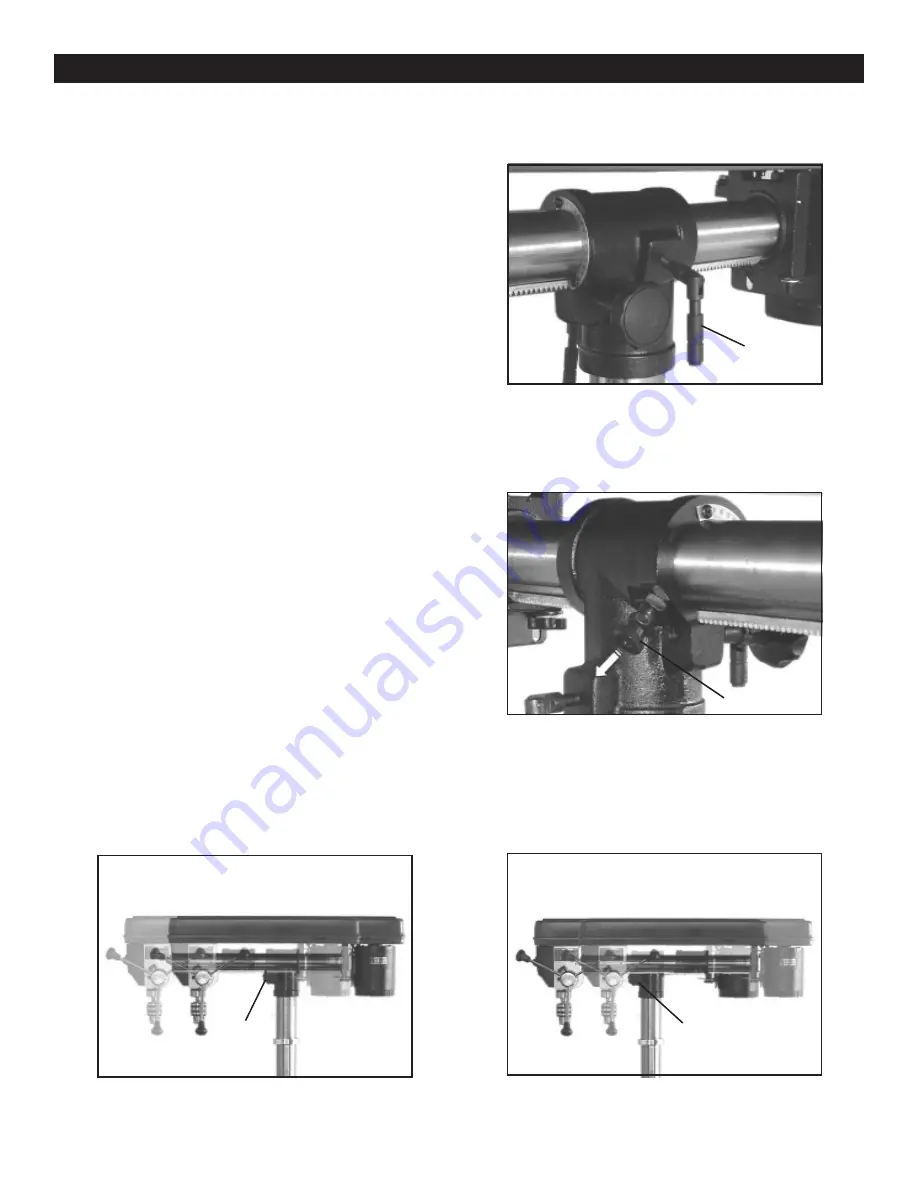
11
HEAD ADJUSTMENTS
Tilting the Drill Press Head 45
o
Clockwise and
90
o
Counterclockwise
1. Loosen the lock handle (A-Fig.19) on the right
side of the drill press head.
2. Pull the guide pin out on the left side of the
drill press head (A-Fig.20) and rotate 90
o
. The
head may be tilted to the desired angle.
3. Tighten the lock handle.
4. To return to the original position, loosen the lock
handle.
5. Move the head back to a vertical position .
6. Pull the guide pin out and rotate until it seats in the
guide pin slot.
7. Tighten the lock handle.
Figure 19
Figure 21
Figure 22
Adjusting the Drill Press Head Forward and
Backwards
1. Loosen the lock handle on the right side of the
head.
2. Turn the handle (A-Fig.21,22 ) to the desired
position.
3. Tighten the lock handle.
Figure 20
Adjustment and Operation
A
A
A
A