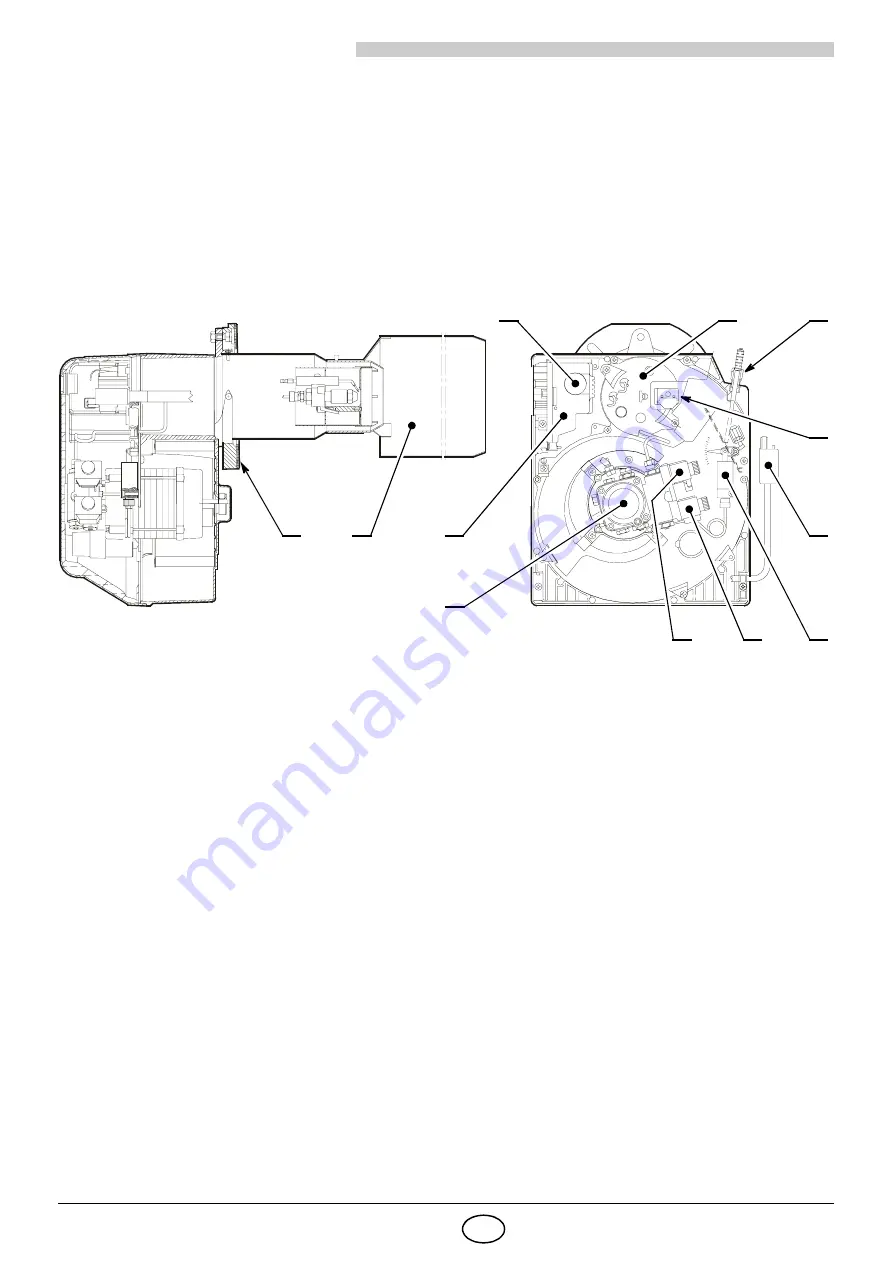
3066
2
GB
1.
BURNER DESCRIPTION
1.1
BURNER EQUIPMENT
Flange with insulating gasket . . . . . . No. 1
Screw and nuts for flange to be fixed to boiler . . . .No. 4
Screw and nuts for flange . . . . . . . . No. 1
Flexible oil pipes with nipples. . . . . . . . . . . . . . . . .No. 2
4 pin plug . . . . . . . . . . . . . . . . . . . . No. 1
Remote reset connection. . . . . . . . . . . . . . . . . . . . .No. 1
1.2 ACCESSORIES
SOFTWARE DIAGNOSTIC KIT
A special kit is available that, by an optical link to a PC, shows the burner life together with operating hours, type
and number of failures, serial number, etc.
To visualise the diagnostics proceed as follows:
³
Connect the kit supplied separately to the control box socket.
Reading of the information begins when the software programme included in the kit starts.
REMOTE RESET KIT
The burner has a remote reset kit (
RS
) consisting of a connection and a push-button operating at a dis-
tance of 20 metres max.
In order to install it remove the protective lock-out installed at the factory and insert the lock-out supplied
with the burner (see electrical diagram on page 8).
1
– Pump with pressure reducer
2
– Blast tube
3
– Control box
4
– Reset button with lock-out lamp
5
– Flange with insulating gasket
6
– 2
nd
stage air damper adjustment assembly
Two stage light oil burner with low pollutant emissions (Nitric Oxide NOx, Carbon monoxide CO and unburnt
Hydrocarbons). The dimension of the boiler’s combustion chamber must respond to specific values, in order
to guarantee a combustion with the lowest polluting emissions rate. The
RIELLO
Technical Service
Personnel will be glad to give you all the imformation for a correct matching of this burner to the boiler.
³
CE Certification No.:
0036 0269/99
as 92/42/EEC.
³
The burner meets protection level of IP X0D (IP 40) as EN 60529.
³
Burner with CE marking in conformity with EEC Directives: EMC 89/336/EEC, Low Voltage 73/23/EEC,
Machines 98/37/EEC and Efficiency 92/42/EEC.
³
The burner is approved for intermittent operation as per standard EN 267.
7
– Nozzle holder assembly
8
– Flame detector
9
– Hydraulic jack
10
– 4 pole socket
11
– 2
nd
stage valve
12
– 1
st
stage valve
1
6
8
7
10
12
11
9
4
2
5
3
Fig. 1
D4683