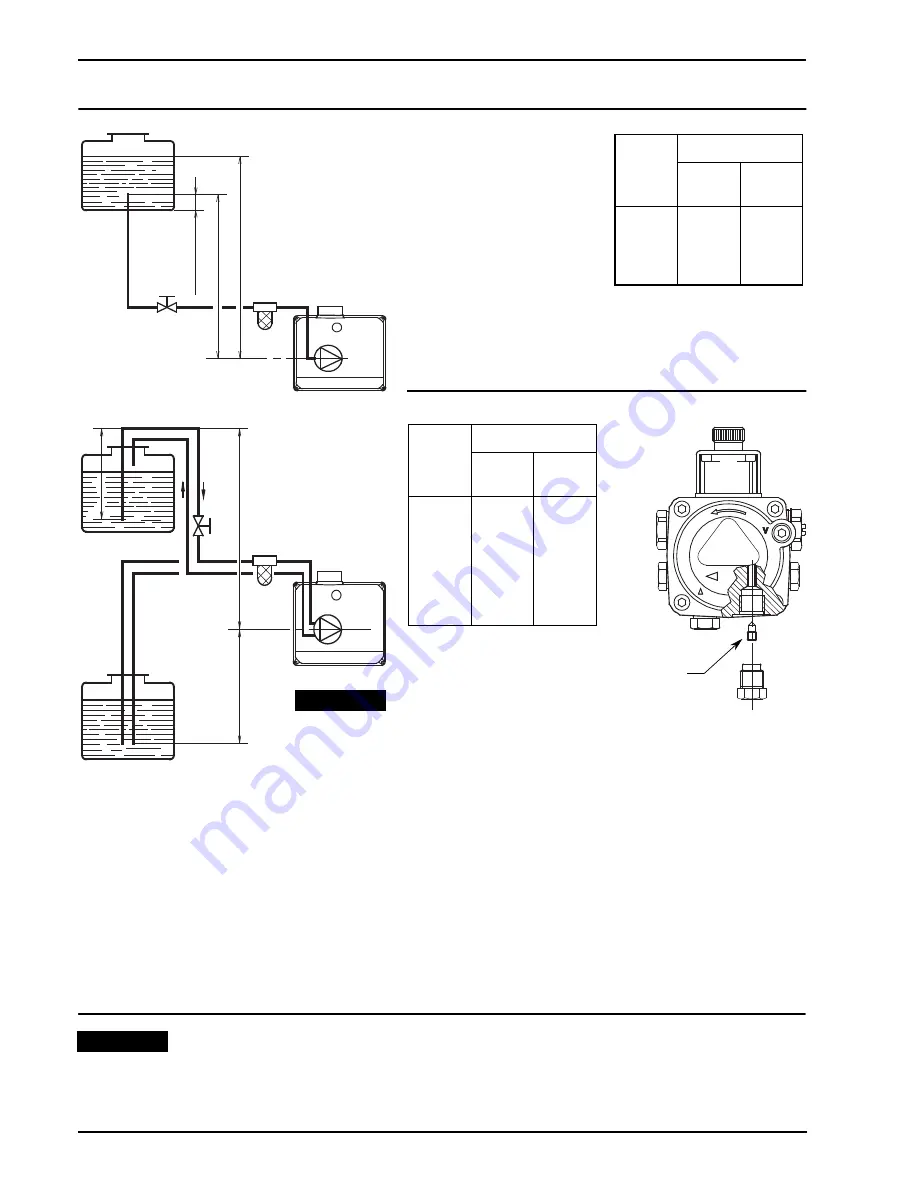
2136
4
OIL LINES
H
meters
L meters
I. D.
8 mm
I.D.
10 mm
0.5
1
1.5
2
10
20
40
60
20
40
80
100
PRIMING THE PUMP
Loosen the plug of the vacuum gauge (4, fig. 1, page 1)
and wait until the fuel flows out.
H
meters
L meters
I. D.
8 mm
I.D.
10 mm
0
0.5
1
1.5
2
3
3.5
35
30
25
20
15
8
6
100
100
100
90
70
30
20
max.
4 m
H
H
max.
4 m
min.
0.1 m
D5307
D5308
H
The pump vacuum should not exceed a maximum of 0.4 bar (30 cm Hg). Beyond this limit gas is released
from the oil. Oil lines must be completely airtight. The return line should terminate in the oil tank
at the same level as the suction line; in this case a non-return valve is not required.
Should however the return line arrives over the fuel level, the non-return valve is indispensable.
This solution however is less safe than previous one, due to the possibility of leakage of the valve.
PRIMING THE PUMP:
Start the burner and wait for the priming. Should lock-out occur prior to the arrival of the fuel, await at
least 20 seconds before repeating the operation.
WARNING: Before starting the burner make sure that the return pipe-line is not clogged: any
obstruction would cause the pump seals to break.
■
Check periodically the flexible pipes conditions.
Using kerosene, they have to be replaced at least every 2 years.
■
A metal bowl filter with replaceable micronic filter must be fitted in the oil supply pipe.
WARNING
A
D5199
The pump is supplied for use with a one pipe system.
For use on a two pipes system, it is necessary to screw the
BY-PASS SCREW (A) supplied with kit code 3000970.
WARNING
H =
Difference of level.
L
= Max.
length of the suction line.
I.D. =
Internal diameter of the oil pipes.