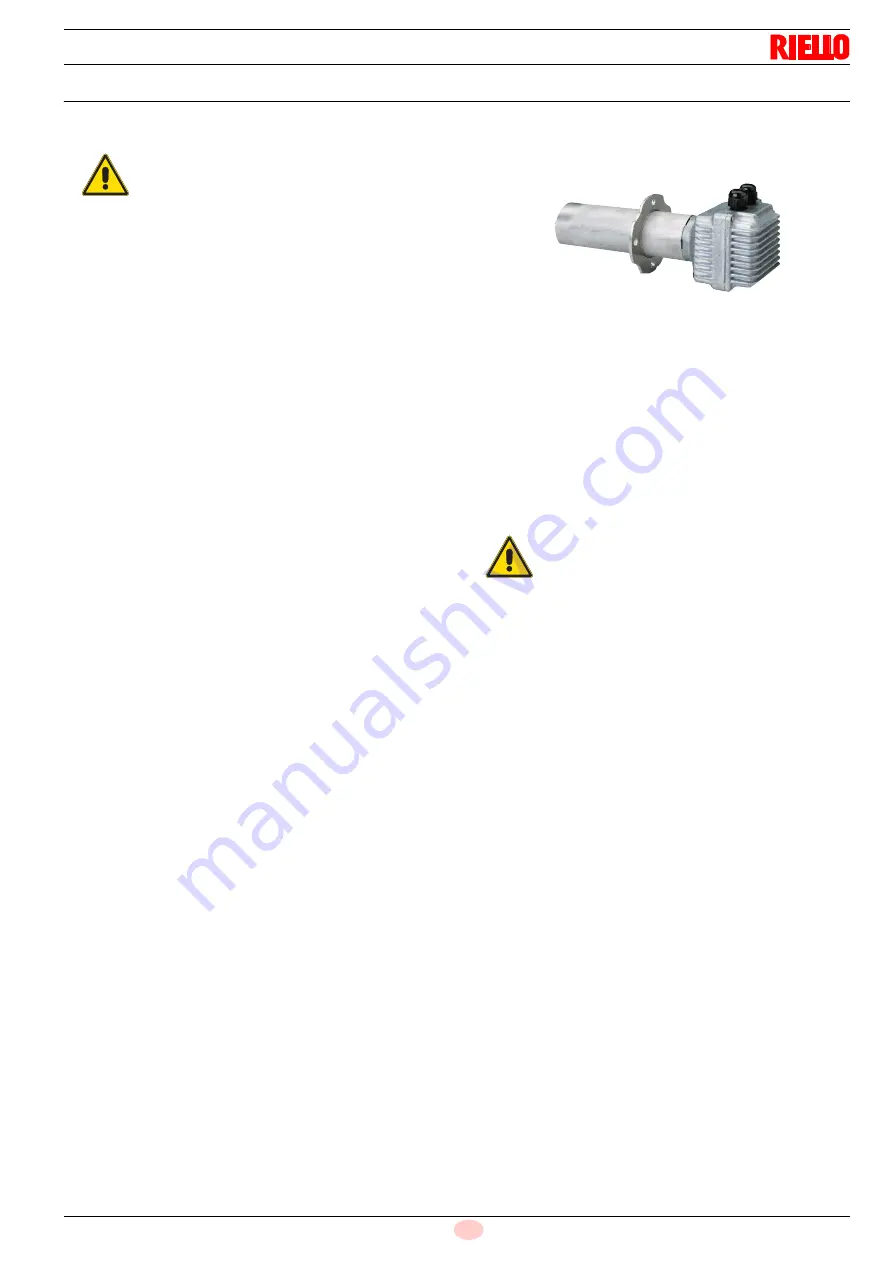
19
20173117
GB
Technical description of the burner
4.15 Oxygen sensor QGO20 ... (optional)
Warnings
All interventions (assembly and installation operations,
assistance, etc.) must be carried out by qualified personnel.
Before modifying the wiring in the sensor connection area,
fully disconnect the burner control device from the power
supply (omnipolar separation).
Ensure that the sensor cannot be inadvertently switched on
again and check this by making a voltage test.
To avoid the risk of electrocution, protect the connection ter-
minals in a suitable manner and correctly fix the cover.
During operation, the flange of the sensor connection must
be kept closed; all screws must be tightened securely.
Check the wiring is in order.
Falls and collisions can negatively affect the safety func-
tions. In this case, the unit must not be operated, even if it
displays no evident damage.
Ensure that the device does not get into contact with explo-
sive or inflammable gases.
There is a risk of burning since the measuring cell works at
an operating temperature of 700 °C and other accessible
parts can get very hot too (> 60 °C).
To prevent injury caused by the hot immersion tube, remove
the device only after the equipment has cooled down.
Make certain that the sensor’s inlet and outlet are always
kept free from dirt.
Before cleaning the inlet and outlet, allow the sensor to cool
down for at least 1 hour.
Mount the sensor such that the connecting part (head to
flange) is free so that the exchange of air is ensured.
Otherwise, measurements might get distorted, possibly lea-
ding to dangerous situations.
Ensure that there are no chemicals, such as solvent vapors,
near the sensor.
Installation notes
The flue gas flow passing the measuring cell must be homo-
geneous, with no or only little turbulence. When mounted too
close to air dampers or pipe bends, faulty measurements
can occur.
A number of faults can distort the measurements (this can
lead to dangerous situations in connection with oxygen trim
control):
– If the stack is not tight, false air can join the flue gases.
– In that case, the residual oxygen content indicated by the
sensor is higher than it actually is.
– If the flue gas velocity is low, the sensor’s response is
slower, since the flue gases take more time to pass the
measuring cell. In that case, it is recommended to mount
the sensor in an inclined position (refer to the manual).
– The greater the sensor’s distance from the flame, the lon-
ger the dead time.
NOTE:
For further explanations about the wiring connetions, please
refer to the manual supplied with the accessory code
20045187.
WARNING
To avoid accidents, material or environmen-
tal damage, observe the following instruc-
tions!
Avoid opening, modifying or forcing the oxy-
gen sensor.
WARNING
Condensation, formation of ice and the entrance
of water are not permitted!
S9895
Fig. 9
Summary of Contents for 1135T1
Page 2: ...Translation of the original instructions...
Page 29: ...27 20173117 GB Installation Fig 20 No Setpoint air gas Max burner output kW 20081480...
Page 53: ...51 20169327 GB Appendix Electrical panel layout ALL MODELS RS 310 RS 410 DIRECT START UP...
Page 54: ...20169327 52 GB Appendix Electrical panel layout RS 310 RS 610 STAR TRIANGLE START UP...
Page 57: ...55 20169327 GB Appendix Electrical panel layout ALL MODELS...
Page 58: ...20169327 56 GB Appendix Electrical panel layout ALL MODELS...
Page 59: ...57 20169327 GB Appendix Electrical panel layout 0 ALL MODELS...
Page 61: ...59 20169327 GB Appendix Electrical panel layout 0 1 1 1 2 ALL MODELS...