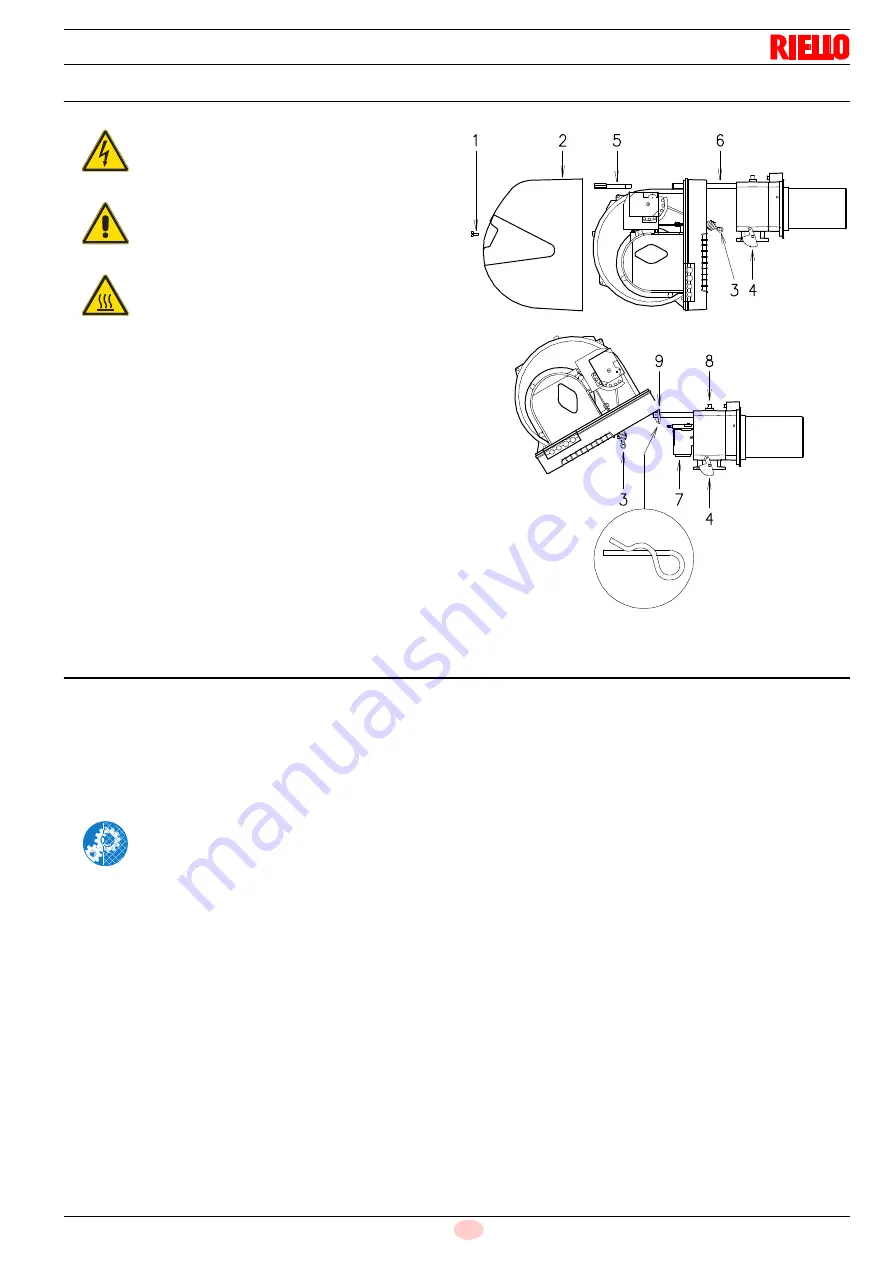
33
20144599
GB
Maintenance
7.3
Opening the burner
Cut off the voltage.
remove the screw 1) and pull out the hood 2).
Disengage the articulated coupling 3) from the graduated
sector 4).
Remove screw 5), the split pin 9) and pull the burner back by
about 100 mm on the slide bars 6.
Disconnect the probe and electrode leads and then pull the
burner fully back.
Turn it as indicated in the diagram, and insert the split pin 9)
into the hole of one of the two guides so that the burner
remains in that position.
Now extract the gas distributor 7) after having removed the screw
8)(Fig. 34).
7.4
Closing the burner
Remove the split pin 9) and push the burner until it is approx.
100 mm from the pipe coupling. Reconnect the cables and
slide in the burner until it comes to a stop. Replace the
screws 5) and split pin 9) and carefully pull the probe and
electrode cables outwards until they are slightly taut.
Reconnect the articulated coupling 3) to the graduated
sector 4).
DANGER
Disconnect the electrical supply from the burner
by means of the main system switch.
DANGER
Close the fuel shut-off valve.
Wait for the components in contact with heat
sources to cool down completely.
Fig. 34
D535
After carrying out maintenance, cleaning or
checking operations, reassemble the cover and
all the safety and protection devices of the burner.
Summary of Contents for RS 28
Page 2: ...Translation of the original instructions ...
Page 40: ...20144599 38 GB Appendix Electrical panel layout K1 RS 28 SINGLE PHASE 20129156 DIAGRAM A ...
Page 41: ...39 20144599 GB Appendix Electrical panel layout K1 RS 38 SINGLE PHASE 20129158 DIAGRAM A ...
Page 42: ...20144599 40 GB Appendix Electrical panel layout K1 RS 38 RS 50 THREE PHASE 20126558 DIAGRAM A ...
Page 43: ...41 20144599 GB Appendix Electrical panel layout RS 28 RS 38 SINGLE PHASE 20143439 DIAGRAM B ...
Page 44: ...20144599 42 GB Appendix Electrical panel layout RS 38 RS 50 THREE PHASE DIAGRAM B 20143440 ...
Page 45: ...43 20144599 GB Appendix Electrical panel layout 20143441 RS 28 RS 38 SINGLE PHASE DIAGRAM C ...
Page 46: ...20144599 44 GB Appendix Electrical panel layout 20143442 RS 38 RS 50 THREE PHASE DIAGRAM C ...