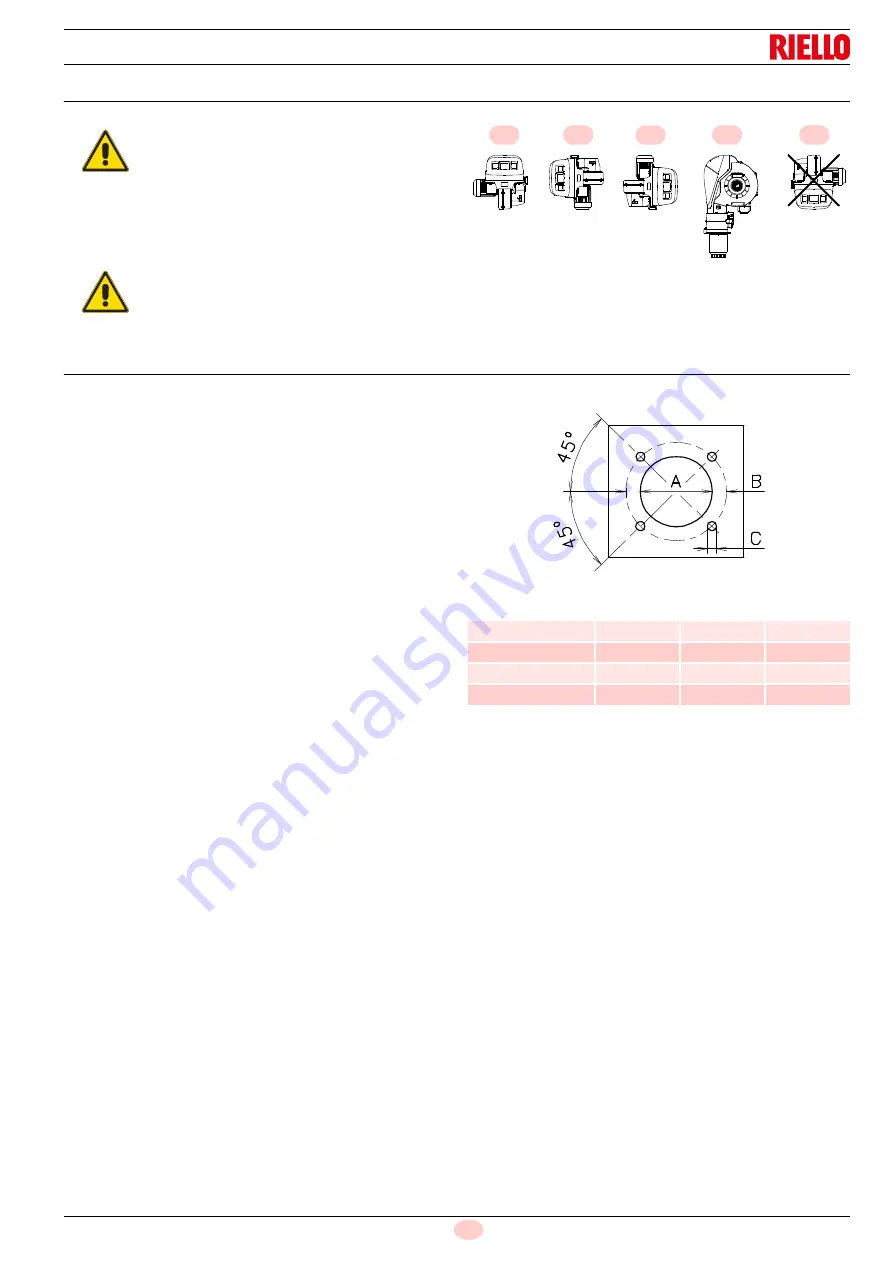
19
20153481
GB
Installation
5.4
Operating position
5.5
Preparing the boiler
5.5.1
Boring the boiler plate
Pierce the closing plate of the combustion chamber, as in Fig. 14.
The position of the threaded holes can be marked using the ther-
mal insulation screen supplied with the burner.
5.5.2
Blast tube length
The length of the blast tube must be selected according to the in-
dications provided by the manufacturer of the boiler, and in any
case it must be greater than the thickness of the boiler door com-
plete with its fettling.
The refractory can have a conical shape (minimum 60°).
For boilers with front flue passes 1)(Fig. 15) or flame inversion
chamber, a protection in refractory material 5) must be inserted
between the boiler fettling 2) and the flame funnel 4).
This protective fettling must not compromise the extraction of the
blast tube.
For boilers with a water-cooled front piece, a refractory lining 2)-
5)(Fig. 15) is not necessary, unless expressly requested by the
boiler manufacturer.
Tab. I
WARNING
The burner is designed to operate only in
positions
1
,
2
,
3
and
4
(Fig. 13).
Installation
1
is preferable, as it is the only
one that allows the maintenance operations
as described in this manual.
Installations
2
,
3
and
4
permit operation but
make maintenance and inspection of the
combustion head more difficult.
DANGER
Any other position could compromise the cor-
rect operation of the appliance.
Installation
5
is prohibited for safety reasons.
Fig. 13
2
3
4
5
1
D7739
mm
A
B
C
RS 310/M BLU
335
452
M18
RS 410/M BLU
335
452
M18
RS 510/M BLU
335
452
M18
RS 610/M BLU
350
452
M18
Fig. 14
D455