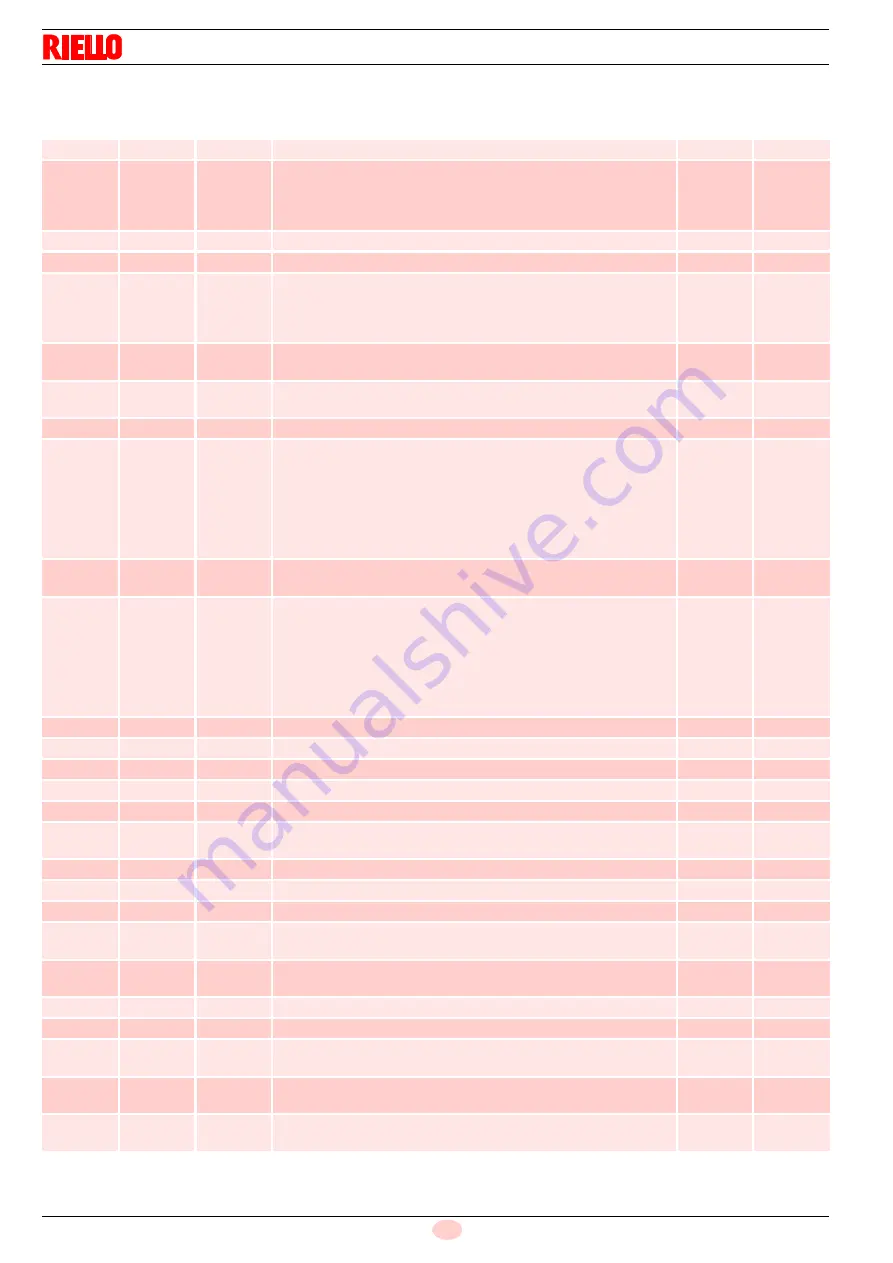
20168262
42
GB
Faults - Possible causes - Solutions
231
Unlimited
3
Fuel/air ration command blocked: Channel
Channel
241
0
0
The actuator does not move, namely no position feedback.
Channel
Direction:
P 2 =
backward,
forward
If this indication appears, the monitoring of fault 271 is damaged.
251
0
0
The actuator does not find the reference position
Channel
Direction:
0 backward
1 forward
Check that the flap moves smoothly towards the reference position.
261
Unlimited
3
The actuator provides an invalid position (too broad a difference
with respect to the target position)
Channel
271
Unlimited
3
The actuator feedback remains constant for too long, also after the
movement of the actuator
Channel
281
1
1
The feedback signal of at least 1 actuator is incorrect
Channel
To identify the rotation direction of the actuator, it sends double
pulse signals, unaligned of 90 degrees.
If fault 281 occurs, these signals are not correctly identified.
Cause of the error:
–
kickback
–
actuator 0.8 Nm: clockwise external torque > 0.2 Nm
–
actuator 9 Nm: clockwise external torque > 1 Nm
291
Optional
3
The actuator does not reach the final position because of a fuzzy
detection.
Channel
The actuators are exchanged during the reconnection. The test for
recognising this fault is described in the BT300 manual - print num-
ber DLT1201.
At least one actuator does not reach its test position:
–
2 actuators are exchanged
–
another problem is preventing the actuator from reaching its
test position
320
1
1
Broken or open cable on the firing rate input
321
1
1
Broken or open cable on the feedback channel: channel number
Channel
351
1
1
Fuel change not valid when the burner is operating
352
Optional
3
Fuel signals combination not valid (no signal)
353
Optional
3
Fuel signals combination not valid (various signals)
360
0
0
The lack of air causes a shutdown due to a fault with the O
2
regu-
lation.
362
0
0
Shutdown die to a fault because of lack of burner maintenance
363
1
1
The smallest O
2
value is adopted
371
0
0
The output for the internal conditions is defective
372
0
0
The difference of burner running values between the main proces-
sor and the watchdog one is too high
381
0
0
The deviation between the main processor and the watchdog con-
trol is too high
Channel
correction
391
0
0
The curve set has changed during programming
393
0
0
Emergency stop activated
394
0
0
The burner ON/OFF signal on the user interface has unexpectedly
stopped
451
1
1
In the operating mode for ignition, not all the channels are in the ig-
nition position
Channel
600
0
0
Programming monitoring time(FAT) exceeded
Reference
number
Error
code
TRD
P301=0
P328>0
EN67
P301=2
P328>0
Description
D1
D2
Summary of Contents for RLS 120/E FGR
Page 2: ...Translation of the original instructions ...
Page 51: ...49 20168262 GB Appendix Electrical panel layout 01 2 3 4506 7 891 01 ...
Page 52: ...20168262 50 GB Appendix Electrical panel layout 0 1 2 2 2 0 ...
Page 54: ...20168262 52 GB Appendix Electrical panel layout 0 0 0 12 3456 7 12 3456 7 ...
Page 57: ...55 20168262 GB Appendix Electrical panel layout 0 0 1 2 3 4 5 667 8 667 2 9 63 8 63 63 3 5 ...