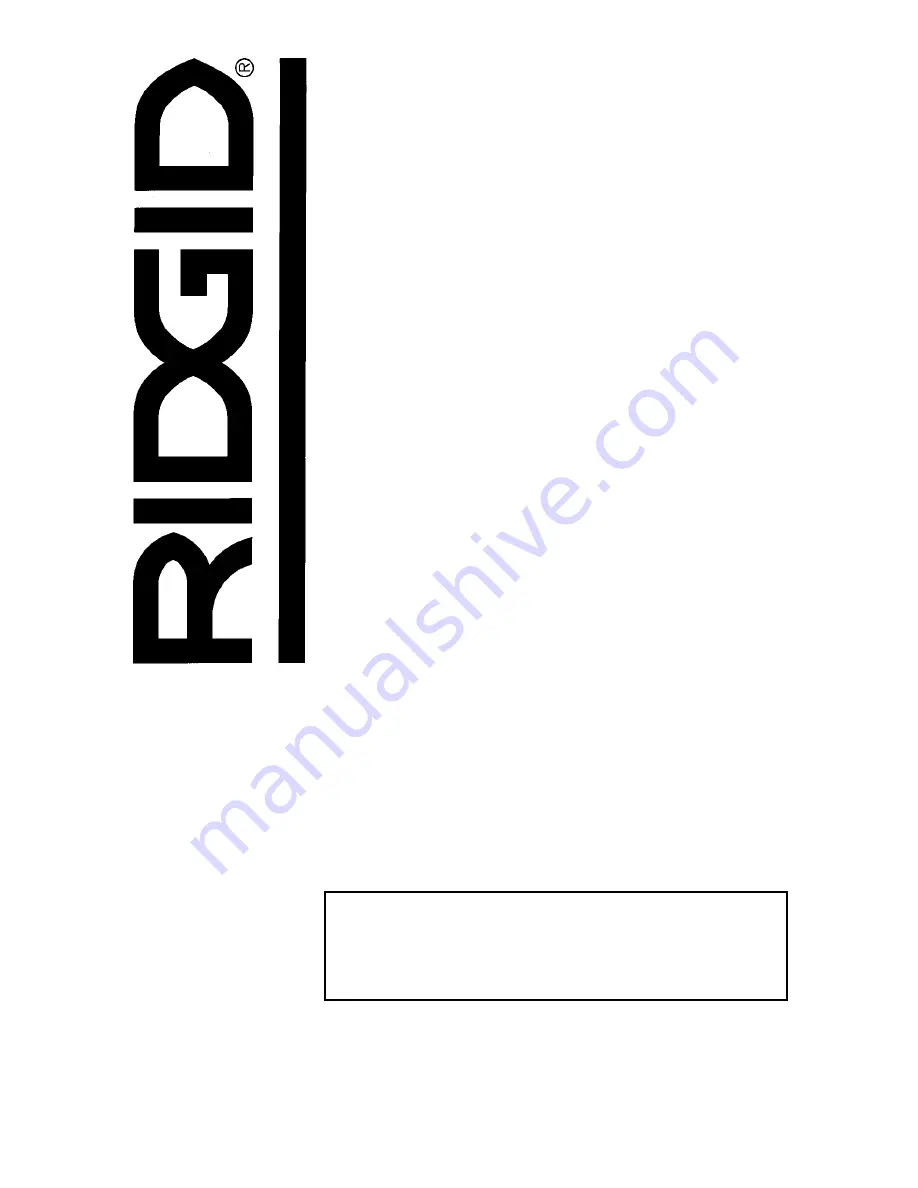
QUESTIONS OR COMMENTS?
CALL 1-866-539-1710
www.ridgidwoodworking.com
Please have your Model Number and Serial
Number on hand when calling.
© 2003 RIDGID,INC.
This product is manufactured under license from Ridgid, Inc. by One World
Technologies, Inc.. All warranty communications should be directed to One
World Technologies, Inc. at (toll free) 1-866-539-1710.
90-Day Satisfaction GuaranteePolicy
During the first 90 days after the date of purchase, if you are dissatisfied
with the performance of this Ridgid® tool for any reason, you may return
the tool to the dealer from which it was purchased for a full refund or
exchange. To receive a replacement tool you must present proof of pur-
chase and return all original equipment packaged with the original product.
The replacement tool will be covered by the limited warranty for the bal-
ance of the three year warranty period.
What is covered under the Limited Three Year Warranty
This warranty covers all defects in workmanship or materials in this
RIDGID® tool for the three year period from the date of purchase. This war-
ranty is specific to this tool. Warranties for other RIDGID® products may
vary.
How to obtain service
To obtain service for this RIDGID® tool you must return it, freight prepaid, to
an authorized RIDGID® service center for hand held and stationary power
tools. You may obtain the location of the authorized service center nearest
you by calling (toll free) 1-866-539-1710 or by logging on to the RIDGID®
website at www.ridgidwoodworking.com. When requesting warranty ser-
vice, you must present the proof of purchase documentation, which
includes a date of purchase. The authorized service center will repair any
faulty workmanship, and either repair or replace any defective part, at our
optioon at no charge to you.
What is not covered
This warranty applies only to the original purchaser at retail and may not be
transferred. This warranty only covers defects arising under normal usage
and does not cover any malfunction, failure or defect resulting from misuse,
abuse, neglect, alteration, modification or repair by other than authorized
RIDGID® service center for hand held and stationary power tools. One
World Technoligies, Inc. makes no warranties, representations or promises
as to the quality or performance of its power tools other than those specifi-
cally stated in this warranty.
Additional Limitations
To the extent permitted by applicable law, all implied warranties, including
warranties of MERCHANTABILITY or FITNESS FOR A PARTICULAR PUR-
POSE, are disclaimed. Any implied warranties, including warranties of mer-
chantability or fitness for a particular purpose, that cannot be disclaimed
under state law are limited to three years from the date of purchase. One
World Technologies, Inc. is not responsible for direct, indirect, incidental or
consequential damages. Some states do not allow limitations on how long
an implied warranty lasts and/or do not allow the exclusion or limitation of
incidental or consequential damages, so the above limitations may not
apply to you. This warranty gives you specific legal rights, and you may
also have other rights which vary from state to state.
RIDGID® HAND HELD AND STATIONARY POWER TOOL
LIMITED THREE YEAR WARRANTY AND
90 DAY SATISFACTION GUARANTEE POLICY
Part No. SP6496
Form No. SP6496
Printed in Taiwan 4/03
Catalog No. EB4424
Model No. EB44241 Serial No. ________
The model and serial numbers may be found on the back side
of the base. You should record both model and serial number in
a safe place for future use.
Summary of Contents for EB4424
Page 1: ...OSCILLATING EDGE BELT SPINDLE SANDER ...
Page 35: ...35 Notes ...