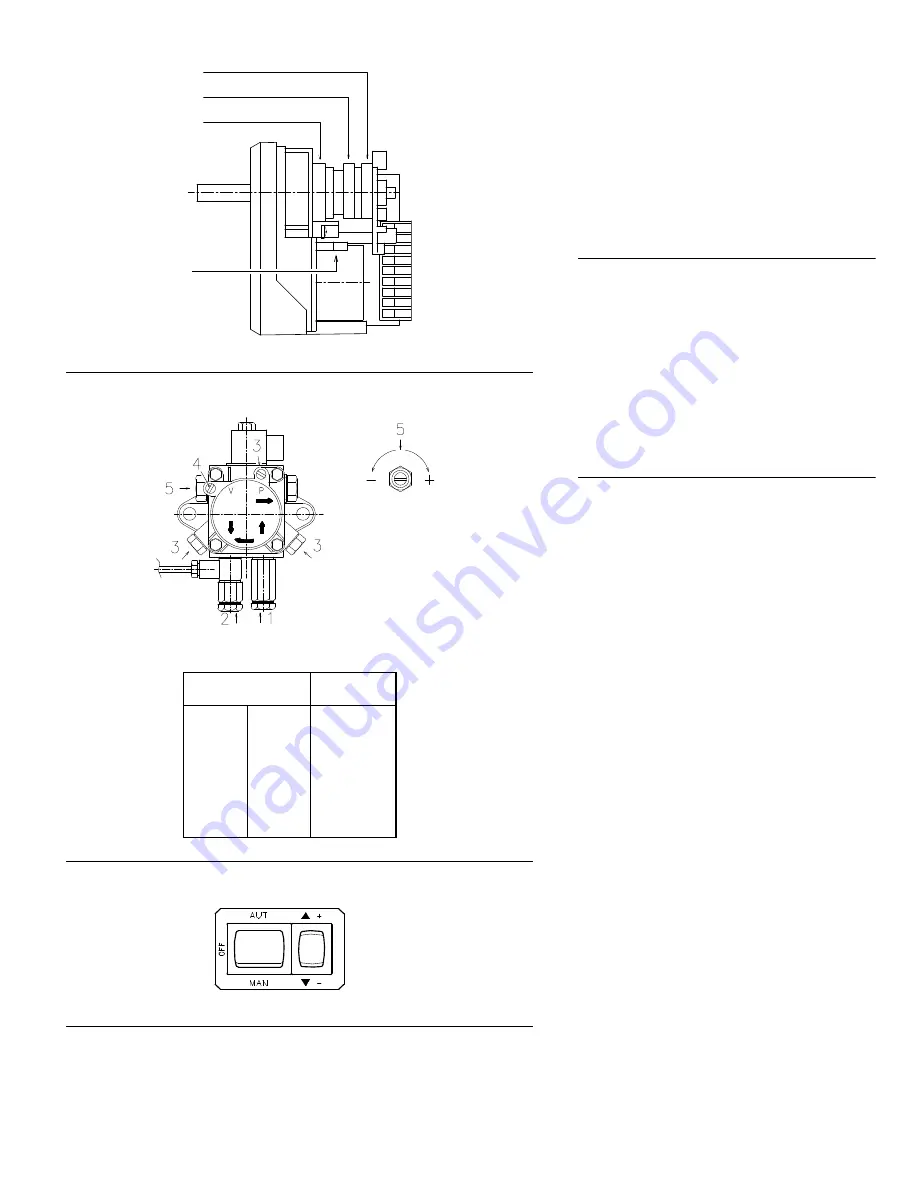
8
SERVOMOTOR (A)
The servomotor provides simultaneous adjustment of the
air damper 11)(B) page 9 and the pressure regulator 9)
by means of a double variable profile cam, 4) and 7). The
servomotor rotates through 90° in 25 seconds.
Do not alter the factory setting for the cams; simply
check that they are set as indicated below:
Red cam
: 90°
Limits rotation toward maximum position.
Blue cam
: 0°
Limits rotation toward the minimum position. When the
burner is shut down the air damper must be closed: 0°.
Orange cam
: 15°
Adjusts the ignition position and the MIN output.
PUMP (B)
1 - Suction
1/4” NPT
2 - Return
1/4” NPT
3 - Pressure gauge attachment G 1/8”
4 - Vacuum gauge attachment
G 1/8”
5 - Pressure adjustment screw
A - Min. delivery rate at 290 PSI pressure
B - Delivery pressure range
C - Max. suction pressure
D - Viscosity range
E - Max fuel oil temperature
F - Max. suction and return pressure
G - Pressure calibration in the factory
H - Filter mesh width
PUMP PRIMING
•
Before starting the burner, make sure that the tank
return line is not clogged. Obstructions in the line
could cause the seal located on the pump shaft to
break.
• In order for self-priming to take place, one of the
screws 3)(B) of the pump must be loosened to bleed
off the air contained in the suction line.
• Start the burner by closing the control circuit with
switch 1)(C) in the "MAN" position. As soon as the
burner starts, check the direction of rotation of the fan
blade, by looking through the flame inspection window
19)(A)p.4.
• The pump can be considered primed when the fuel oil
starts coming out of the screw 3). Stop the burner:
switch 1)(C) set to "OFF" and tighten the screw 3).
The time required for this operation depends upon the
diameter and length of the suction tubing. If the pump
fails to prime at the first cycle of the burner and the
burner locks out, wait approx. 15 seconds, reset the
burner, and then repeat the starting operation as often
as required. After 5 or 6 starting operations allow 2 or 3
minutes for the transformer to cool.
Important
The priming operation is possible because the pump is
already full of fuel when it leaves the factory. If the pump
has been drained, fill it with fuel through the opening for
the vacuum gauge prior to starting; otherwise, the pump
will seize. Whenever the length of the suction piping
exceeds 66 - 99 ft, the supply line must be filled using a
separate pump.
(C)
(A)
(B)
SUNTEC AL 95 C
D2286
AL 95 C
A
B
C
D
E
F
G
H
GPH
PSI
“Hg
cSt
°F - °C
PSI
PSI
inch
32
145 - 290
13
2 - 12
140 - 60
29
290
0,006
1
2
D791
BLUE CAM
RED CAM
ORANGE CAM
D2522
RESET
Summary of Contents for 9511300
Page 2: ...Original instructions...