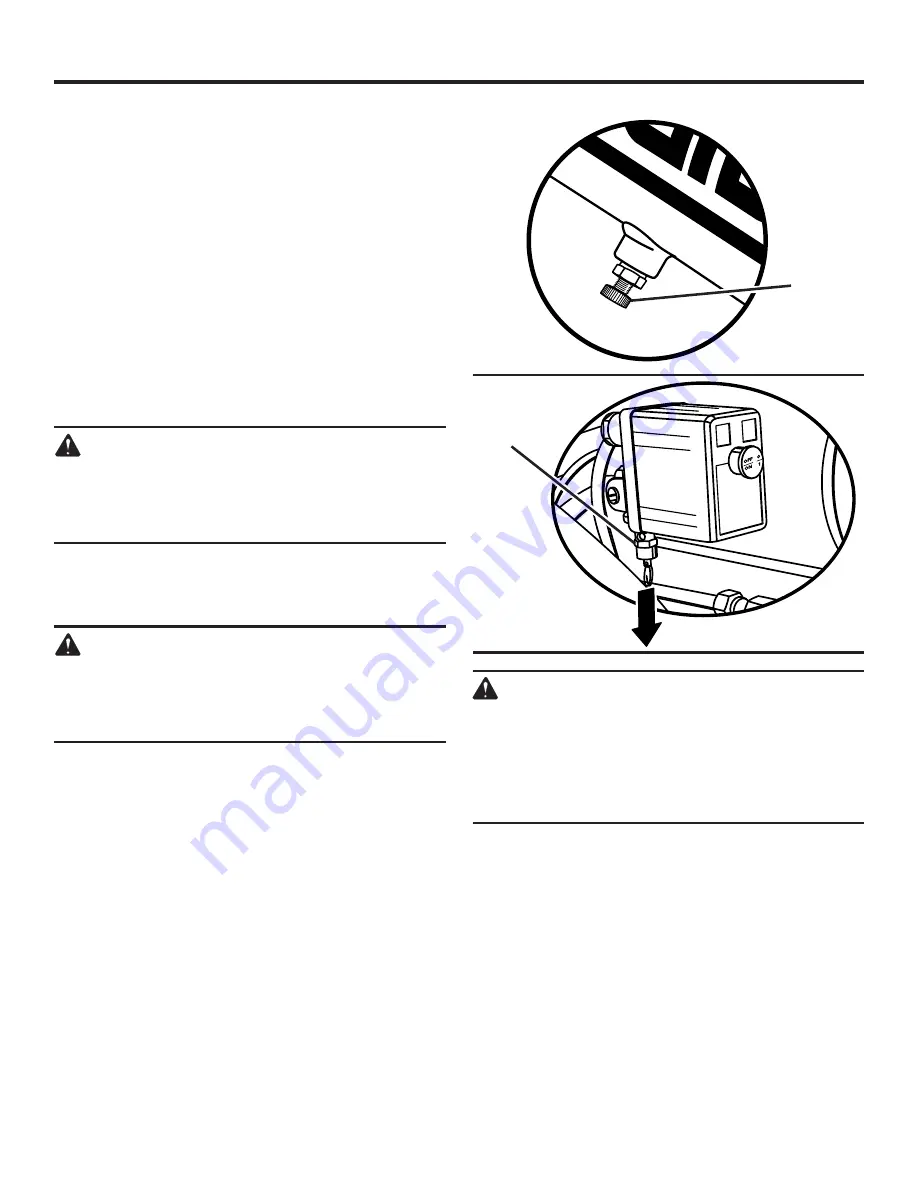
14
15
WARNING:
If air leaks after the ring has been released, or
if the valve is stuck and cannot be actuated by
the ring, Do not use the air compressor until
the safety valve has been replaced. Use of the
air compressor in this condition could result in
serious personal injury.
DRAINING THE TANKS
See Figure 12.
To help prevent tank corrosion and keep moisture out of the
air used, the air tanks of the compressor should be drained
daily.
NOTE: The air compressor has two separate tanks: an upper
tank and a lower tank. Be sure to open drain valves for both
and perform this operation for both tanks.
To drain:
n
Rotate drain valves counterclockwise to open.
n
Drain moisture from tanks into a suitable container.
NOTE: Condensate is a polluting material and should be
disposed of in compliance with local regulations.
n
If drain valves are clogged, release all air pressure, remove
and clean valves, then reinstall.
WARNING:
Unplug the air compressor and release all air from
the tanks before servicing. Failure to depressurize
tanks before attempting to remove valve may
cause serious personal injury.
n
Rotate drain valves clockwise until tightly closed.
CHECKING THE SAFETY VALVE
See Figure 13.
DANGER:
Do not attempt to tamper with the safety valve.
Anything loosened from this device could fly up
and hit you. Failure to heed this warning could
result in death or serious personal injury.
The safety valve will automatically release air if the air re-
ceiver pressure exceeds the preset maximum. The valve
should be checked before each day of use by pulling the
ring by hand.
n
Turn the air compressor on and allow the tanks to fill. The
compressor will shut off when the pressure reaches the
preset maximum.
n
Turn the air compressor off.
n
Pull the ring on the safety valve to release air for three to
five seconds.
n
Release the ring. Air must immediately stop escaping
when the ring is released. Any continued loss of air after
releasing the safety valve ring indicates a problem with
the safety valve. Discontinue use and seek service before
continued use of the air compressor.
Fig. 12
Fig. 13
SAFETY
VALVE
TANK
DRAIN
VALVES (2)
OPERATION
Summary of Contents for OL50135W
Page 20: ...20 NOTES ...