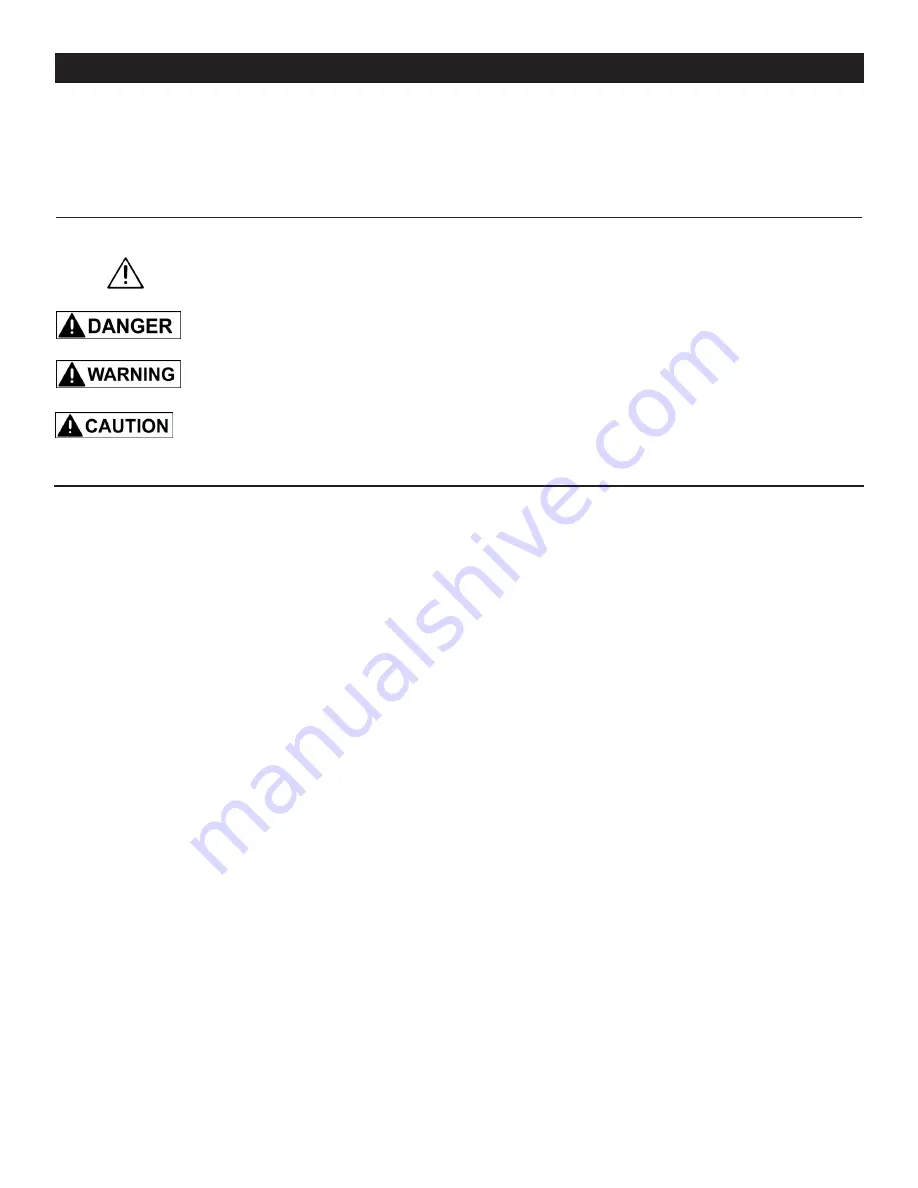
3
SAFETY SYMBOLS
IMPORTANT!
Safety is the single most important consideration in the operation of this equipment.
The following
instructions must be followed at all times.
Failure to follow all instructions listed below may result in electric shock,
fire, and/or serious personal injury.
There are certain applications for which this tool was designed. We strongly recommend that this tool not be modified
and/or used for any other application other than that for which it was designed. If you have any questions about its
application, do not use the tool until you have contacted us and we have advised you.
SAFETY INSTRUCTIONS
GENERAL SAFETY
KNOW YOUR POWER TOOL.
Read the owner’s manual
carefully. Learn the tool’s applications, work capabilities,
and its specific potential hazards.
BEFORE USING YOUR MACHINE
To avoid serious injury and damage to the tool, read and
follow all of the Safety and Operating Instructions before
operating the machine.
1. Some dust created by using power tools contains
chemicals known to the State of California to cause cancer,
birth defects, or other reproductive harm.
Some examples of these chemicals are:
• Lead from lead-based paints.
• Crystalline silica from bricks, cement, and other
• masonry products.
• Arsenic and chromium from chemically treated lumber.
Your risk from these exposures varies, depending on how
often you do this type of work. To reduce your exposure to
these chemicals: work in a well ventilated area and work
with approved safety equipment, such as those dust masks
that are specially designed to filter out microscopic
particles.
2.
READ
the entire Owner’s Manual.
LEARN
how to use
the tool for its intended applications.
3.
GROUND ALL TOOLS.
If the tool is supplied with a 3
prong plug, it must be plugged into a 3-contact electrical
receptacle. The 3rd prong is used to ground the tool and
provide protection against accidental electric shock.
DO
NOT
remove the 3rd prong. See Grounding Instructions
on the following pages.
4.
AVOID A DANGEROUS WORKING ENVIRONMENT.
DO NOT
use electrical tools in a damp environment or
expose them to rain.
5.
DO NOT
use electrical tools in the presence of
flammable liquids or gasses.
6.
ALWAYS
keep the work area clean, well lit, and
organized.
DO NOT
work in an environment with floor
surfaces that are slippery from debris, grease, and wax.
7.
KEEP VISITORS AND CHILDREN AWAY.
DO NOT
permit people to be in the immediate work area,
especially when the electrical tool is operating.
8.
DO NOT FORCE THE TOOL
to perform an operation
for which it was not designed. It will do a safer and
higher quality job by only performing operations for
which the tool was intended.
9.
WEAR PROPER CLOTHING. DO NOT
wear loose
clothing, gloves, neckties, or jewelry. These items can
get caught in the machine during operations and pull the
operator into the moving parts. The user must wear a
protective cover on their hair, if the hair is long, to
prevent it from contacting any moving parts.
10.
CHILDPROOF THE WORKSHOP AREA
by
removing switch keys, unplugging tools from the
electrical receptacles, and using padlocks.
11.
ALWAYS UNPLUG THE TOOL FROM THE
ELECTRICAL RECEPTACLE
when making adjustments,
changing parts or performing any maintenance.
SAFETY ALERT SYMBOL: Indicates DANGER, WARNING, or CAUTION. This symbol may be used
in conjunction with other symbols or pictographs.
Indicates an imminently hazardous situation, which, if not avoided, could result in death or
serious injury.
Indicates a potentially hazardous situation, which, if not avoided, could result in death or serious
injury.
Indicates a potentially hazardous situation, which, if not avoided, could result in minor or
moderate injury.
NOTICE:
Shown without Safety Alert Symbol indicates a situation that may result in property damage.