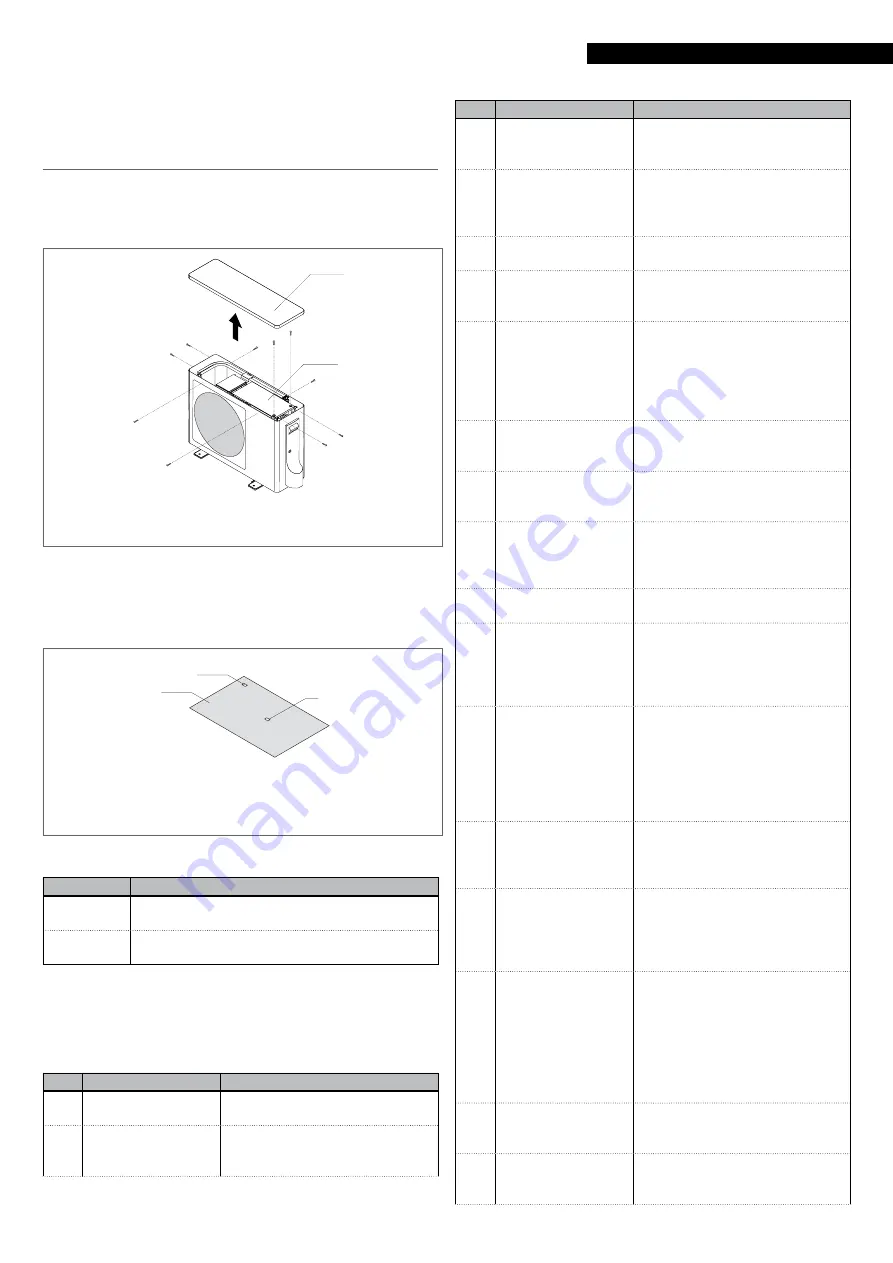
COMMISSIONING AND MAINTENANCE
25
9
Carefully check for absence of leakages from the closing
point of the plug.
3.4 Operation signal and alarms
Signals are displayed by means of LEDs on the unit main elec-
tronic board.
Proceed as follows to access the filters:
1 Upper panel
2 Electric panel cover
1
2
—
unscrew the fastening screws
—
remove the top panel
—
unscrew the fastening screws
—
remove the electric panel cover
1 Main electronic board
2 Led 2
3 Led 1
1
2
3
The unit operation is signalled with LED 2.
led 2
Description
On
Indicates that the unit is supplied with
electricity
Off
Indicates that the unit is not supplied with
electricity
After the LED switches off:
9
Wait 10 minutes before touching the device electric compo-
nents.
Faults are signalled by means of LED 1 blinking.
led 1 Description
Remarks
1
External unit
microprocessor fault
The unit resets after problem
resolution
2
Power module fault
After 3 consecutive interventions
in 10 minutes, the unit resets
after problem resolution
led 1 Description
Remarks
3
Main electronic
board protection
against overcurrent
After 3 consecutive interventions
in 30 minutes, the unit resets
after problem resolution
4
Communication
error between main
board and power
module
The alarm activates 4 minutes
after the unit start
The unit resets after problem
resolution
6
Wrong power supply
voltage
The unit resets after problem
resolution
7
Compressor lockout
After 3 consecutive interventions
in 10 minutes, the unit resets
after problem resolution
8
Overheat protection
for compressor
discharge
The unit resets automatically
when the temperature drops
under 110°C
After 3 consecutive interventions
in 30 minutes, the unit resets
after problem resolution
9
Fan motor
malfunction
After 3 consecutive interventions
in 30 minutes, the unit resets
after problem resolution
10
Defrost
temperature sensor
failure
The unit resets after problem
resolution
11
Suction probe
fault or suction
overtemperature
The unit resets automatically
when the temperature drops
under 40°C or after problem
resolution
12
External air probe
fault
The unit resets after problem
resolution
13
Discharge
temperature sensor
failure
The alarm activates 4 minutes
after the unit start
After 3 consecutive interventions
in 30 minutes, the unit resets
after problem resolution
14
Compressor suction
overtemperature
The alarm activates 10 minutes
after the unit start
The alarm activates if
temperature exceeds 40°C for 5
consecutive minutes
The alarm resets after problem
resolution
15
Communication
error between
outdoor and indoor
unit
The alarm activates 4 minutes
after the unit start
The unit resets after problem
resolution
16
Lack of refrigerant
The alarm activates 5 minutes
after the unit start
After 2 consecutive interventions
in 20 minutes, the unit resets
after problem resolution
17
4-way valve
malfunction
The alarm activates 5 minutes
after the unit start
The alarm activates when, in
Heating mode, the temperature
detected by the indoor unit heat
exchanger probe is less than or
equal to 15°C for 1 minute and for
3 times in an hour
18
Deviate from the
normal for the
compressor
The unit resets after problem
resolution
19
Power module
malfunction
After 3 consecutive interventions
in 10 minutes, the unit resets
after problem resolution