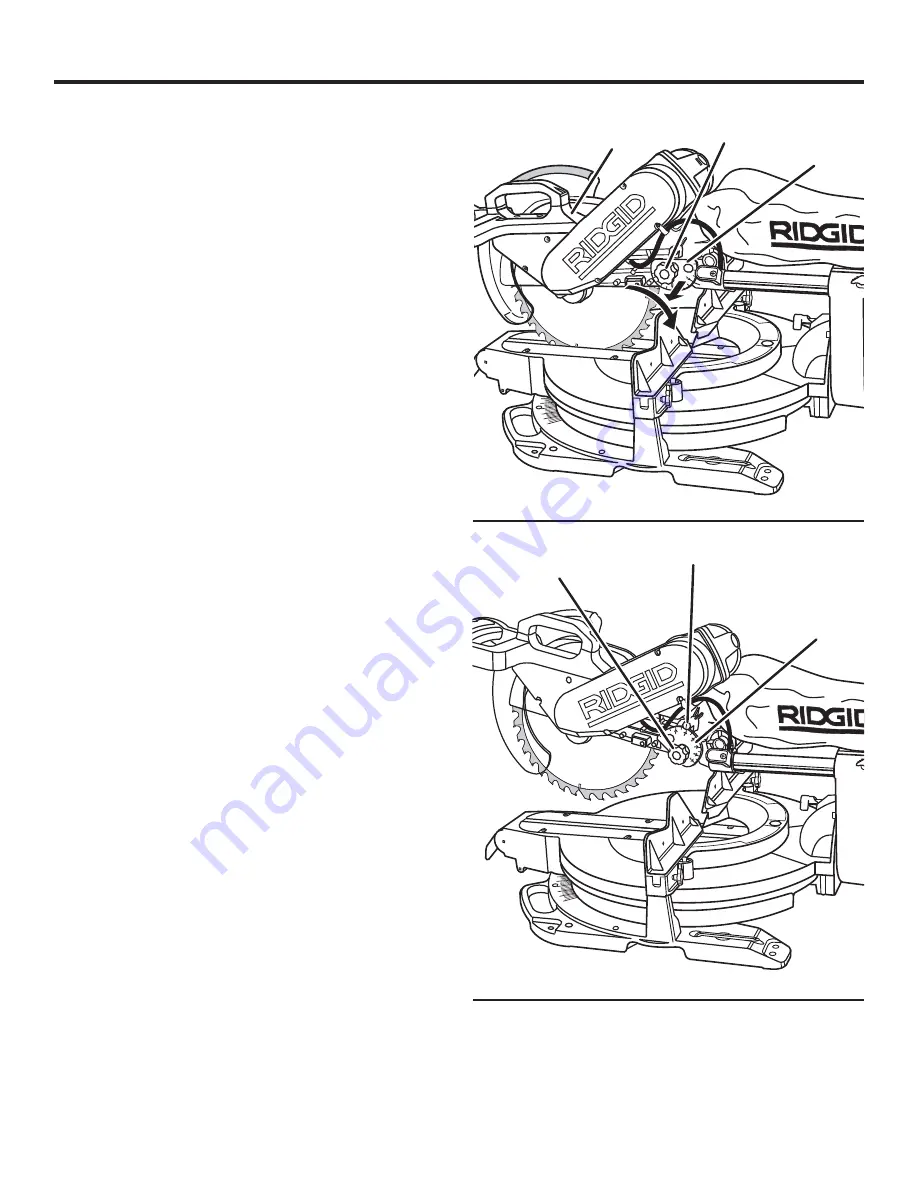
16
ASSEMBLY
Fig. 9
NOTE:
Many of the illustrations in this manual show only
portions of the compound miter saw. This is intentional
so that we can clearly show points being made in the
illustrations.
Never operate the saw without all guards
securely in place and in good operating condition.
LOCKING / UNLOCKING THE SAW ARM
See Figure 9.
When locking and unlocking the saw arm, it is not necessary
to loosen the depth control knob.
To unlock and raise the saw arm:
Firmly grasp the “D” handle and apply downward pres-
sure while at the same time pulling the depth guide out
and away from the saw housing.
Turn the guide to the right until the flat of the guide is
facing up.
Release the guide and slowly raise the saw arm.
To relock the saw arm:
Firmly grasp the “D” handle and apply downward pressure
while at the same time pulling the depth guide out and
away from the saw housing.
Turn the guide to the left until the hole in the guide is
positioned over the lock pin.
Release the guide allowing the lock pin to align with the
hole
in the guide.
Check that the slide lock knob is locked in place by
turning the knob clockwise.
USING THE DEPTH GUIDE
See Figure 10.
When used, the depth guide limits the downward travel of the
blade when cutting dadoes and other non-through cuts.
Make a mark on the lock pin with a pencil for use with the
scale on the guide. “A” on the guide represents the saw
blade teeth being level with the miter table. Each mark on
the depth guide is approximately 1/4 in. Always make a
practice cut on scrap wood. With the flat side of the guide
facing up, the saw can be used without any interference
from the guide.
To use the depth guide:
If the saw is in storage or transport position, unlock the
saw arm.
Position the depth guide by turning until it engages the
internal locking mechanism.
Loosen the depth control knob (turn knob counter-
clockwise).
Determine the desired depth of cut, set the guide to that
mark, and retighten the depth control knob (turn knob
clockwise).
NOTE:
To override the depth setting, pull the depth gauge
out and away from the saw housing and turn the guide until
the flat of the guide is facing up.
Fig. 10
SAW ARM
DEPTH
GUIDE
DEPTH CONTROL
KNOB
DEPTH
GUIDE
LOCK PIN
DEPTH CONTROL
KNOB