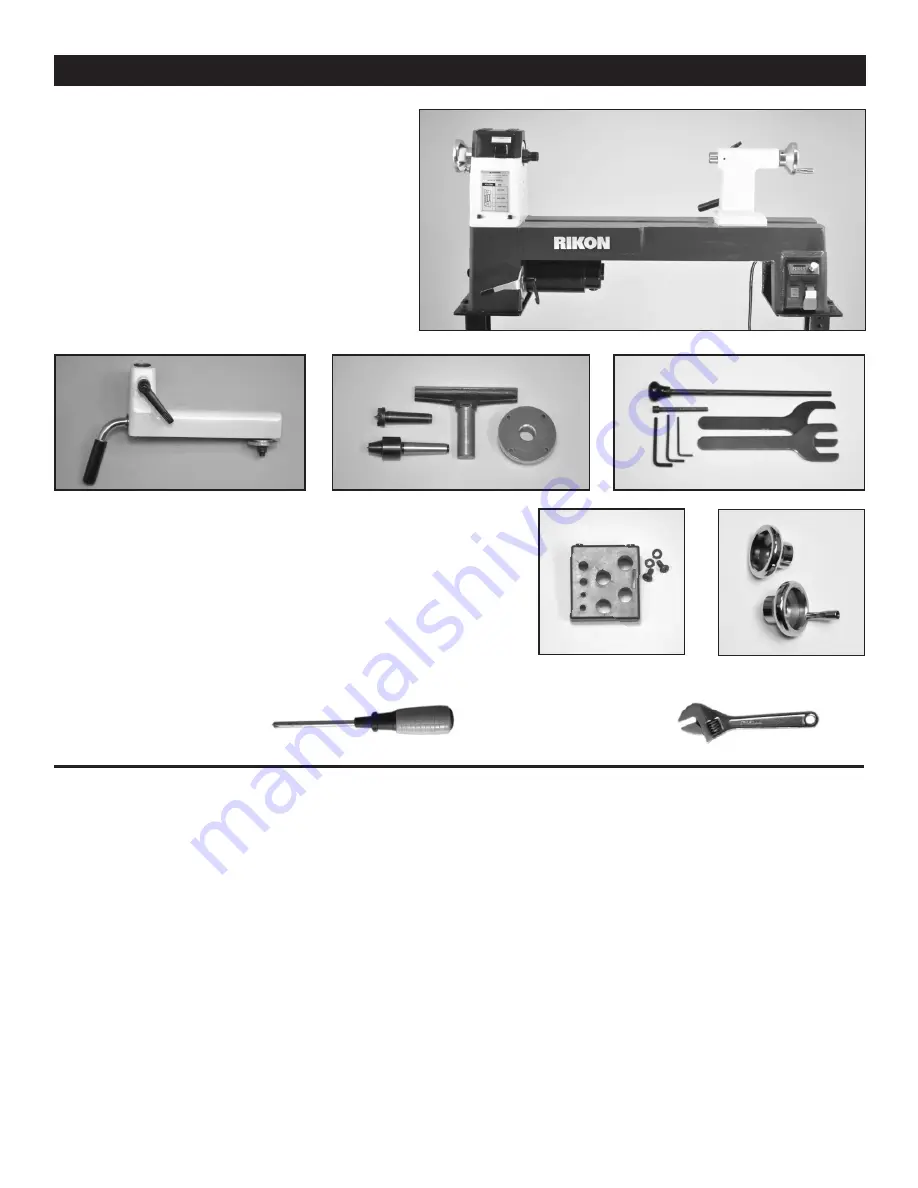
7
Model 70-220VSR Wood Lathe is shipped complete in one box.
Unpacking and Clean-up
1. Carefully remove all contents from the shipping carton. Compare the contents with the list of contents to make sure
that all of the items are accounted for, before discarding any packing material. Place parts on a protected surface
for easy identification and assembly. If any parts are missing or broken, please call RIKON Customer Service (877-
884-5167) as soon as possible for replacements. DO NOT turn your machine ON if any of these items are missing.
You may cause injury to yourself or damage to the machine.
2. Report any shipping damage to your local distributor.
3. Clean all rust protected surfaces with ordinary household type grease or spot remover. Do not use flammables; gas-
oline, paint thinner, mineral spirits, etc. These may damage painted surfaces. Clean thoroughly under the headstock,
tailstock and tool rest body. Then coat with a light film of dry lubricant spray, or wax, to enhance passage of the tool
rest and tailstock on/over the bed. Refrain from using any water-based solvents as they will promote metal rusting.
4. Apply a coat of paste wax to any machined surfaces to prevent rust. Wipe all parts thoroughly with a clean dry cloth.
5. Set packing material and shipping carton aside. Do not discard the packing material until the machine has been set up
and is running properly, in case a return is necessary.
CONTENTS OF PACKAGE
A. Lathe Bed Assembly - including;
B. Motor Assembly
C. Headstock Assembly
D. Tailstock Assembly
E. Electronic Controls
CONTENTS OF PACKAGE
LIST OF LOOSE PARTS
F. Tool Rest Base
G. Spur Center
H. Live Center
I. 8” Tool Rest
J. 3” Faceplate
K. Long Knockout Bar
L. Short Knockout Bar
M. Hex Wrenches (3, 4, 5 mm)
N. Spanner Wrenches (32, 46 mm)
O. Tool Holder, Screws & Washers (2)
P. Outboard Hand Wheel
Q. Tailstock Hand Wheel
R. Manual & Warranty Card
(not shown)
A
E
B
C
F
G
D
H
I
J
L
K
M
N
O
ADDITIONAL TOOLS REQUIRED FOR ASSEMBLY & ADJUSTMENTS
#2 Phillips Screwdriver
Adjustable Wrench
P
NOTE:
Lathe shown with Outboard Hand Wheel * on the
Headstock and Tailstock Hand Wheel ** installed.
Lathe is shown on the #70-920 Stand (sold separately)
*
**
Q