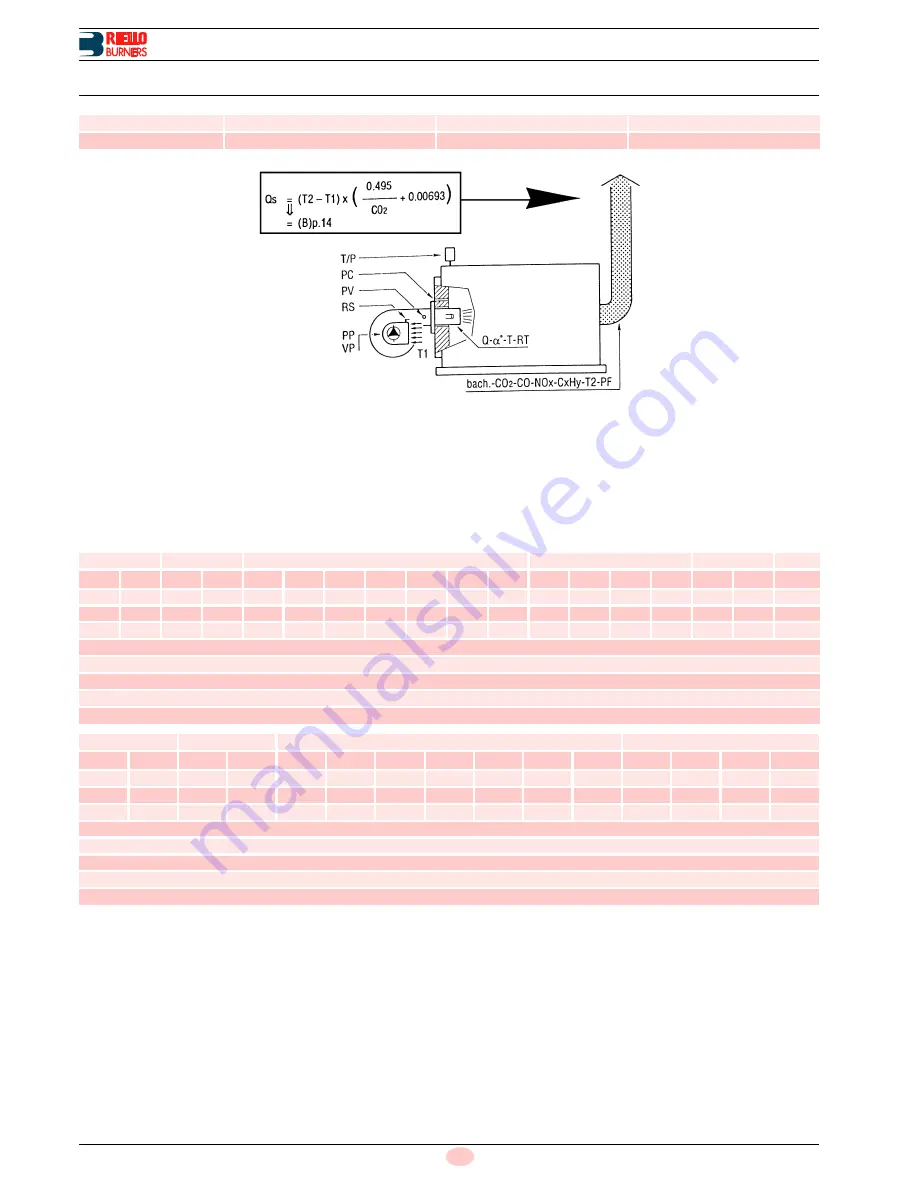
20033090
34
GB
Faults - Possible causes - Solutions
9.3
Control card
Q
= Delivery
α
°-T
= Angle and type of spray (Tab. G on page 17)
PP
= Pump delivery pressure
VP
= Pump suction pressure or depressure
BACH = Bacharach
CO
2
= Carbon dioxide
CO
= Carbon monoxide
NOx
= Nitrogen oxide
CxHy
= Uncombusted hydrocarbons
T2
= Temperature
PF
= +/- pressure at stack
T1
= Temperature
PV
= Fan pressure
RT
= Combustion head adjustment
RS
= Fan gate valve adjustment
T/P
= Temperature or pressure
PC
= Comb. chamber pressure
Qs
= Heat loss at stack
BURNER
MODEL
TYPE
CODE
BOILER
COMPANY
MODEL
kW
Fig. 36
D390
NOZZLE
PUMP
FLUE GASES
AIR
BOILER
STACK
Q
α
°-T
PP
VP
BACH
CO
2
CO
NOx
CxHy
T2
PF
T1
PV
RT
RS
T/P
PC
Qs
GPH
bar
bar
N°
%
ppm
ppm
ppm
°C
mbar
°C
mbar
n°
n°
°C/bar mbar
%
NOZZLE
PUMP
FLUE GASES
AIR
Q
α
°-T
PP
VP
BACH
CO
2
CO
NOx
CxHy
T2
PF
T1
PV
RT
RS
GPH
bar
bar
N°
%
ppm
ppm
ppm
°C
mbar
°C
mbar
n°
n°