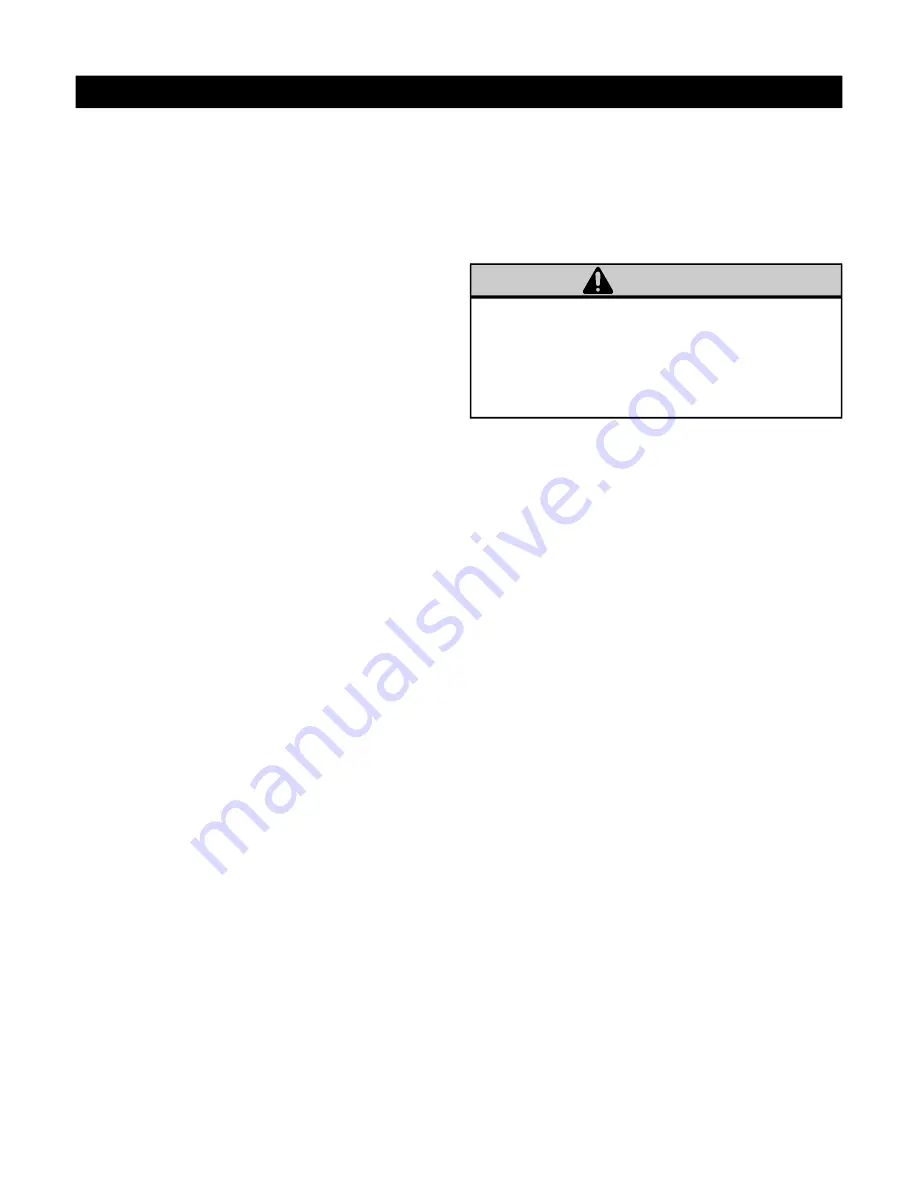
Rinnai Corporation Hydronic Air Handler Manual
19
START-UP PROCEDURE (HEATING ONLY):
The following conditions must be met prior to unit
start-up.
Debris from soldering and/or other installation
activities can cause equipment failure. Ensure that all
associated lines and appurtenances are free of debris.
Check to ensure that unit is secure.
Check that blower wheel rotates freely within the scroll
housing.
Check all wiring to ensure that connections are tight.
Check all ductwork and pipe connections to ensure
proper seal.
Check to ensure that all packaging wraps are removed
from equipment.
Ensure that front access doors are properly installed.
Check to ensure proper connection(s) to the
appropriate blower speed tap (Heat /Cool – High and
Low). Refer to Dry Air Delivery Table and/or the
appropriate wiring diagram(s) in this manual.
Perform all safety and start-up checks for Tankless
Water Heater as per manufacturer’s instructions.
Having verified all preceding checks, the Air Handler’s
Start-Up Procedure is as follows:
STEP 1:
Purge and fill system; follow appropriate
purging procedure as laid out in this manual in section
titled “Purging and Priming the System”.
STEP 2:
Turn on power supply to Air Handler.
Caution: blower and/or circulator may start to operate
if thermostat is on and a call is present.
STEP 3:
Turn thermostat on and switch system to the
heating mode. The thermostat shall be set higher than
the actual room temperature; this will cause the
circulator to energize and initiate the heating cycle. (If
the pump does not start, or the Air Handler is not
producing heat, refer to the Troubleshooting Section in
this manual).
STEP 4:
Program room thermostat as desired by
homeowner.
START-UP PROCEDURE (COOLING SYSTEM)
Refer to field supplied evaporator coil and outdoor unit
manufacturer’s Installation Instructions for system
hook-up, start-up instructions and refrigerant charging
method details.
TROUBLESHOOTING BLOWER AND/OR PUMP
MOTOR AND CONTROLS
If blower and/or pump motor does not run:
Turn off power and check the following:
1. Check that door switch is in the CLOSED position.
2. Check 3 amp fuse on Printed Circuit Board (PCB).
3. Check for 24 VAC between COM and 24 VAC on
PCB. If no voltage is present, check transformer.
4. Check all connections for kinks which could cause
loose connections. Ensure connections are secure.
5. Verify that approximately 120 VAC is present
across L1 and L2.
If system still fails to start, refer to Figures 20 through
Installation
High voltage is at all times present at motor.
Disconnect power to AHU before removing or
replacing or servicing motor. Wait at least 5 min after
disconnecting power before opening motor. Failure to
follow this CAUTION could result in minor personal
injury or product and property damage.
CAUTION