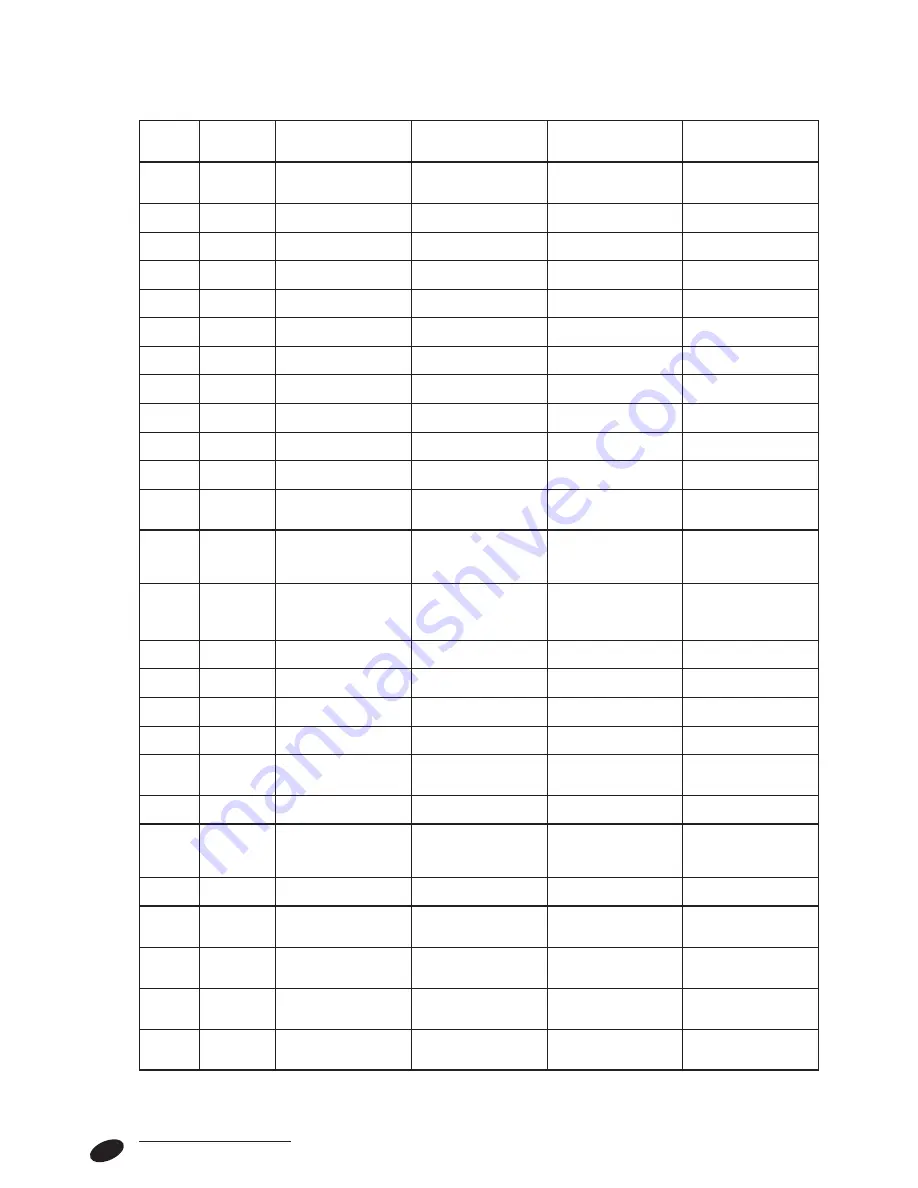
TECHNICAL ASSISTANCE SERVICE
50
Error
code via
QAA
Diagnostic
info
Description of error
Type of fault
System action
Procedure
50
462
DHW 1 temperature
sensor error
Short circuit and fault in
DHW temperature sensor
(B3)
Message
Check/replace
temperature sensor
52
148
DHW 2 sensor error
Short circuit in DHW
temperature sensor (B3)
Message
Check/replace
temperature sensor
52
149
DHW 2 sensor error
DHW temperature sensor
(B3) faulty
Message
Check/replace
temperature sensor
61
126
Room unit 1 error
No further differentiation
Message
Check/replace room unit,
room temperature sensor
61
382
Room unit 1 error
No further differentiation
Message
Check/replace room unit,
room temperature sensor
61
383
Room unit 1 error
No further differentiation
Message
Check/replace room unit,
room temperature sensor
61
384
Room unit 1 error
No further differentiation
Message
Check/replace room unit,
room temperature sensor
61
385
Room unit 1 error
Software error detected
Message
Check/replace room unit,
room temperature sensor
61
386
Room unit 1 error
Unknown message type
Message
Check/replace room unit,
room temperature sensor
61
387
Room unit 1 error
No further differentiation
Message
Check/replace room unit,
room temperature sensor
61
471
Room unit 1 error
Unknown datapoint
request from room unit
Message
Check/replace room unit,
room temperature sensor
61
472
Room unit 1 error
Room unit waiting to
write to write-protected
parameter
Message
Check/replace room unit,
room temperature sensor
62
438
Room unit 1 or timer
connection error
Connection error
Message
Check connection
to room unit/timer-
thermostat. Unit not
recognised
73
609
Solar collector sensor
error (if solar clip-in
option is installed -
accessory)
Valid temperature for
solar collector not
available
Message
Check solar clip-
in; check/replace
temperature sensor
77
156
Air pressure sensor error
(not used)
Short circuit in
temperature sensor
Message
Check/replace air
pressure switch
77
157
Air pressure sensor error
(not used)
Pressure switch faulty
Message
Check/replace air
pressure switch
78
154
Water pressure sensor
error (not used)
Short circuit in pressure
switch
Message
Check/replace water
pressure switch
78
155
Water pressure sensor
error (not used)
Pressure switch faulty
Message
Check/replace water
pressure switch
78
510
Water pressure sensor
error (not used)
Water pressure too high
or too low, or reading not
plausible
Burner lockout
(permanent). Lockout
reset required
Check/replace water
pressure switch
78
511
Water pressure sensor
error (not used)
Reading not plausible
Safety shutdown
Check/replace water
pressure switch
81
518
LPB communication error
LPB circuit short
circuited or not powered
Message
Check the LPB
connection. Check the
power supply to the
control card
82
519
LPB address error
LPB address conflict
Message
Check the LPB
connection
91
131
EEPROM data loss
Hardware fault
Burner lockout
(permanent). Lockout
reset required
Contact Technical
Assistance Service
91
258
EEPROM data loss
Data overflow caused
by power failure during
functioning
Burner lockout
(permanent). Lockout
reset required
Contact Technical
Assistance Service
91
268
EEPROM data loss
Hardware fault
Burner lockout
(permanent). Lockout
reset required
Contact Technical
Assistance Service
91
583
EEPROM data loss
EEPROM read/write test
error
Burner lockout
(permanent). Lockout
reset required
Contact Technical
Assistance Service