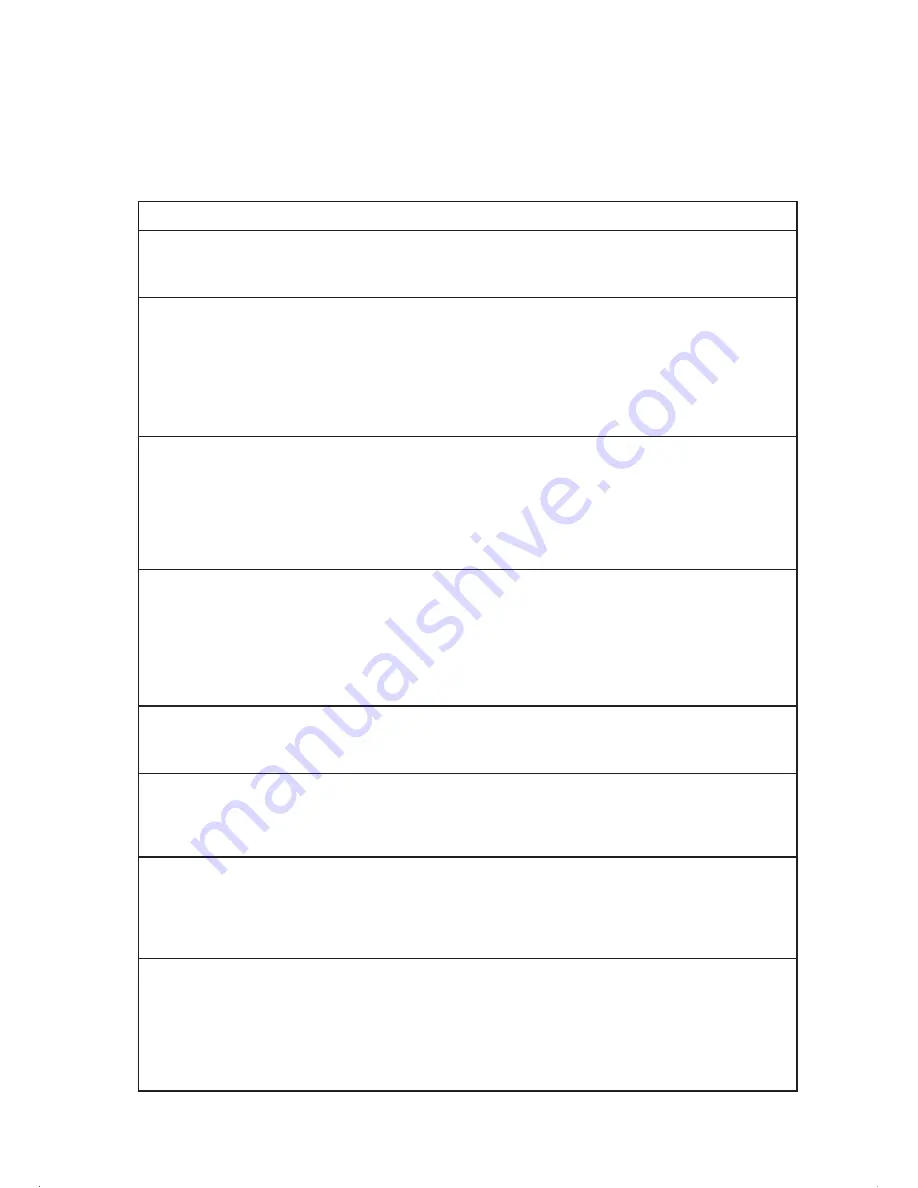
TROUBLE
The machine does
not work when
switched on.
The blade does not
move with the motor
running.
The blade does not
cut in a straight line.
The blade does not
cut, or cuts very
slowly.
Sawdust builds up
inside the machine.
Sawdust inside the
motor housing.
The machine does
not cut at 45
o
or 90
o
angles.
The blade cannot be
properly positioned
on the bandwheels.
PROBABLE CAUSE
1. No power supply.
2. Defective switch.
1. The quick release lever or
blade tension wheel has not
been tightened.
2. The blade has come off one
of the wheels.
3. The saw blade has broken.
4. The drive belt has snapped.
1. Fence for cutting not used.
2. Too fast feed rate.
3. The blade teeth are dull or
damaged.
4. Blade guides not suitably
adjusted.
1. The teeth are dull, caused by
cutting hard material or long
use.
2. The blade was mounted in
the wrong direction.
1. This is normal
1. Excessive dust build-up
on the machine exterior
components.
1. The table is not at right
angles to the blade.
2. The blade is dull or too
much pressure was put on
the workpiece.
1. The wheels are not in
alignment. Defective
bearing.
2. The blade tracking knob
hasn’t been properly
adjusted.
3. Inferior blade.
8.0 Troubleshooting
WARNING:
FOR YOUR OWN SAFETY, ALWAYS TURN OFF AND UNPLUG THE
MACHINE BEFORE CARRYING OUT ANY TROUBLESHOOTING.
10
REMEDY
Check the cable for breakage.
Contact your local dealer for repair.
Switch off the motor, tighten the quick
release lever or blade tension handwheel.
Open the hinged door and check.
Replace the blade.
Replace the belt.
Use a fence.
Put light pressure on the workpiece &
make sure the blade does not bend.
Use a new blade.
Adjust the blade guides (see the section
on page 7).
Replace the blade, use a 6 T.P.I. blade for
wood and soft materials. Use a 14 T.P.I.
blade for harder materials. A 14 T.P.I.
blade always cuts slower due to the fi ner
teeth and the slower cutting performance.
Fit the blade correctly.
Clean the machine regularly. Open the
hinged door and remove the sawdust with
a vacuum cleaner.
Clean the ventilating slots of the motor
with a vacuum cleaner. From time to time
remove the sawdust to prevent it from
being sucked into the housing
Adjust the table.
Replace the blade or put less pressure on
the workpiece.
Contact your local dealer for repair.
Adjust the knob (see the section on page
6).
Replace the blade.
Summary of Contents for 10-336
Page 2: ......
Page 3: ......
Page 12: ...9 0 Parts diagram 11...
Page 14: ...13 Table...
Page 15: ...14 Guide...