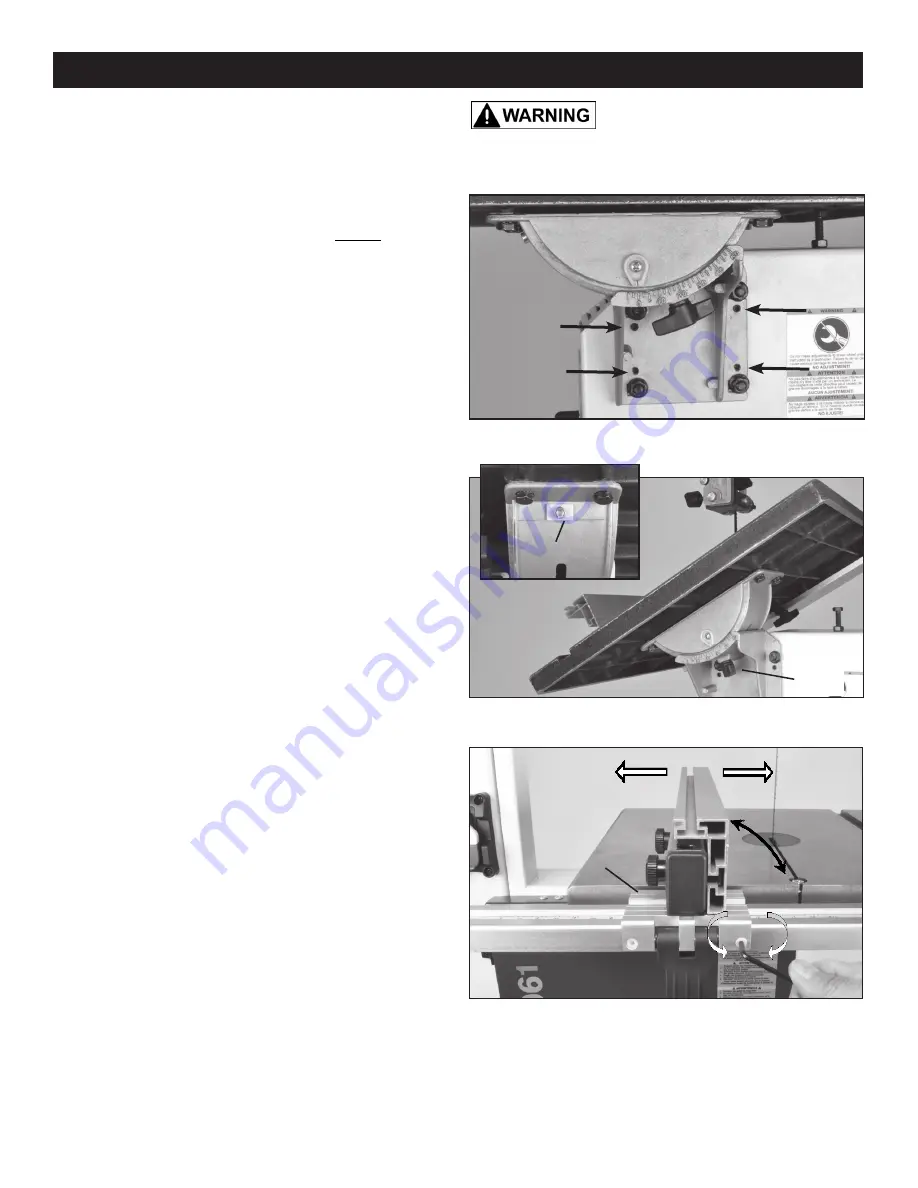
13
ADJUSTMENTS
THE MACHINE MUST NOT BE
PLUGGED IN AND THE POWER SWITCH MUST BE IN THE
OFF POSITION UNTIL ALL ADJUSTMENTS ARE COMPLETE.
SETTING THE TABLE SQUARE
TO THE SAW BLADE’S BACK
While pre-set before shipping, if needed, the table may also
be re-set at 90° to the back of the saw blade by adjusting
the trunnion micro adjust
ment screws.
1. On the lower Trunnion Support (#115),
slightly
loosen
the four Hex Flange Nuts (#116) whose bolts (#112) hold
the support to the bandsaw frame. FIG. 14.
2.
Set a square on the table and against the saw blade’s
back, flat edge.
3. Using the 2.5mm hex wrench, turn the rear trunnion
micro adjusting hex screws (#116A) to adjust the table
position. FIG. 14. Adjust the micro screws in pairs, top 2 or
bottom 2, to adjust the table angle to the blade.
-
Clockwise
moves the support away from the saw frame.
-
Counterclockwise
moves the support towards the frame.
4. Check the table and blade angle for 90° and when
achieved, r
e-tighten the flange nuts to secure the table in
position.
FIGURE 14
TILTING THE TABLE
For bevel cuts, the table tilts 0 through 45 degrees.
1. To tilt the table, loosen the Wing Nut (#113) on the
table trunnion. Set the table to the required angle and
then tighten the wing nut to secure the table. FIG 15.
The trunnion features a Stop (#118) that adjusts to set
the table angle at a precise 45° angle. FIG. 15 Inset.
NOTE:
For critical angled cuts, it is recommended to
verify the correct angle setting using an angle guide, or
by making trial cuts in scrap wood.
ADJUSTING THE RIP FENCE
The locking pressure and angle of the rip fence has been
factory-set with the two plastic Hex Screws (#99) on the
front of the Fence Carrier (#100). FIG. 16.
If adjustment is required, proceed as follows:
1. Position the fence assembly on the front Guide Rail
(#98) and raise the cam action Fence Handle (#101) up to
vertical position.
2. With the 3mm hex wrench, adjust the plastic hex screws
clockwise to increase clamping pressure, counterclockwise
to decrease clamping pressure. Note that these adjust-
ments will also change the angle of the fence to the blade.
A
lign the fence so it is parallel to the blade and miter gauge
slot in the table top.
3. Press the handle down to clamp the fence assembly
to the front guide rail to check the settings.
Make
further
adjustments with the hex screws in small steps.
FIGURE 15
FIGURE 16
The Fence (#106) can be adjusted
90
°
to the table by
turning the four plastic set screws (#160) until the desired
setting is reached (A-Fig. 16).
SET
SCREWS
45° STOP
WING
NUT
USE FENCE
ON LOWER
SIDE OF
TABLE
90
°
A
(X4)