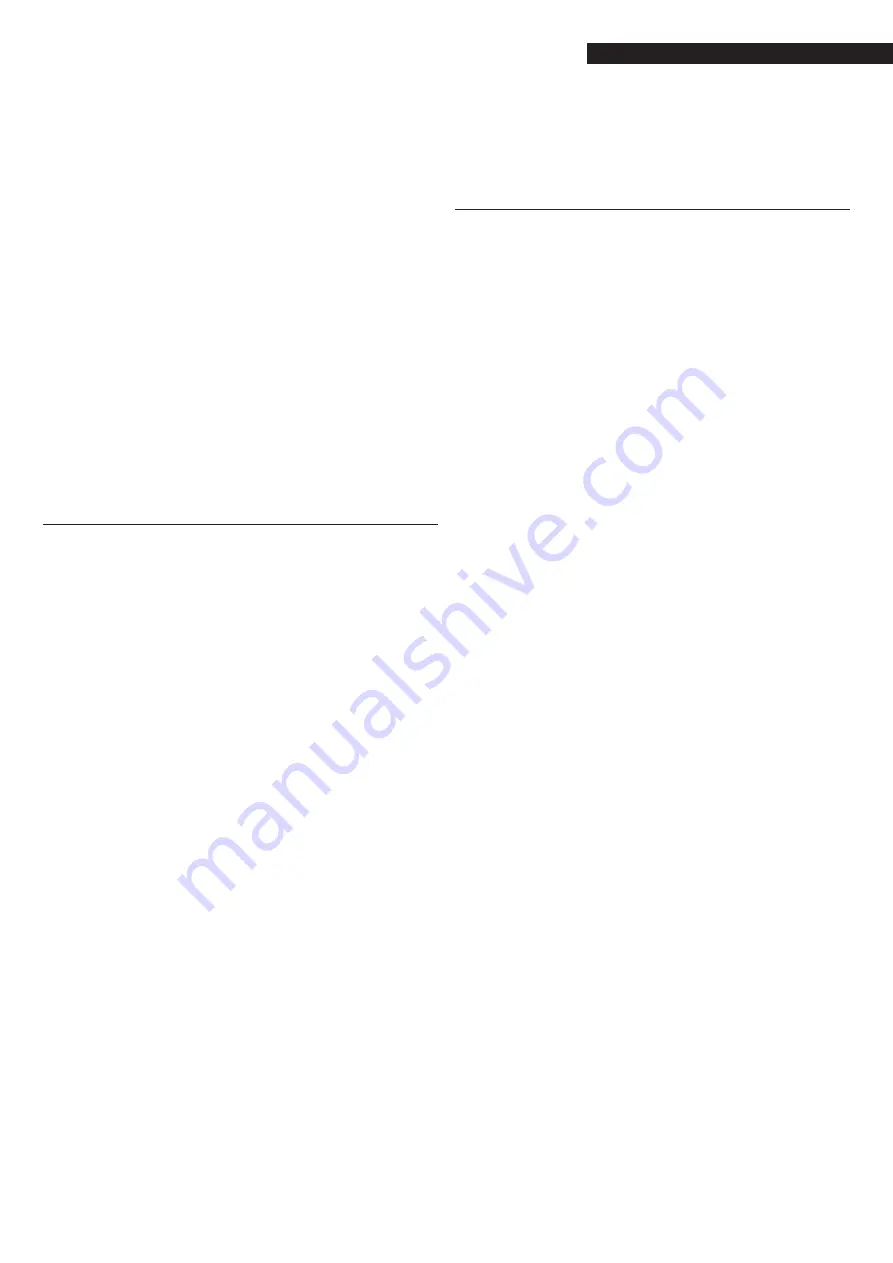
15
the boiler room.
First checks in the event of a fault
When the burner or a boiler has a fault, check the following be-
fore calling for assistance. Do not carry out any other interven-
tion except for the controls indicated. After these checks, contact
the technical assistance service.
If the boiler stops and does not restart, the stop could have been
caused by the safety thermostat due to the overheating of the
water in the boiler. In this case, wait for the boiler to cool down
and carry out the following checks.
− Check that the fuel is being correctly supplied to the
burner. If necessary, restore the fuel supply to the burner.
− Check that the pump is working. If the pump has stopped
it could be the cause of the overheating. Contact the
pump's manufacturer or distributor.
− Check the position of the valves. If the valves are closed,
open them. Press the switch of the safety thermostat
when the boiler has cooled down enough.
− The burner should start.
− If the boiler does not start, or if the safety thermostat
stops the boiler again, contact the technical assistance
service.
− If the warning light of the burner is on, consult the burn-
er's instruction manual or contact the appliance's man-
ufacturer or dealer.
1.22
Maintenance instructions
The boiler and burner checks are carried out: daily (daily use),
periodically and annually.
Daily checks
The user should carry out these checks daily in the season when
the boiler is used every day. Read and follow the instructions
for the daily checks in the chapter “Preliminary checks” in the
manual.
Periodic checks
To perform efficiently, to prevent faults and to prolong the boil-
er's life, it is important to carry out periodic checks. We recom-
mend these checks be carried out once every three months. Pe-
riodic checks are carried out by the technicians as follows:
− Checking and cleaning, if necessary, of the combustion
chamber and the passageways of the boiler smoke.
− Checking for water leaks going into and coming out of the
boiler and checking the flue gases pipe fitting seal.
− Checking the valves.
− Checking the pumps.
− Checking and cleaning, if necessary, the fuel filter.
− Checking the combustion (visual). Adjusting the burner
and flame, if necessary.
− Checking and cleaning, if necessary, the liquid fuel sen-
sor.
− Checking the operation and safety of the burner and the
boiler.
Annual checks
The annual checks should be carried out by technicians before
the start of the season. The flue gases pipe and the relative fit-
tings need to be cleaned before requesting the intervention of
technicians for the annual checks. In the annual checks, the
technicians assess the following:
− Conditions and sealing of the elements and the insulat-
ing cords.
− Operating pressure for adjusting the combustion with the
combustion gas measurement system, if necessary.
− Sensors and connection of the sensors.
− Boiler combustion chamber and any formations of soot
in the flue gas passages; cleaning after checking.
− Fastening and seal of the boiler door.
− Seals of the boiler fittings.
− Correct opening and closing of the valves.
− Fuel filter and eventual cleaning.
− Burner liquid sensor with cleaning or replacement.
− Operation and safety of the burner and the boiler.
1.23
Cleaning the boiler
Before carrying out this work on the boiler, switch off the electri-
cal supply with the master switch, close the fuel valves and pro-
tect the control panel and the burner so as not to damage them.
Cleaning the flue gas passages
The formation of soot on the heating surfaces can lead to an
increase in the temperature of the fumes by up to 100° above
normal, leading to a yield reduction of 5%.
− Remove the M16 screws and the nuts from the four hinges
that connect the burner door to the front and then open
the door.
− Clean the combustion chamber, extract the turbulators
and the horizontal flue gas passages (second and third
passage).
− Clean the turbulators and put them back in the channels.
− Close the door of the burner securely.
− During this cleaning operation, a layer of soot could form
in the flue gas outlet zone. The soot can be removed by
separating the horizontal passages from the flue pipe.
− After this operation, put back the screws and check the
door seal.
The frequency of the cleaning changes depending on the type of
fuel used by the boiler and the period it is used. When cleaning
the boiler, check the ceramic fibre cords that insulate the door
from the front element and the flue gases pipe from the rear
element and replace them if necessary.