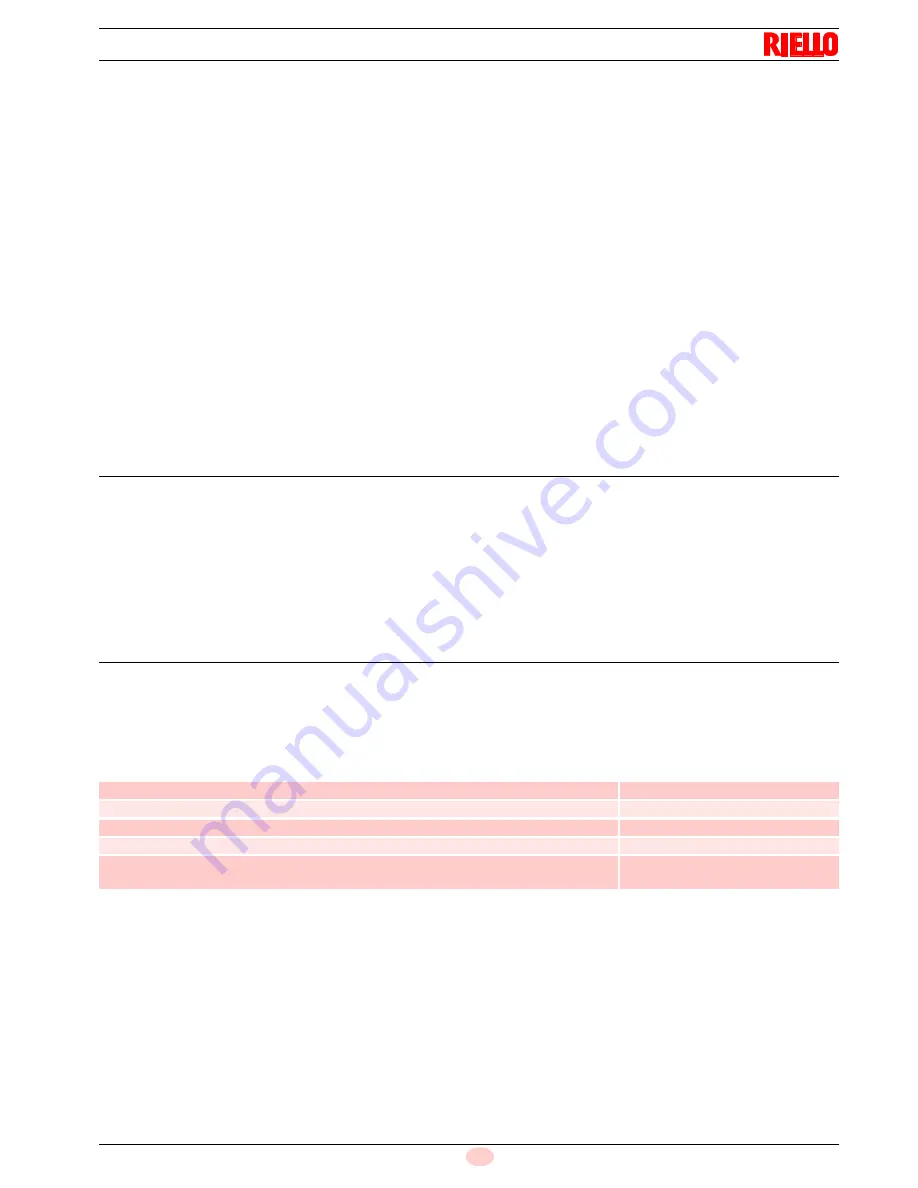
23
20063165
GB
Start-up, calibration and operation of the burner
6.13.10 Internal voltage monitor anomaly
The control-box automatically detects if the internal voltage
works correctly. The anomaly is indicated by the led flashing (see
table).
➤
If the anomaly is detected during the initialisation check time,
the burner does not start.
➤
If the anomaly is detected after a lockout the burner does not
start.
➤
If the anomaly is not detected after a shutdown test the
burner does not start.
➤
The anomaly is not detected during normal operation the
burner remains in this mode.
When the anomaly disappears, the burner restarts.
6.13.11 Reset push-button or remote reset anomaly
If the reset push-button or remote reset are faulty or remains
pressed for more than 60 seconds, the fault will be indicated by
the flashing of the LED (see table) (which continues to flash as
long as the fault is active).
This fault is merely a visualisation.
➤
If the fault is detected during pre-purging or safety time, the
burner does not stop (the start-up sequence will continue).
➤
If the fault is detected during operation, the burner does not
stop (it continues operating, but the fault signal will be
active).
➤
If the fault is detected during a lockout, the fault is not sig-
nalled and the burner cannot be reset.
When the fault disappears, the LED stops flashing.
6.13.12 Checking the fan motor
The control box automatically detects the presence of the fan mo-
tor and, in the event of a fault, it performs a lockout.
The lockout is indicated by led flashing (see table).
6.13.13 Checking the oil valve
The control box automatically detects the state of contacts of re-
lays of the oil valve, in the event of a fault, it performs a lockout.
The lockout is indicated by led flashing (see table).
6.13.14 EEprom check
The control-box automatically detects if EEprom memory of mi-
crocontroller has failed and will perform a lockout.
The lockout is indicated by the led flashing (see table).
6.14
Post-purging
Post-purging is a function that maintains air ventilation even after
the burner is switched off (no heat request).
The burner switches off when the limit thermostat (TL) opens,
cutting off the fuel supply to the valves.
The post-purging function is not performed:
➤
after a lockout
➤
if the heat request is halted during pre-purging;
➤
if the heat request is halted during safety time.
NOTE:
If during post-purging there is an extraneous light, the burner
blocks after 25 seconds.
If during post-purging there is a new heat request, post-purging
time is halted fan motor stop and a new burner operating cycle
starts if the heat request thermostat switches off.
6.15
Automatic pre-heating disabling
It is possible to disable the pre-heater function in automatic mode
by pressing the reset push-button.
When the pre-heating is disabled, the pre-heating remains off un-
til:
– a lockout occurs
– the main supply voltage is interrupted
– intermittent operation (reset after 1 hour or 24 hours)
Tab. G
Sequence of pre-heating deactivation
The colour of the LED
button becomes
Pre-heating deactivation is only permitted if there is no lockout or fault
-
Pre-heating deactivation is only permitted by means of the remote reset button
-
Supply the burner and simultaneously maintain pressed the remote reset for 3 sec.
RED
Release the remote reset button within 3 seconds
OFF
The burner will only begin the pre-heating deactivation and the purging restart if the remote
reset button has been released within 3 seconds
-