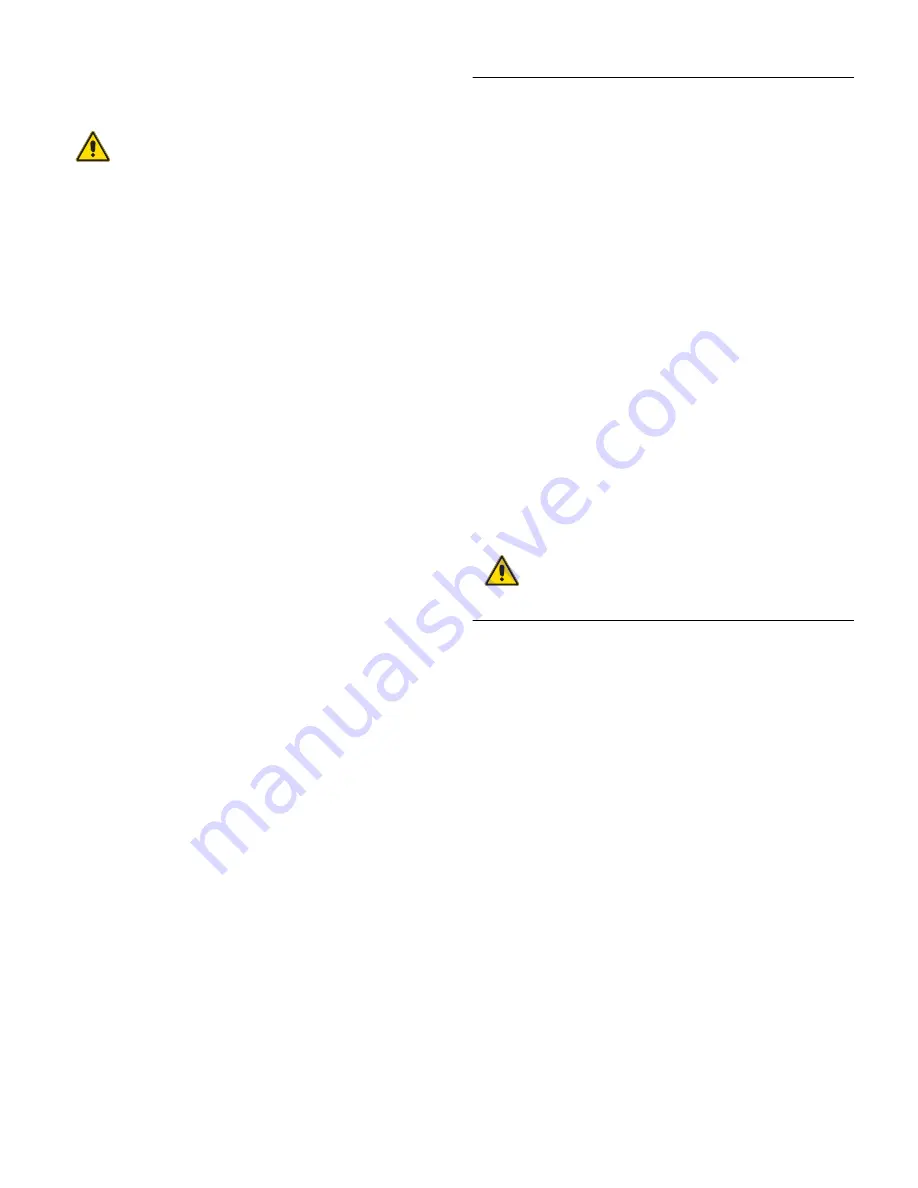
2
GUARANTEE AND RESPONSIBILITY
The manufacturer guarantees its new products from the installation date,
in accordance with the regulations in force and/or the sales contract. At
the moment of the first start-up, check that the burner is integral and com-
plete.
In particular, the rights to the guarantee and the responsibility will no lon-
ger be valid, in the event of damage to things or injury to people, if such
damage/injury was due to any of the following causes:
- incorrect installation, start-up, use and maintenance of the burner;
- improper, incorrect or unreasonable use of the burner;
- intervention of unqualified personnel;
- carrying out of unauthorised modifications on the equipment;
- use of the burner with safety devices that are faulty, incorrectly
applied and/or not working;
- installation of untested supplementary components on the burner;
- powering of the burner with unsuitable fuels;
- faults in the fuel supply system;
- use of the burner even following an error and/or an irregularity;
- repairs and/or overhauls incorrectly carried out;
- modification of the combustion chamber with inserts that prevent the
regular development of the structurally established flame;
- insufficient and inappropriate surveillance and care of those burner
components most likely to be subject to wear and tear;
- the use of non-original components, including spare parts, kits,
accessories and optional;
- force majeure.
The manufacturer furthermore declines any and every responsibili-
ty for the failure to observe the contents of this manual.
SAFETY AND PREVENTION
INTRODUCTION
The burners have been designed and built in compliance with current
regulations and directives, applying the known technical rules of safety
and envisaging all the potential danger situations.
It is necessary, however, to bear in mind that the imprudent and clumsy
use of the equipment may lead to situations of death risk for the user or
third parties, as well as the damaging of the burner or other items. Inat-
tention, thoughtlessness and excessive confidence often cause acci-
dents; the same applies to tiredness and sleepiness.
It is a good idea to remember the following:
- The burner must only be used as expressly described. Any other use
should be considered improper and therefore dangerous.
In particular:
it can be applied to boilers operating with water, steam, diathermic oil,
and to other uses expressly named by the manufacturer;
the type and pressure of the fuel, the voltage and frequency of the elec-
trical power supply, the minimum and maximum deliveries for which the
burner has been regulated, the pressurisation of the combustion cham-
ber, the dimensions of the combustion chamber and the room tempera-
ture must all be within the values indicated in the instruction manual.
- Modification of the burner to alter its performance and destinations is
not allowed.
- The burner must be used in exemplary technical safety conditions.
Any disturbances that could compromise safety must be quickly elim-
inated.
- Opening or tampering with the burner components is not allowed,
apart from the parts requiring maintenance.
- Only those parts envisaged by the manufacturer can be replaced.
PERSONNEL TRAINING
The user is the person, body or company that has acquired the machine
and intends to use it for the specific purpose. He is responsible for the
machine and for the training of the people working around it.
The user:
- undertakes to entrust the machine exclusively to suitably trained and
qualified personnel;
- undertakes to inform his personnel in a suitable way about the appli-
cation and observance of the safety instructions. With that aim, he
undertakes to ensure that everyone knows the use and safety
instructions for his own duties;
- Personnel must observe all the danger and caution indications
shown on the machine.
- Personnel must not carry out, on their own initiative, operations or
interventions that are not within their province.
- Personnel must inform their superiors of every problem or dangerous
situation that may arise.
- The assembly of parts of other makes, or any modifications, can alter
the characteristics of the machine and hence compromise operating
safety. The manufacturer therefore declines any and every responsi-
bility for any damage that may be caused by the use of non-original
parts.
Failure to observe the information given in this manual, op-
erating negligence, incorrect installation and carrying out
of non authorised modifications will result in the annulment
by the manufacturer of the guarantee that it supplies with
the burner.
WARNING
The manufacturer guarantees safety and proper function-
ing only if all burner components are intact and positioned
correctly.
WARNING
Summary of Contents for 9511300
Page 2: ...Original instructions...