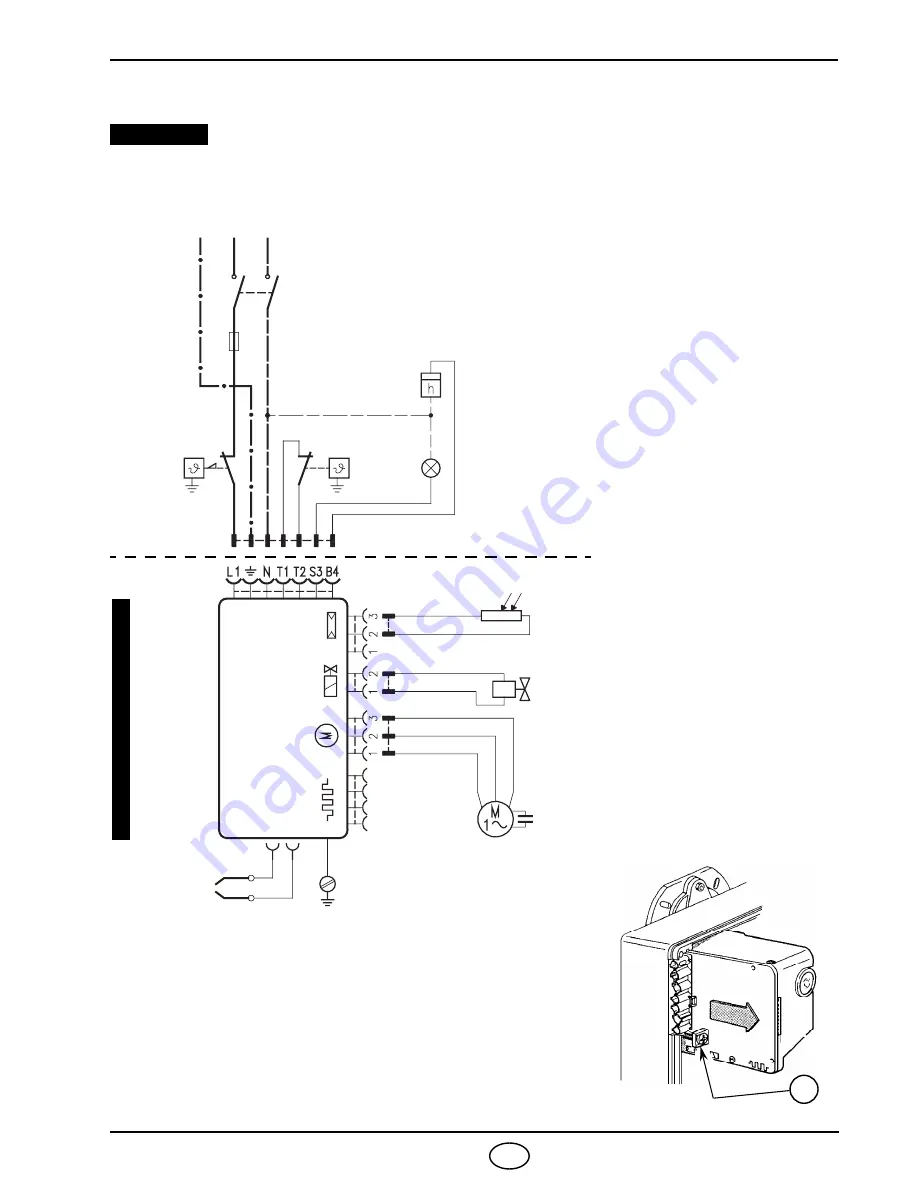
2623
5
GB
3.4
ELECTRICAL WIRING
D1913
ESEGUITO IN FABBRICA
TESTING
Check the shut-down of the
burner by opening the thermo-
stats and the lock-out by dark-
ening the photoresistance.
NOTES:
– Wires of min. 1 mm
2
section.
(Unless requested otherwise by local standards
and legislation).
– The electrical wiring carried out by the installer
must be in compliance with the rules in force in
the Country.
WARNING
DO NOT EXCHANGE NEUTRAL WITH PHASE
7 pin plug
7 pole socket
Black
White
Capacitor
Main switch
T6A
Motor
Blue
Oil valve
Hour counter
(230V - 0.1A max.)
Limit thermostat
Remote lock-out signal
(230V - 0.5A max.)
Ignition
electrodes
Brown
Burner-earth
CARRIED-OUT IN THE FACTORY
552
SE
CONTR
OL BO
X
Photoresistance
PE
L
N
~
50Hz 230V
Blue
CONTROL BOX (see fig. 11)
To remove the control-box from the burner, loosen screw (A) and
pull to the arrow direction, after removing all components, the
7 pin plug and earth wire.
In case of disassembly of the control box, retighten the screw
(A) with a torque wrench setting of 1 – 1.2 Nm.
Fig. 11
S7072
A
Safety thermostat